Fine-tuned coatings
Today, many industries use laser cladding to coat metal parts in order to make them more wear and corrosion resistant. Together with the industrial partner OC Oerlikon, ETH Zurich develops methods to fine-tune the coating properties. Jona Engel shows first promising results.
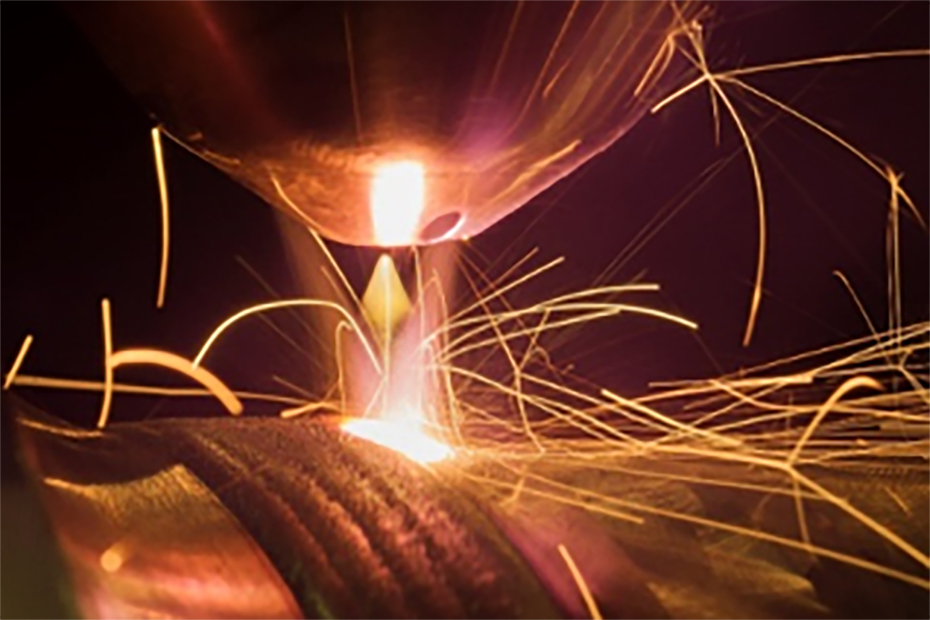
What are the latest trends in laser cladding?
Current applications of laser cladding are e.g. the coating of machine parts in mining and construction, as well as the repair of pumps and turbine blades. Embedding carbide particles into the laser cladding is a new process that improves the performance of the coating and enables new material combinations e.g. with the toughness of high-performance alloys (super alloys) and the hardness of carbides and hard-metals. Another advantage of laser cladding compared to conventional welding is the robust automation of the process. Our industrial partner Metco from OC Oerlikon wants to broaden the field of possible applications of this process and to fine-tune the achieved properties. For this, a better understanding of the laser cladding process is necessary.
Laser cladding creates a metallurgical bond while minimizing the heat-affected zone (Courtesy of Oerlikon Metco).

How do you achieve a better understanding of the laser cladding process?
We need three things:
- Simulations that predict what happens during the process
- Experiments that validate the simulations
- Benchmark testing of the part performance
Here at ETH Zurich, we have the unique possibility to do joint research in all three areas. My colleagues from the Institute of Machine Tools and Manufacturing have expertise in mechanical engineering and take care of the simulations. I am part of the Laboratory for Nanometallurgy and have a background in materials science. In my experiments, I use advanced technologies to characterize the coating material and to analyze how the whole part performs. Oerlikon Metco appreciates this interdisciplinary approach and has collaborated with our group for many years.
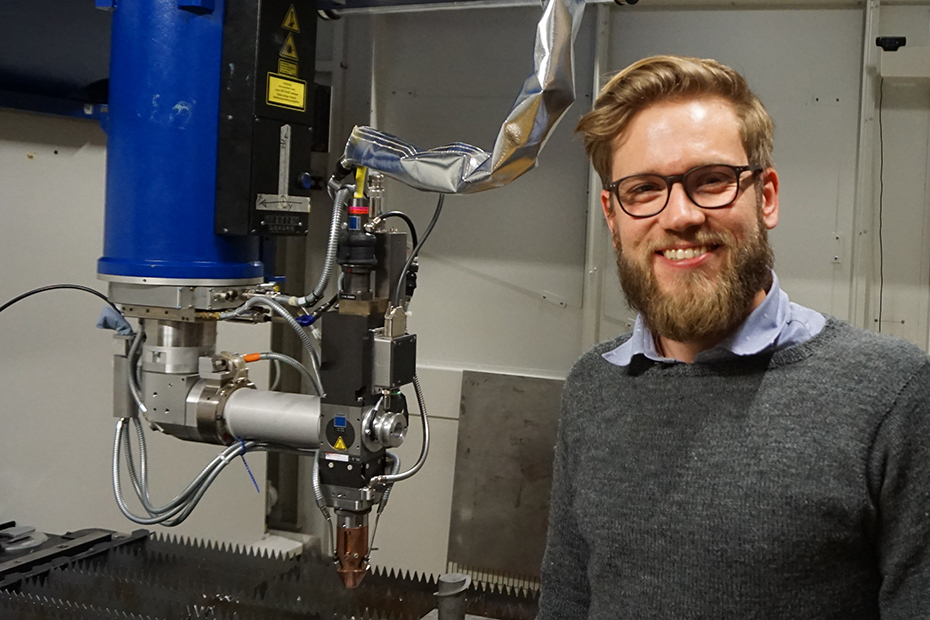
What kind of advanced technology do you apply for your experiments?
By using electron microscopes and in-situ testing, we can see much more details in the microstructure of the coating. We found out that parts that appear to be similar after the first simple tests are actually quite different if we look closer. Our analyses reveal how the differences on the microscopic level lead to different material and part performances. In materials, performance depends directly on the microstructure. We change the coating properties in two ways. Firstly, we investigate new material combinations. Secondly, we alloy the feedstock material at very high heating and cooling rates in the laser cladding process and are able to reach unprecedented microstructural features. With small-scale and in-situ mechanical testing, we can find the properties of all phases and optimize the processes in terms of performance. My colleagues use these experimental results to improve the simulations.
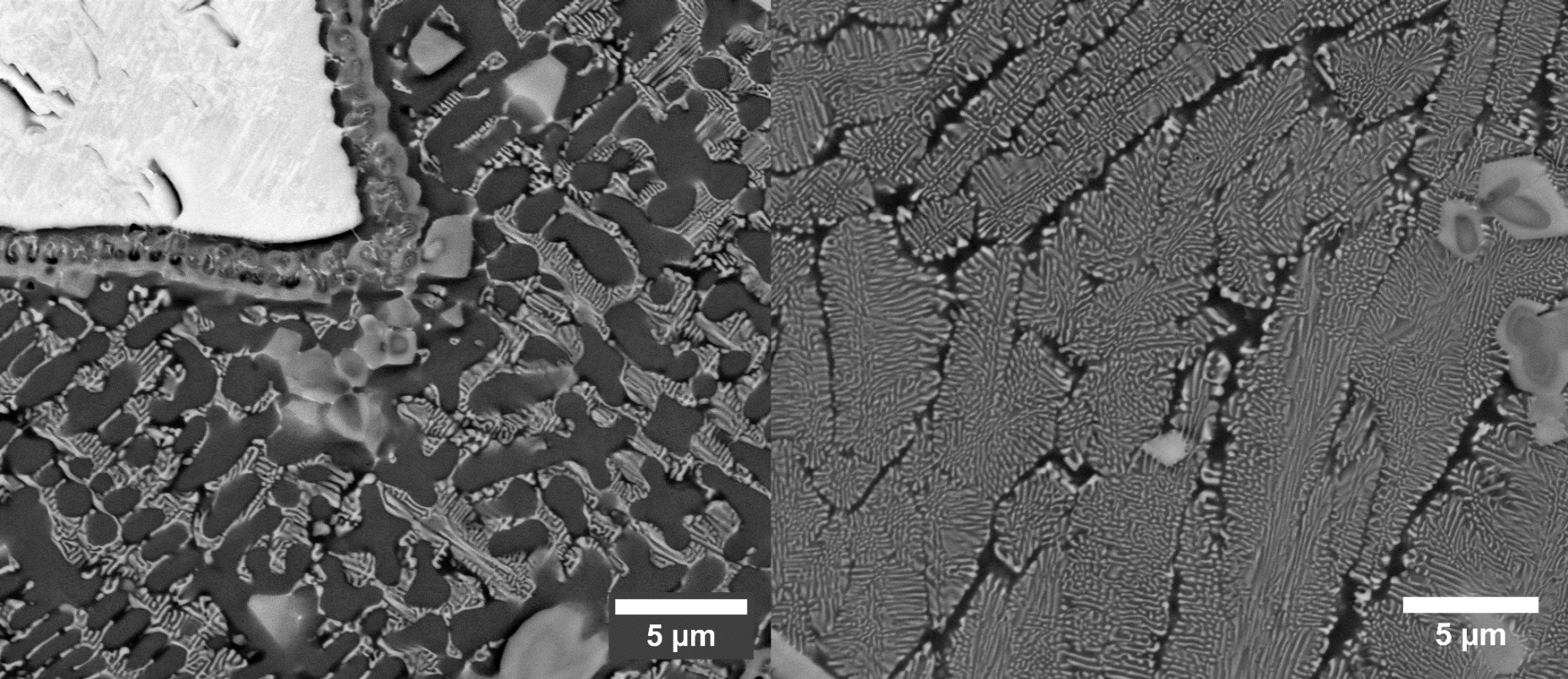
How can you fine-tune the coating properties?
In the laser cladding process, we can design the material properties by using the laser as a local heat source. By adjusting the process parameters, we can guide a heat flow through the work piece. This way, we can control how much the embedded hard particles dissolve and what kind of microstructure develops in the matrix. A great advantage of laser cladding is the fast processing that allows to process the material far away from equilibrium. This fast processing window gives us many opportunities to tune the microstructures and the final properties of the material. In short: We shift the current focus in additive manufacturing from geometry to local properties.
What are the next steps?
We have now coated first parts on an industrial scale, like e.g. large pipes and rolls for rolling mills. The next step will be to test the coated parts for specific applications. With these results, our partner Oerlikon Metco will be able to offer a wide variety of coating solutions tailored to specific applications.
Contact / Links:
Jona Engel, ETH Laboratory for Nanometallurgy
OC Oerlikon external pagewww.oerlikon.com/metcocall_made
Do you want to subscribe to ETH News for Industry?
external pageSubscribe to our newslettercall_made
Are you looking for research partners at ETH Zurich?
Contact ETH Industry Relations