Cooling of milling machines
The cooling of heavily-stressed machine parts like spindles is a challenge – especially when high speed and high precision are required. inspire (competence center and strategic partner of ETH Zurich) has carried out a project with industrial and academic partners to tackle this challenge. Read the interview with Lukas Weiss (inspire).
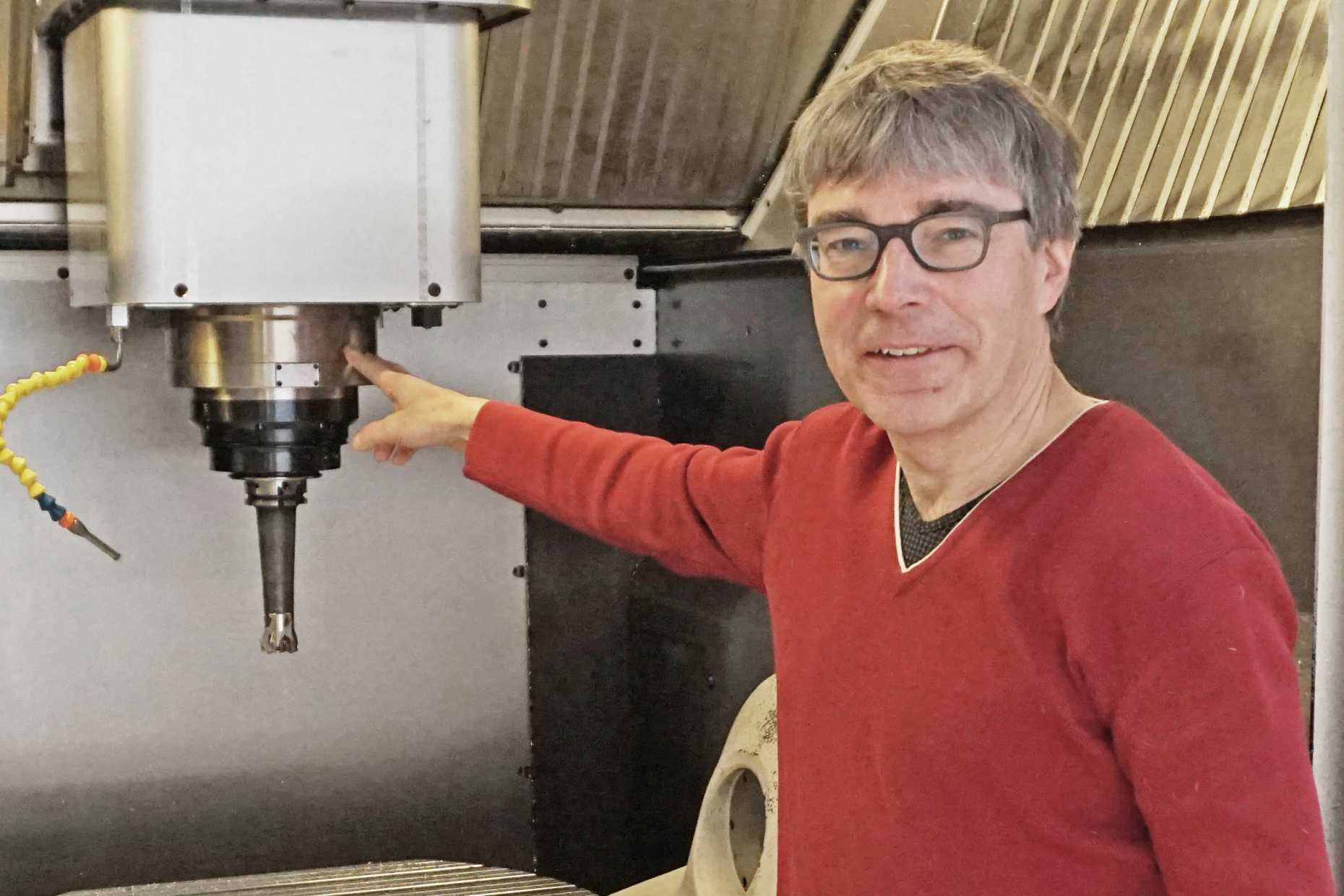
Why is cooling so important and challenging in modern milling machines?
The customers demand machines for high-speed milling of tough materials with high accuracy. This poses grand challenges on the design of the cooling systems, especially of the spindle, which is the rotating axis of the machine. The spindle has a frequently changing speed of up to 42’000 rpm that results in complex thermal loading. At the same time, the center point of the tool must be stabilized in the micrometer range. This is only possible with an even and stable temperature distribution within the spindle. Our goal is to optimize the cooling of the spindle and limit the temperature differences to 1°C.
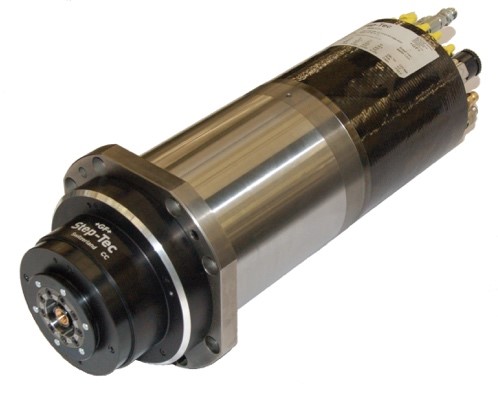
How can you improve the cooling of the spindles?
One of the core competences of inspire is the development of simulation tools. We established a platform for physical and thermal simulations and fine-tuned it for the spindle application. We work together with the Competence Center for Thermal Energy Storage of HSLU who are experts in phase-change materials (PCM). The idea is to use PCM in the spindle to minimize the temperature differences. We approached the company Step-Tec (Georg Fischer), a producer of spindles, and they were so excited about this idea that we carried out a joint project.
What are the achievements of this collaboration?
Regarding the simulation tool, the main achievement was the reduction of calculation time. Our tool only needs 1 second instead of 1 hour, which is common for commercial tools. Thanks to our new tool, we were able to optimize the cooling channel geometry of the spindle in an iterative approach by calculating thousands of varieties.
Our partners from HSLU developed a phase-change dispersion that can be pumped through the cooling circuit of the spindle. This special material can store heat and in this way cools the spindle during operation.
Altogether, we achieved the goal to limit the temperature differences in the spindle to 1°C.
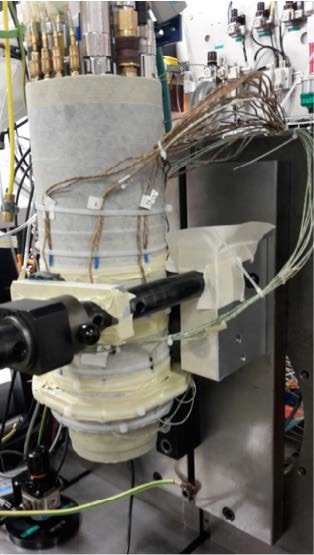
Has the company implemented your results?
Yes, Step-Tec implemented the simulation tool and built a spindle based on the new method. After successful tests and the market introduction of the first type, the company is developing now a complete new series of spindles.
The main prerequisite for such a successful commercialization was that we also considered economic aspects at an early stage of the project.
Will you continue working on this topic?
Currently, we have on-going discussions with several companies and are planning to continue this work. We have plenty of ideas on how to further optimize cooling circuits. We believe that our approach has a huge potential, also for other applications.
Contact / Links:
Lukas Weiss, inspire
Prof. Ludger Fischer, external pageHSLUcall_made
Download DownloadProject Report DeltaZero4PSP (PDF, 878 KB)vertical_align_bottom (German)
Do you want to subscribe to ETH News for Industry?
external pageSubscribe to our newslettercall_made
Are you looking for research partners at ETH Zurich?
Contact ETH Industry Relations