Paradigm shift in clamping technology
Clamping workpieces efficiently in machines is challenging and will become even more difficult with increasing automation and additive manufacturing of free-form surfaces. In cooperation with inspire and ETH Zurich, the Gressel company has found an innovative solution with some surprising benefits.
Lukas Weiss (manager machine concepts at inspire) gives an insight into the project.
What is the challenge when clamping workpieces?
Conventional clamping between two clamping jaws has various disadvantages:
- Deformation of the workpiece
- Loss of material (added material for clamping, so-called clamping loss)
- Limited accessibility
- Difficulty with free-form surfaces and automation
Gressel had an idea that looked simple on first sight but, as so often, the evil lay in the detail.
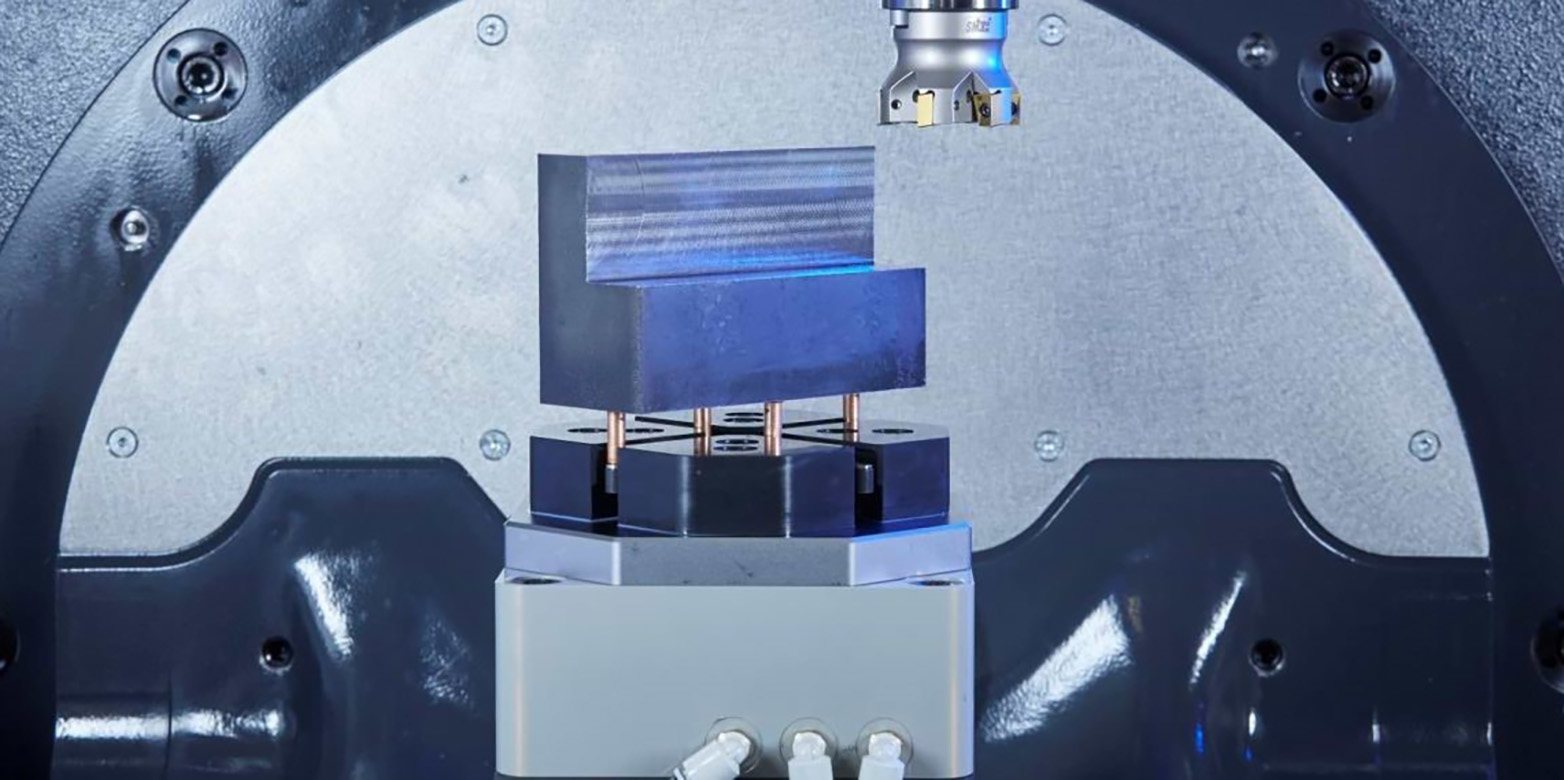
What is innovative about the idea and what are the difficulties?
Gressel’s idea is to weld small steel bolts to the workpiece to help clamping them. The benefit here is that the bolts always look the same regardless of the workpiece geometry and thus represent a universal handling interface. The challenge was to implement this idea cost-effectively and reliably (i.e. with a zero-defect tolerance). This includes the bolt dimensions, the choice of material and the evaluation of the welding process. In addition, the entire production must be analysed: How does this type of clamping change the production process? What are the requirements to make this profitable?
Gressel decided to cooperate with inspire in order to approach the problem in a holistic and scientifically sound way.
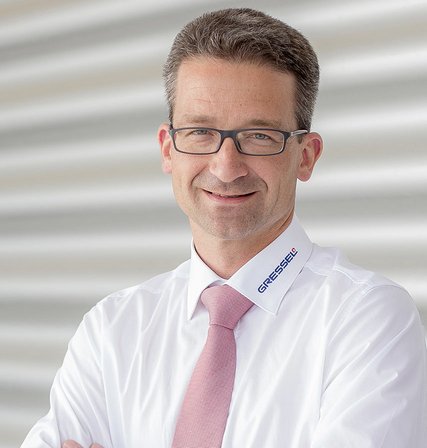
Marcel Schlüssel (Gressel):
“inspire and ETH Zurich thought outside the box when it came to solving the problem. The ideas and proposed solutions resulting from the project cooperation inspired us to create new products.”
What was the result of this cooperation?
The project showed that this clamping method works and that it avoids all the disadvantages of conventional clamping. It was particularly important to prove the reliability of the bolt welding. This method is already established in sheet metal processing but we used various other materials in this project (steel, aluminium, alloys). By using a semi-automatic CNC bolt welding station, it was possible to guarantee high dimensional accuracy and high-quality joints.
The simulation of the effects of the bolt position on the workpiece and the design of the clamping jaws delivered further important results. All results were validated in the field, tested by pilot users and are filed for patent.
What are the (partly unexpected) benefits of the new method?
With this method, a wide range of workpieces can be clamped precisely, reproducibly, reliably, and economically. Resource efficiency is a major added value as there is no more clamping loss.
In addition, we have identified another huge advantage that we did not have in mind at the beginning: The new clamping technology is very attractive for automation. Thanks to the new technology, a universal gripper is used for robot-supported automated part production. Moreover, standard trays are used instead of numerous part-specific pallets. This simplifies the handling of workpieces and is more cost-effective.
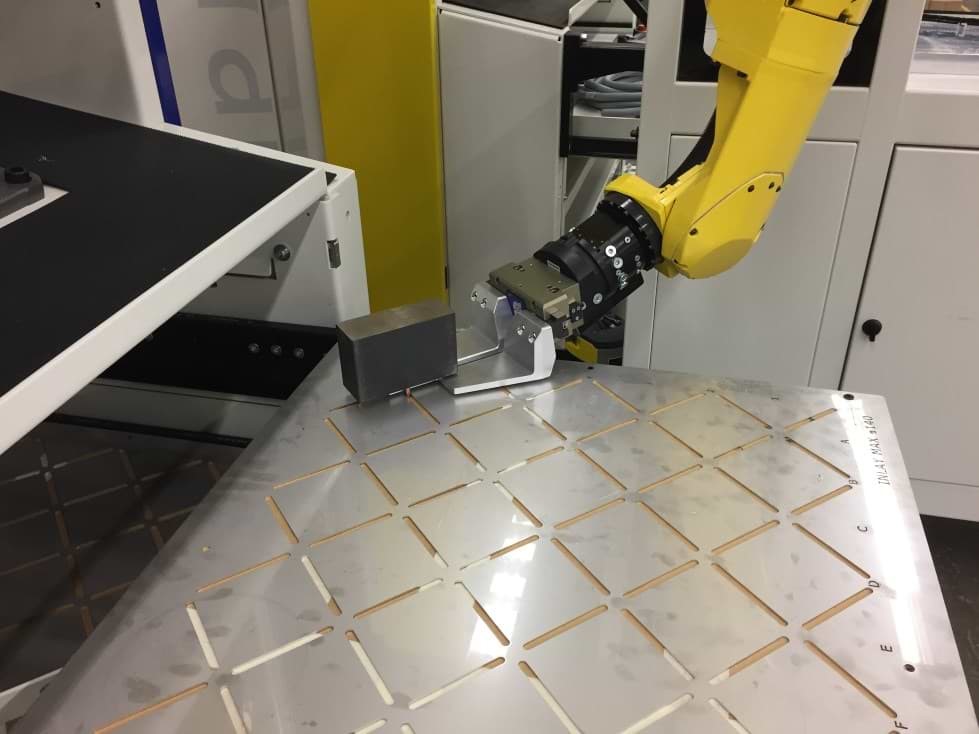
Where to from now?
Gressel has already launched the new clamping technology on the market and thus initiated a paradigm shift in the industry.
In cooperation with ETH Zurich, Gressel is involved in a follow-up project in the field of additive manufacturing. Prof. Meboldt’s inspire team (pd | z Product Development Group Zurich) is investigating the use of the new clamping technology for additively manufactured components. It is difficult to clamp free-form surfaces with previous clamping methods whereas this new method could be a solution for the future.
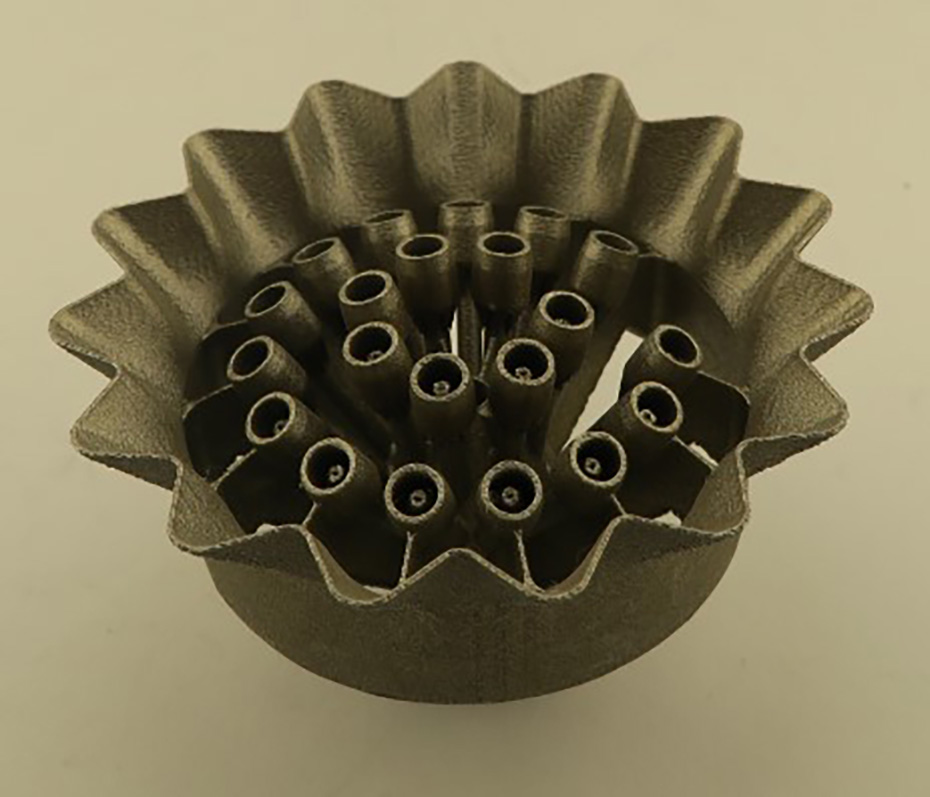
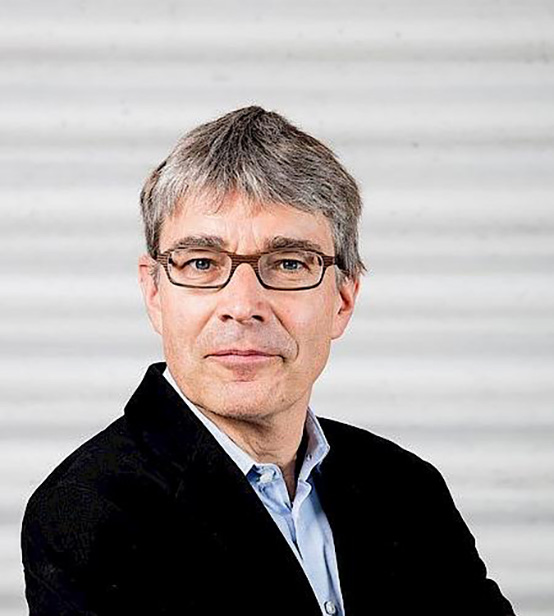
Lukas Weiss (inspire):
“It is a particular challenge to question the obvious such as the well-established clamping technology. The practical relevance helped to involve students in the process.”
Contact / Links:
Lukas Weiss, inspire
Do you want to get more "News for Industry" stories?
external pageSubscribe to our newslettercall_made
external pageFollow us on LinkedIncall_made
Are you looking for research partners at ETH Zurich?
Contact ETH Industry Relations