Robotic production of large-scale components
ETH spin-off SAEKI’s ground-breaking robot is revolutionising the manufacturing of large components for space shuttles and concrete structures. This all-in-one machine handles everything from 3D printing to milling, saving costs, time, and materials. Welcome to the future of manufacturing.
We talked to Matthias Leschok, co-founder of SAEKI.
Why is it so difficult to manufacture formwork for a large concrete part in a building or a mould for the hull of a space shuttle?
There are several aspects to this problem. First, the manual labour required to fabricate those elements is high, making it expensive and time-consuming. Second, there is a labour shortage of skilled craftsmen qualified to fabricate high-precision and/or complex shape elements.
Therefore, SAEKI provides a one-stop-shop digital manufacturing solution for the small-batch production of large-sized parts. Our solution essentially provides a micro-factory with a new way of manufacturing complex elements at competitive prices with increased speed.
The tool-head we developed is about 1.5m tall and quite powerful, specially made for large-scale components. Furthermore, our clients may use our patented printing technology to produce lightweight elements at an increased speed.
Our robot can produce full-circle components, from 3D printing to milling and sanding. SAEKI combines robotics, 3D printing, milling, post-processing, and 3D scanning for large-scale components.
How does the technology work?
The technology enables switching back and forth between the different tools when working on a product, which is much more efficient and means the product doesn’t have to be moved. Depending on the component, we can produce large elements five times faster than other manufacturers.
Having a patent for a novel 3D printing technology, we can print objects such as formwork or interior elements up to 10 times faster with less material.
Our process starts with additive manufacturing in large dimensions. Then we subtract material with the milling tool to carve and form the parts in the correct shape. We also intend to integrate post-processing solutions, including a wide range of coatings, spraying, sanding, or inserting components into a print – all during manufacturing. In the future, we will integrate quality control inspections, to provide an all-in-one manufacturing solution.

SAEKI’s full-circle component production (source: SAEKI)
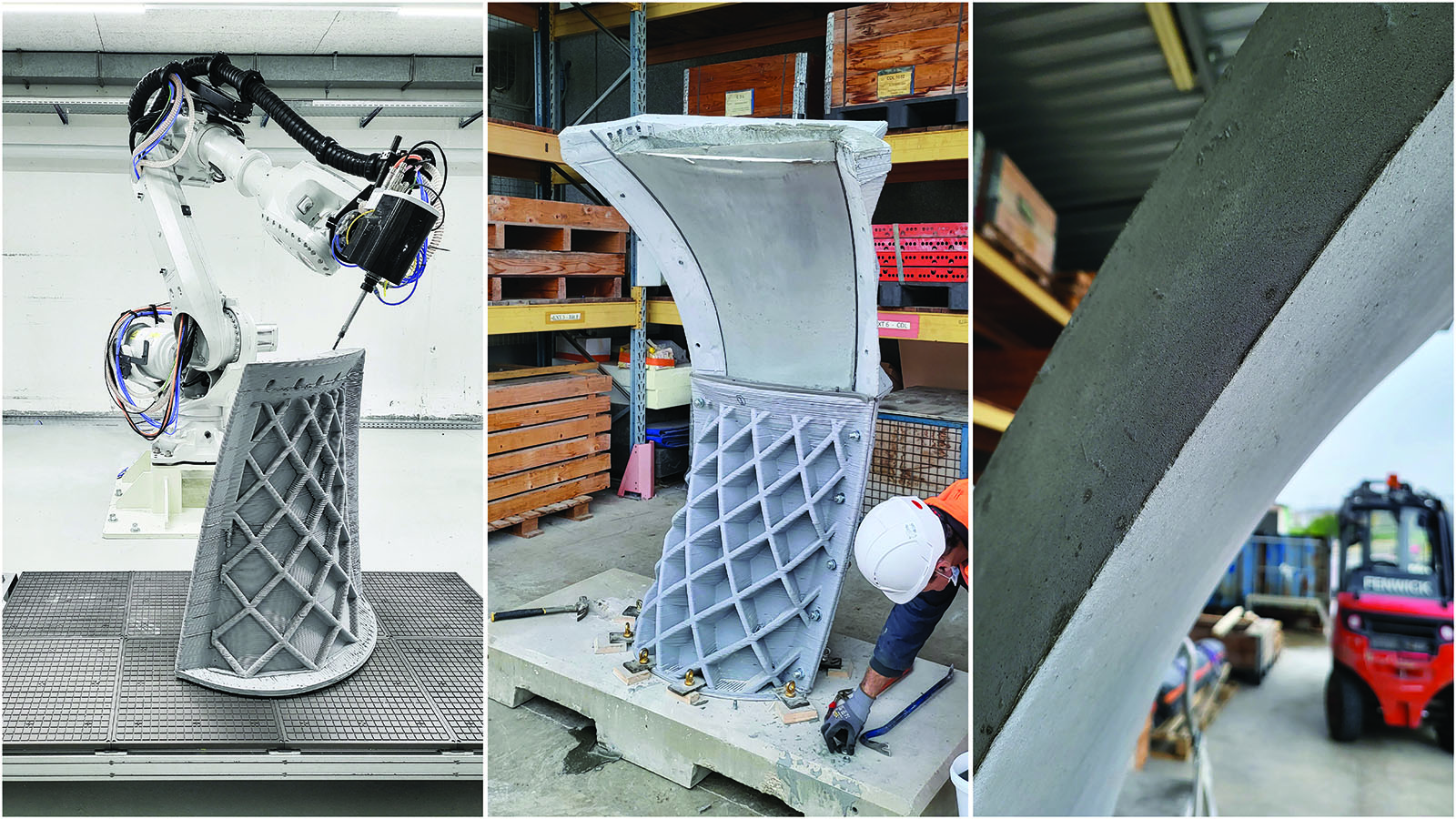
What sets you apart compared to similar solutions?
We can offer the complete hardware and software automation package, consisting of the tools and material required for RDM, control, and design software.
A clear differentiating factor lies in enabling circular production: any waste products generated can be recycled. Concrete formwork, for example, can be reused, rather than discarded.
Furthermore, we will provide decentralised production hubs for large-scale components, fabricated close to where they are needed. Currently, we are setting up our first Hub of micro-factories.
What is planned in the near future and what is your vision?
At the moment, we are looking for more projects and collaborations within the industry to offer our solution. We just closed our pre-seed round and are looking for more team members in all fields of engineering.
Ten years from now, we envision lights-out factories filled with SAEKI micro-factories. They will be autonomously producing complex, material and weight-saving formwork for the construction industry, fixtures, and tooling for super-sonic jets, or composite moulds for the next generation of Formula 1 cars.
“We are thrilled to have teamed up with Andrea, Oliver and Matthias on their mission to make large-scale manufacturing fast, cheap, and sustainable by leading their pre-seed round. SAEKI’s groundbreaking approach to distributed additive manufacturing has the power to revolutionise a vast number of sectors, be it aerospace, automotive and construction”Edouard Treccani, Principal at Wingman Ventures
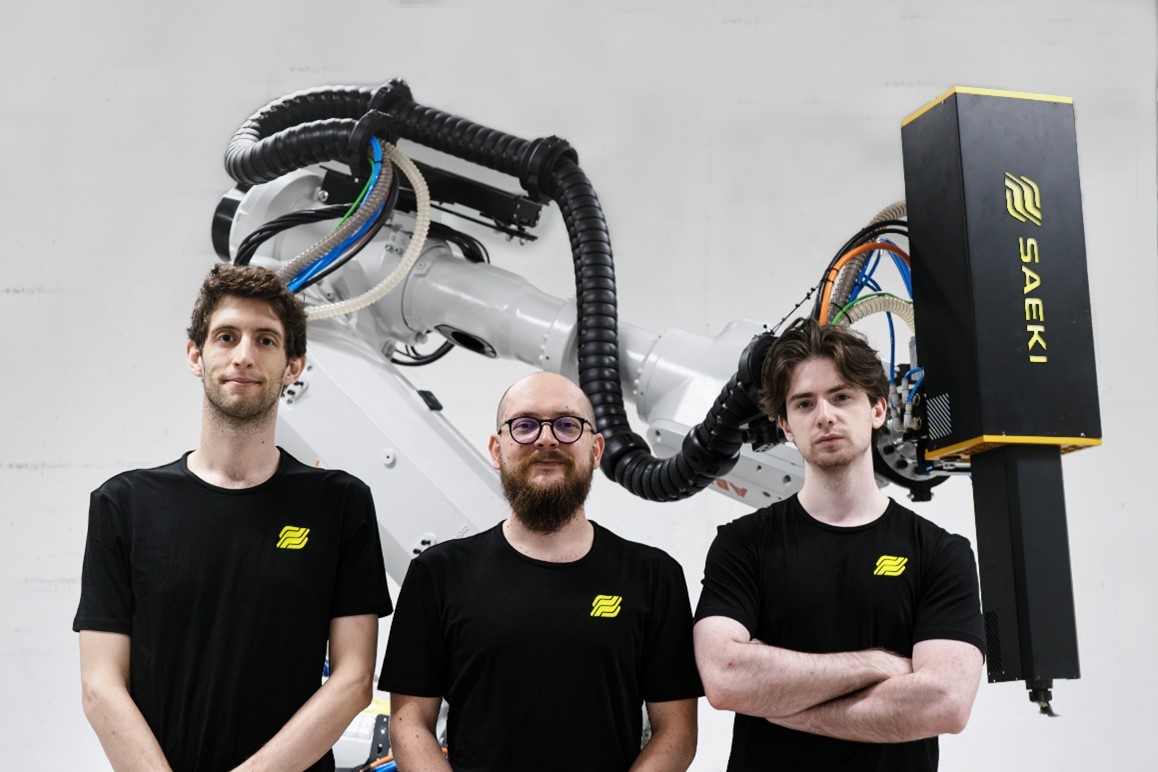
Contact/Links:
Do you want to get more "News for Industry" stories?
external pageFollow us on LinkedIn
Are you looking for research partners at ETH Zurich?
Contact ETH Industry Relations
ETH spin-offs: facts and figures
Since 1973, 540 spin-offs have been founded at ETH Zurich. ETH transfer, the technology transfer office at ETH Zurich, supports recognized ETH spin-offs in the founding process and in their first years of operation.
With the help of the Pioneer Fellowship Programme, funded by the ETH Foundation, young researchers can develop innovative products and services based on their scientific work at ETH Zurich. A Pioneer Fellowship is awarded to young ETH entrepreneurial minds intending to develop a highly innovative product or service to be exploited commercially and/or for the benefit of society.
Offers for entrepreneurs at ETH
Press release ETH spin-offs January 2023: Digital twins, new cancer treatments and three unicorns