A wooden dome made solely from waste
Catherine De Wolf firmly believes that digitalisation can help shift the construction industry towards a more circular economy. The assistant professor and her research group recently completed a hands-on project to illustrate how this could work.
- Read
- Number of comments
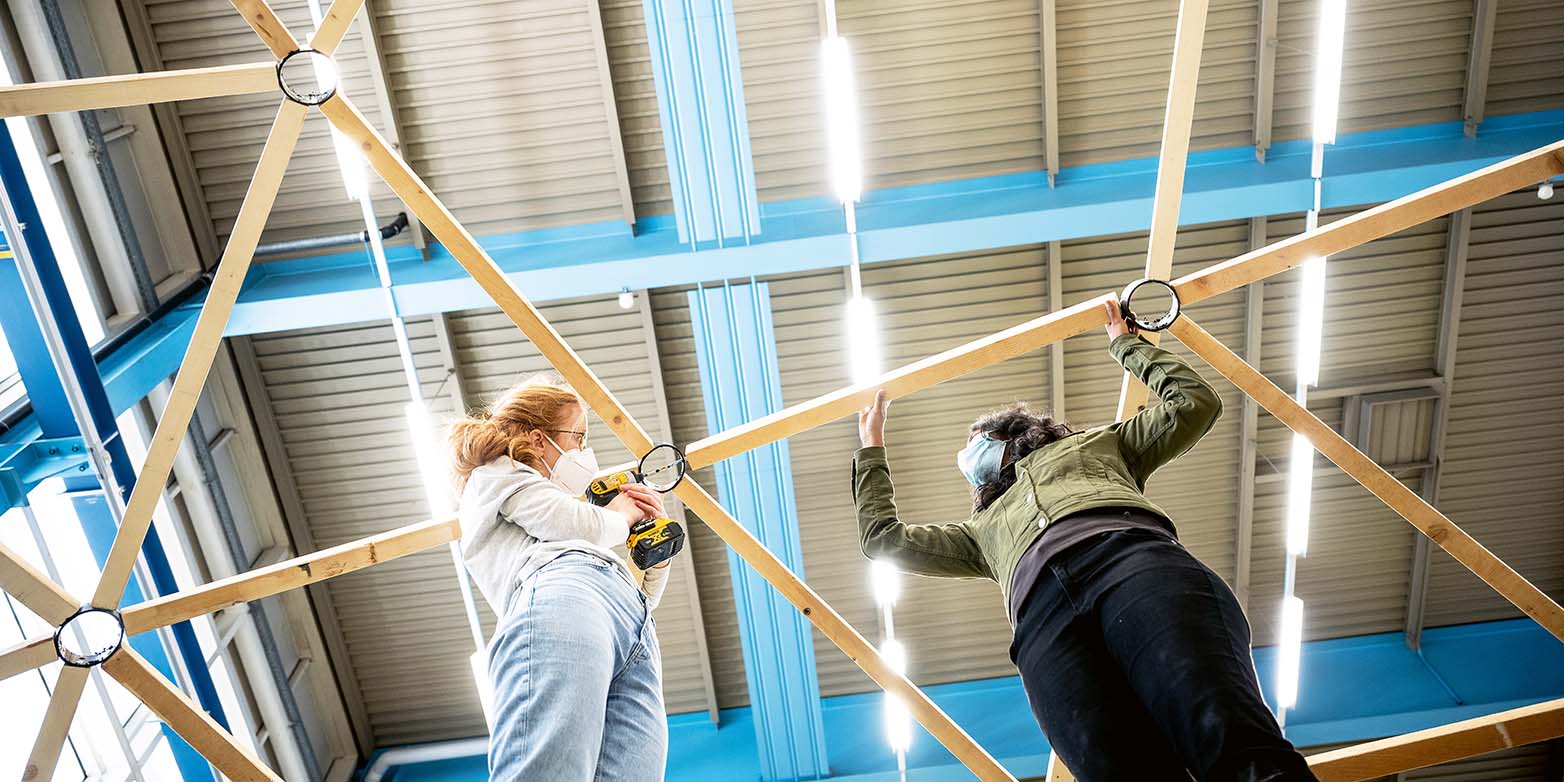
Strolling into the carpentry shop on the Hönggerberg campus on this January morning, you could be forgiven for thinking you’ve stumbled into a beginners’ woodworking course. Huddled around a bandsaw, six people are getting a quick tutorial on how to cut timber beams into rectangular struts. Once they’ve received their instructions, some get straight down to work, deftly guiding the timber past the saw blade. Others – clearly less confident – call on the instructor’s help to make sure they’re putting their hands in the right place.
Today’s team of woodworkers are part of the research group led by Catherine De Wolf, assistant professor in the Department of Civil, Environmental and Geomatic Engineering at ETH Zurich. This is the first time some of them have tried their hand at carpentry, but this crash course is essentially just a means to an end. The Circular Engineering for Architecture (CEA) lab members' real goal over the next four weeks is to construct a building from nothing but demolition waste. The end result will be a geodesic dome, and the first step is to cut the reused beams into the struts that will form the basic framework. “It’s fun working on a project together!” says doctoral student Deepika Raghu, explaining that she never had the opportunity to construct a building on such a large scale during her architecture degree programme.
The team began their work last October in an old car depot in Geneva that was scheduled for demolition. The ETH researchers had been given permission to salvage any materials they liked before the bulldozers moved in. Aided by deconstruction specialists, De Wolf and her three doctoral students dismantled an entire floor of the building. This yielded a rich haul of OSB panels, wooden beams, steel girders and some plastic piping, which they loaded into their minivan before heading back to Zurich.
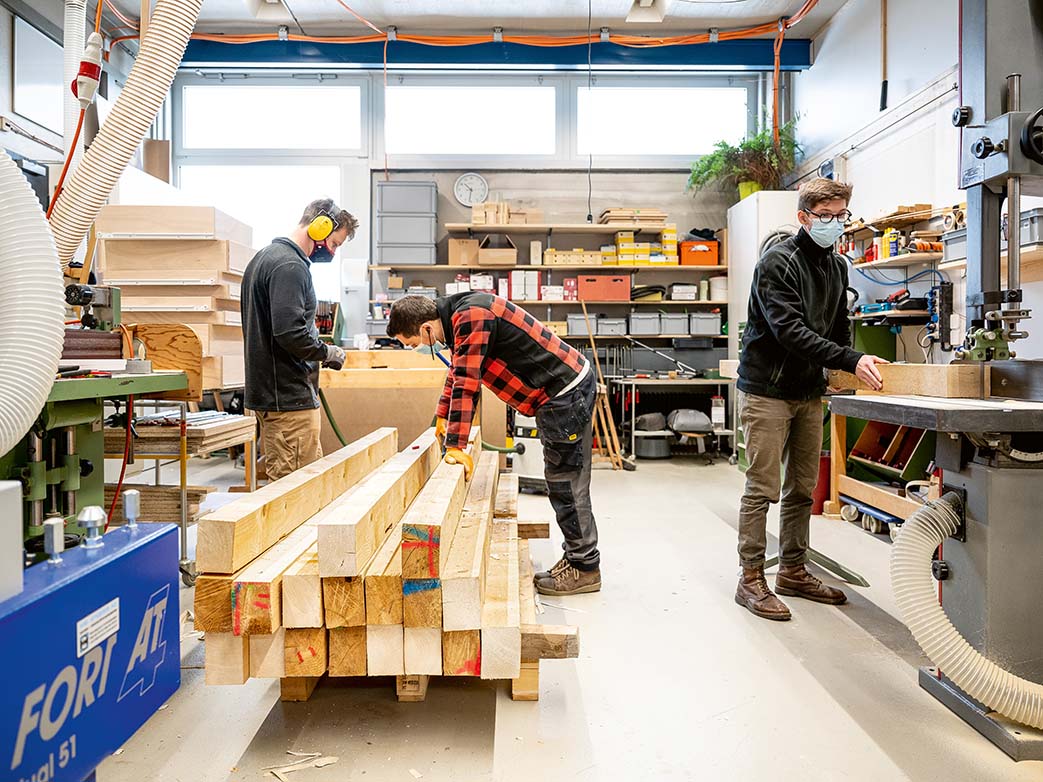
Aiming for sustainability
Assistant Professor De Wolf was part of that deconstruction crew, and she’s also on hand today to help with the carpentry. Right now, she’s moving a metal detector over a wooden beam to find any nails or other foreign objects that need to be removed before sawing. Material reuse and the principles of the circular economy lie at the heart of the 32-year-old Belgian’s work at ETH. But her decision to get involved in sustainable construction goes all the way back to her degree programme in architecture and civil engineering. In one of her first classes, says De Wolf, the lecturer revealed that the construction industry is the world’s biggest emitter of greenhouse gases. As a nature-lover, she found this shocking: “But then I decided I could play a big part in helping to change that."
“By carrying out every step in the process ourselves, we can build a clearer picture of where the challenges lie and identify the best solutions.”Catherine De Wolf
Now, more than a decade later, De Wolf firmly believes that achieving greater sustainability in the construction industry depends on exploring digital tools and technologies. Showing how and where digitalisation can add value is therefore one of the key goals of the dome project.
De Wolf wants all the members of her group to go through the whole lifecycle of use and reuse – from the deconstruction of the old to the design and construction of the new. “By carrying out every step in the process ourselves, we can build a clearer picture of where the challenges lie and identify the best solutions,” she says.
Missing beam
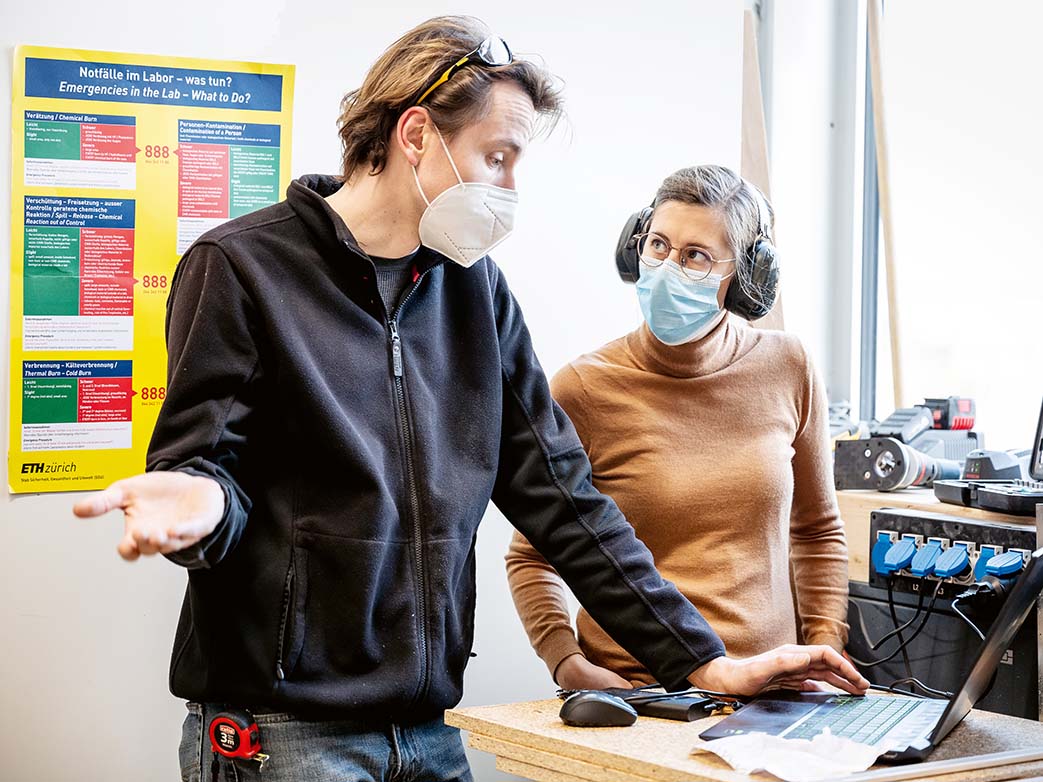
“Do we have enough beams?” At the back of the carpentry shop, De Wolf is studying the construction plans with doctoral student Matthew Gordon. Their decision to build a geodesic dome was a calculated one. With a basic structure composed of nothing but triangles, it’s one of the most space- and energy-efficient constructions they could have chosen, and it’s also extremely stable. But what’s special about this particular dome is that it uses wooden struts of varying lengths to form the sides of the triangles, thereby making the most efficient use of the reused materials.
Gordon, who has a degree in digital fabrication, programmed an algorithm to calculate the optimum geometry and dimensions based on the available timber. “The aim was to create a programme that would avoid sawing the biggest beams into small pieces and that would use up as much of the wood as possible,” he says. Right now, he’s rechecking that the computer data on the wooden beams corresponds to the reality on the ground.
During their initial preparations, he noticed that some beams were missing. These had already been incorporated in the construction plans – so it was time for chief designer Gordon to put his computer programme’s flexibility to the test. He redid the calculations earlier this morning, and while the rest of the group was busy sawing up the beams, he labelled the new parts with the corresponding numbers from the plans. So far things seem to be back on track – another hurdle overcome.
Platform for reused materials
“That whole episode was a good example of how challenging it can be to work with reused materials,” says De Wolf wryly. The only space left to store the wooden beams had been outside the workshop, so someone had probably disposed of them by mistake. Similar problems abound in the construction industry, she says. Although more and more companies are trading in second-hand materials, getting hold of these can be costly and time-consuming, and storage space is often limited. “The ideal thing would be to tell companies about demolition projects well in advance, because then they could start hunting for buyers for the materials right away,” says De Wolf. In reality, however, they often get this information at short notice.
“During the pandemic, numerous construction projects were delayed by disruptions to global supply chains. That’s made the case for the circular economy even stronger.”Brandon Byers
But what if all the information on the materials in an existing building were available on a digital platform? That would mean architects could check the upcoming availability of materials from demolition projects and incorporate them in their plans for new buildings. “During the pandemic, numerous construction projects were delayed by disruptions to global supply chains. That’s made the case for the circular economy even stronger,” says doctoral student Brandon Byers, who has a degree in civil engineering.
His tasks in the dome project included the creation of an online platform for building materials. Using the example of the timber components, he gives us a quick demonstration of how information can be stored across multiple building cycles and updated as required. For this project, the doctoral student has created a table covering every stage of the timber’s life, including up-to-date information on its quality and dimensions, and the date and place each item was installed.
QR code on every piece of material
But the advantages of a digital material passport encompass more than just the practical side of construction, says Byers: “By making the information on a building’s materials freely accessible, we actually help people learn more about that building’s history.” To complete the loop, the ETH doctoral student has marked each piece with a clearly visible QR code that links directly to the corresponding material passport on the internet.
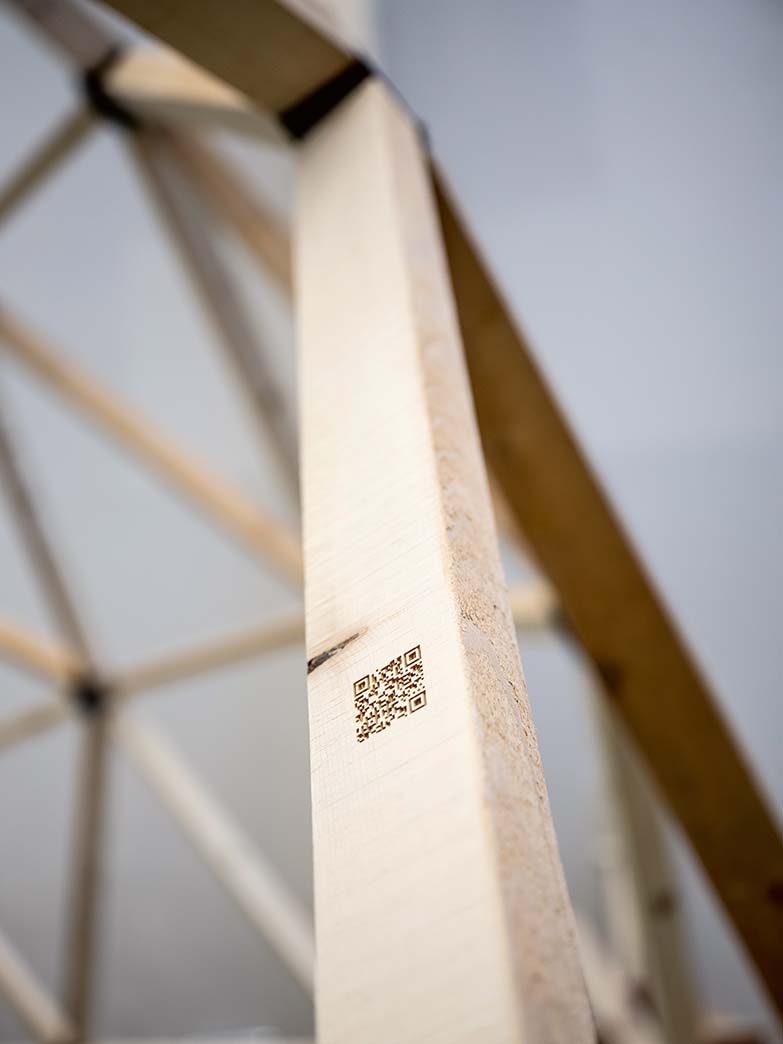
Right now, Byers is using a laser cutter to engrave the last of the QR codes into the wood. Meanwhile, in the construction hall, the rest of the group is starting to build the dome. Working in pairs, the researchers screw the ends of the wooden struts onto the ring-shaped connections, which are made of sections from an old plastic water sewage pipe, also salvaged from the building in Geneva. Two hours later, the bottom layer of geodesic triangles is already finished. All in all, it takes them just three days to assemble the entire dome – but then they encounter another obstacle.
The wooden struts are putting so much strain on the plastic hubs that they have begun to warp – another illustration of how challenging it is to plan a building when you have almost no information about the reused materials you’re working with. But this is another hurdle that can be overcome thanks to digital fabrication. Using a computer-numerical-controlled (CNC) milling machine, the researchers cut the salvaged chipboard into discs that fit perfectly into the plastic rings. “As well as improving the dome’s stability, the pieces of chipboard actually make the construction more aesthetically pleasing,” says Raghu, who is leading this part of the project.
Summer course for students
“I’m really proud that my research group managed to build something so beautiful in such a short space of time,” says De Wolf at an informal gathering to mark the building’s completion. In the private sector, very few buildings are currently built according to circular economy principles. “Projects like this one can only succeed if all the stakeholders are on the same page,” says De Wolf.
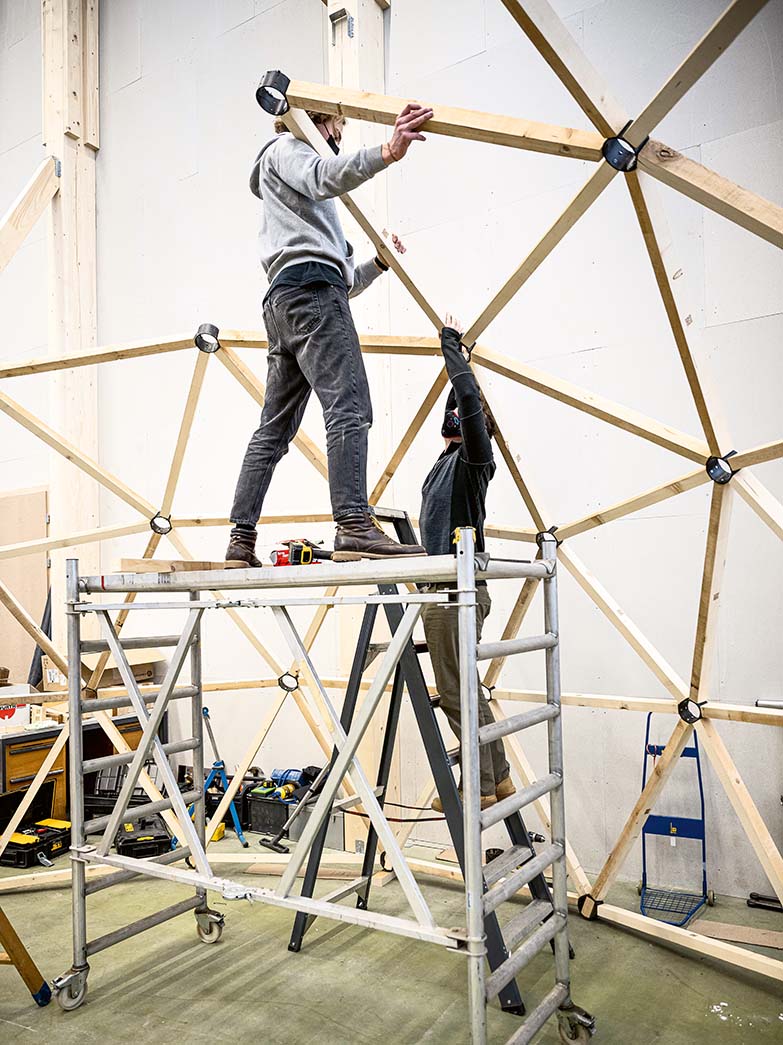
By bringing together architects, engineers and computer scientists, she hopes to create the right conditions to achieve this – at least within her own research group. Perhaps even more important, she says, is the ability to combine environmental sensitivity with an affinity for the digital world. But that can be a tough call. “On one side you have
people who are fighting for the environment like Greta Thunberg, and on the other tech geeks like Elon Musk,” says De Wolf. What she’s looking for are digital natives who are willing to dedicate their skills to protecting the environment.
One of De Wolf’s primary goals is to raise awareness of her field of research. Her course
at this year’s summer school will bring together students from different departments to build another dome from reused materials. This dome will
remain on the Hönggerberg campus over the summer to showcase her work. She is also planning an exhibition on the circular economy in construction as well as a number of smaller events.
Video about this story
Globe (Un)known threats
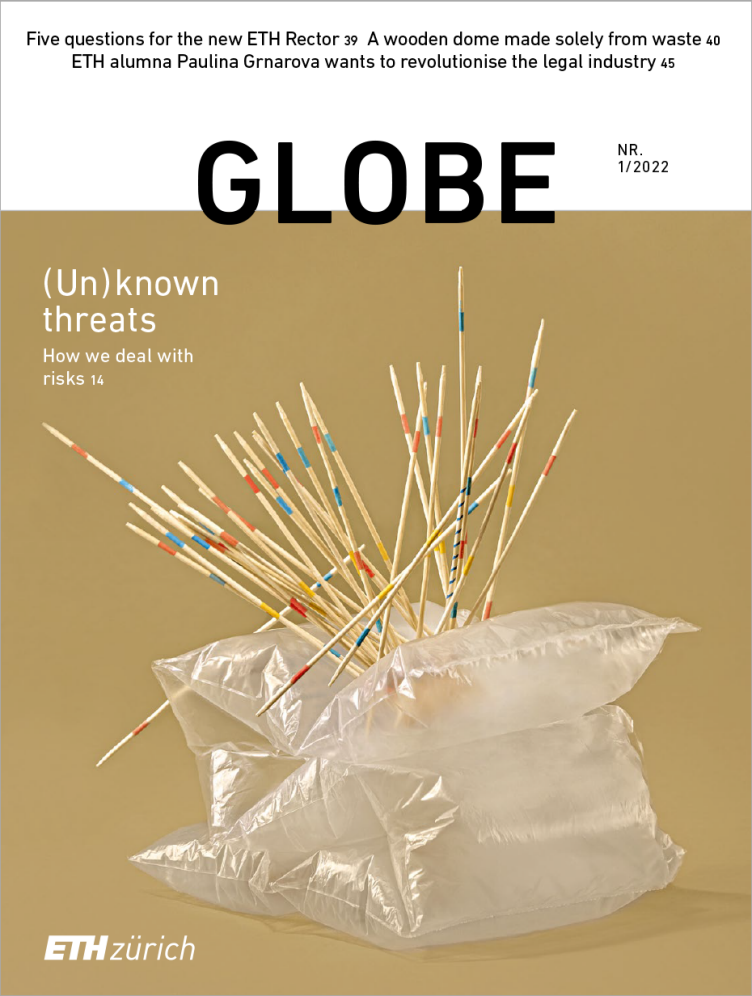
This text appeared in the 22/01 issue of the ETH magazine Globe.
Download Read the issue as a PDF (PDF, 5.5 MB)
Read the issue online