A robot takes its pick
Agriculture is a very labour-intensive business and finding the workforce is increasingly difficult. Wouldn’t it be great to let a robot do the work?
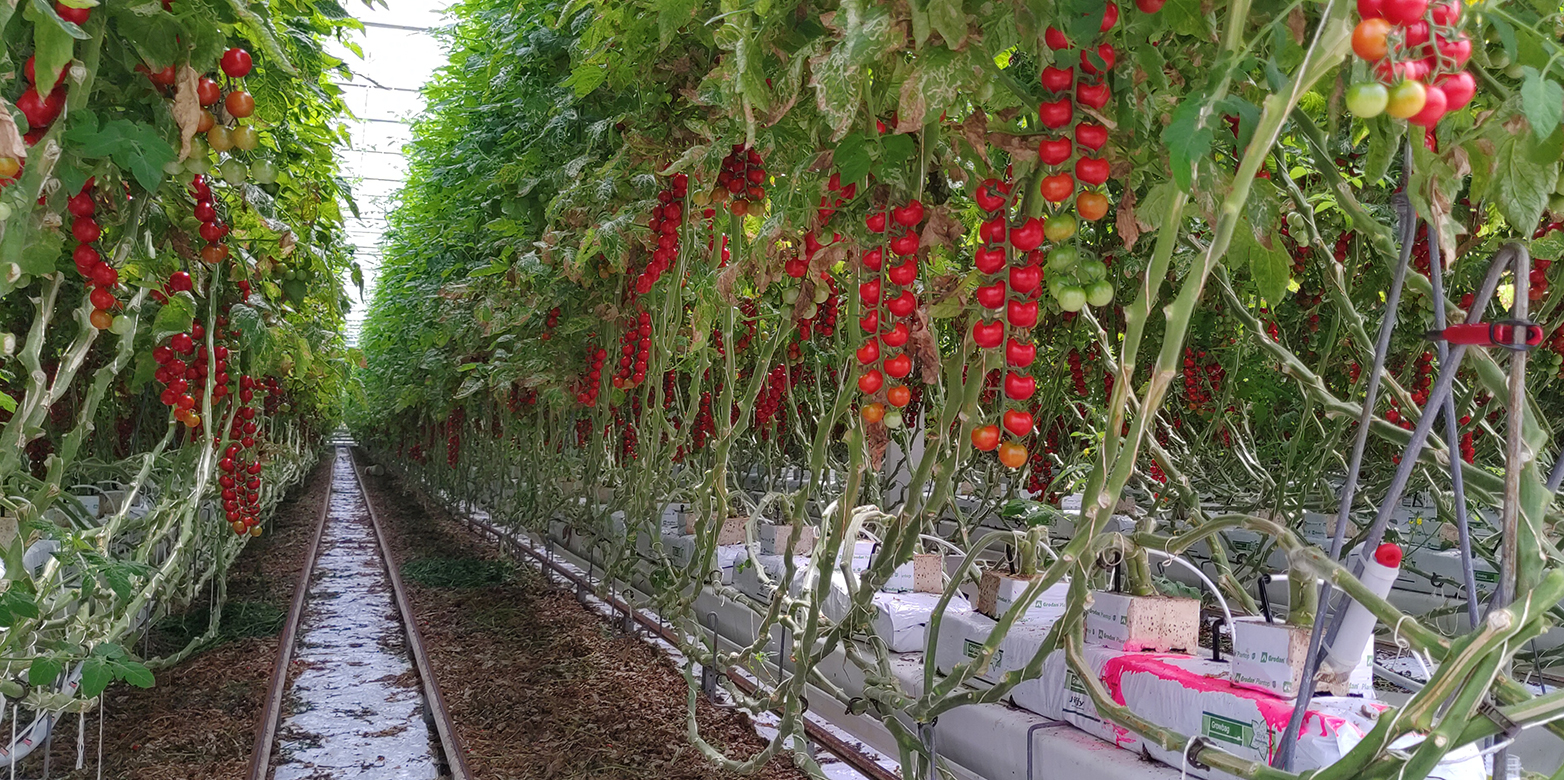
Modern horticulture is already quite industrialised. However, a lot of manual work is still involved, which greatly impacts annual costs. Added to the difficulty of finding the workforce, it is no surprise that there is great interest in automating certain tasks. Salman Faraji from the ETH Robotic Systems Lab (RSL) and his team developed a robot that does some of the work and is easy to incorporate into existing systems. Watching the robot do the work is almost therapeutic – the arm reaches out, steers towards the peduncle, cuts and drops it into the box - repeat.
“Harvesting alone accounts for 4 to 6% of the total production cost and, therefore, the potential savings are significant,” says Toni Suter, Production Manager at Meiergemüse in Rütihof, Switzerland. On average, it takes a total of 2’815 hours of labour to harvest and de-leaf one hectare per year. On the other hand, a robot is operational for 4’246 hours per year, including night work. So extrapolating, a single picking robot manages the required output for 1.5 hectares, which is why it can replace 3.5 employees. Given these facts, it is not surprising that Salman was not the first to think of automating horticulture. So, what sets Floating Robotics apart from its competitors?
Deep learning and a clever system
“Our system combines robotics, image processing, and advanced AI”, says Salman. The robot consists of a robotic arm with gripper and shears, cameras, and cutting-edge parallel-processing capabilities. The arm can be mounted on an existing cart used for maintenance in greenhouses. For harvesting, a boxing system is added.
The robot is trained to detect the fruit’s ripeness (e.g., cherry tomatoes) thanks to image processing. It also identifies the peduncles and leaves. This allows the robot to work each lane, pick the peduncles close to the stem, and put them into the harvesting box. Equally, the robot can work the rows de-leafing the tomato plants – the same principle but different training. “It sounds simple, but behind the technology are two years of intensive research and programming at ETH. The biggest challenge was to teach the robot to detect thin objects correctly”, explains Salman. “We are working with plants, after all, and plants are not identical which makes the training of the robot all the harder.” Nevertheless, Floating Robotics are targeting to pick tomatoes with 95% precision.
There are competitors in the market, but none of them offers as much flexibility as Floating Robotics. Some devices only defoliate plants and others only pick individual tomatoes or peduncles. Also, they are not compatible with existing greenhouse infrastructure and, therefore, require additional investment.
Successful pilot project
In 2022, Salman and his team piloted their first prototype with the support of Innosuisse at Meiergemüse. In 2023, Floating Robotics will carry out a second pilot at Beerstecher near Zurich. Bianca Curcio, Head of the Greenhouse at Beerstecher says: “We got to know Floating Robotics last year and were impressed to see how well the robot can handle picking and defoliating. We are confident that the pilot will show how an automated robot could best be incorporated into current crop management, and in what conditions it can be a useful tool for greenhouse managers to ensure healthy produce all year round.”
Challenges and outlook
Even though there are still a few hurdles to take, Floating Robotics is planning to offer much more in the future. While the harvesting and boxing should be optimised in 2023, they plan to incorporate row changing and night operation in 2024. By 2025 they hope to be able to add string clipping and cucumber harvesting to their portfolio and, very importantly, enter the much bigger EU and North American market.
Salman is currently looking for investors to support Floating Robotics. He plans to incorporate it in early 2023 and is looking forward to talking to interested parties.
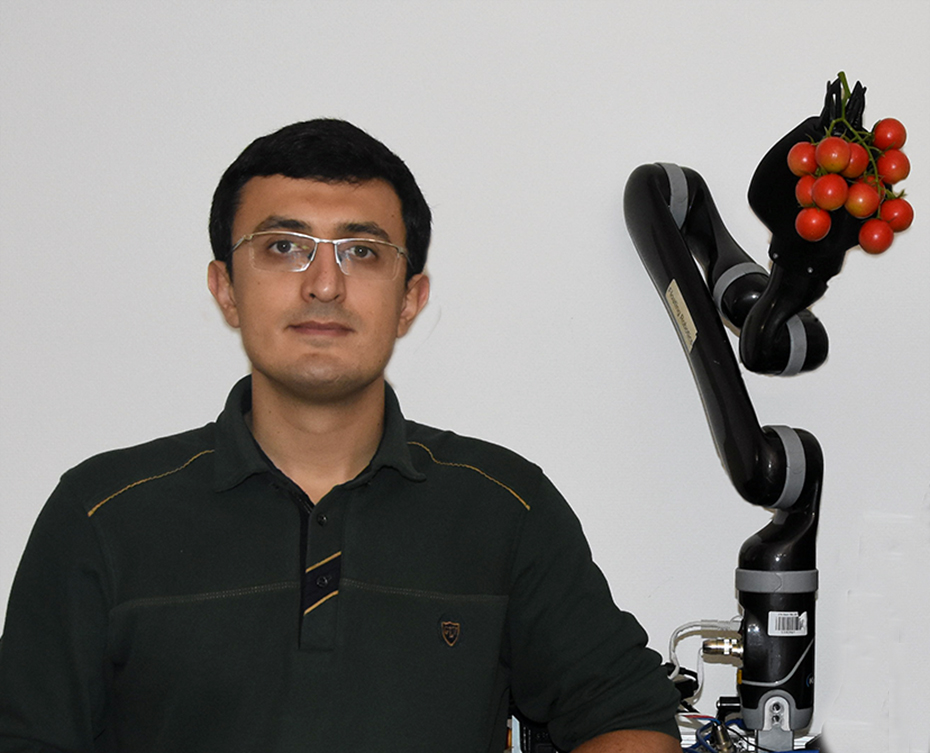
Contact/Links:
external pageFloating Robotics
Do you want to get more "News for Industry" stories?
external pageFollow us on LinkedIn
Are you looking for research partners at ETH Zurich?
Contact ETH Industry Relations