Recyclable batteries for tomorrow’s cars
Lithium-ion solid-state batteries are the batteries of the future. However, their mass production is still too expensive. ETH spin-off Eightinks is developing a manufacturing technology for the mass production of new battery materials and designs. In addition to the scalability of the technology, the goal is also a complete circular economy for batteries.
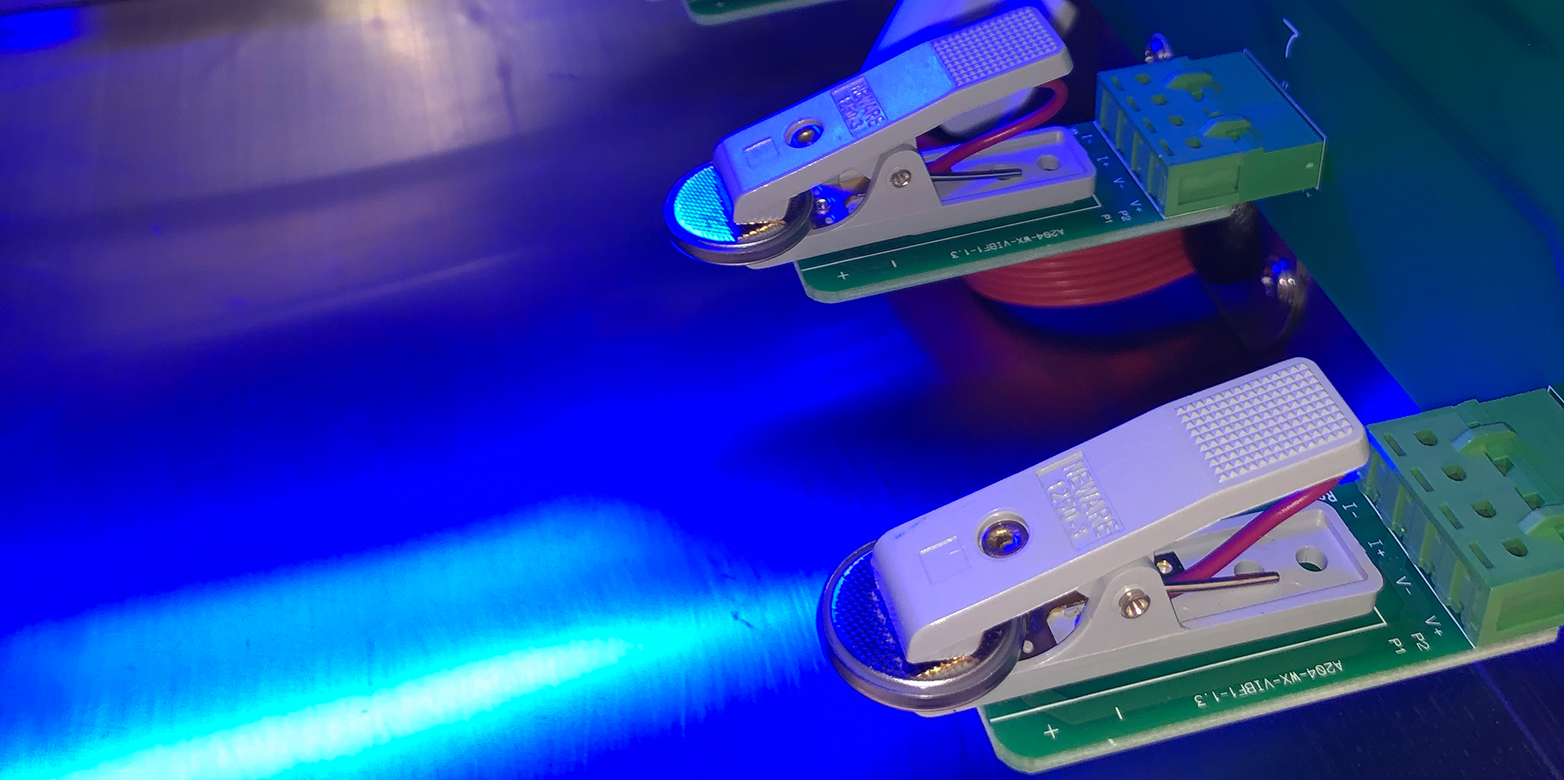
Thinking about our mobility in 10 years time, we picture electric vehicles and thus vehicles with batteries. However, the batteries of future cars will no longer be comparable with those of today because the materials and technologies currently used in conventional lithium-ion batteries are reaching their limits in terms of performance. New materials and, above all, solid-state batteries are called for and, therefore, the subject of intensive research and development.
Solid-state batteries have the advantage of being safer due to the absence of a highly flammable liquid. They also allow the use of materials with higher energy density, which enables thinner layers and thus faster charging. This also leads to lower weight, which makes solid-state batteries even more attractive. However: currently, the high costs and scalability of their manufacturing are a challenge.
The ETH spin-off Eightinks is taking on this challenge and is venturing even further. In addition to cost-effective scalability, they are simultaneously striving for a complete circular economy for lithium-ion solid-state batteries.
Patented technology
Today's lithium-ion batteries are traditionally manufactured using the "slot-die coating" process: the electrode is coated onto a metal foil (current collector). Former Pioneer Fellow Dr Paul Baade of Eightinks has developed and patented a coating technology at ETH using the "curtain coating" process. This allows several as well as thinner layers to be applied simultaneously. Applied to solid-state batteries, this means that the cathode and solid-state electrolyte can be coated in a single application. In the long term, it is even conceivable that all functional battery layers could be applied in a single process step, which would enable further cost reductions and quality improvements.
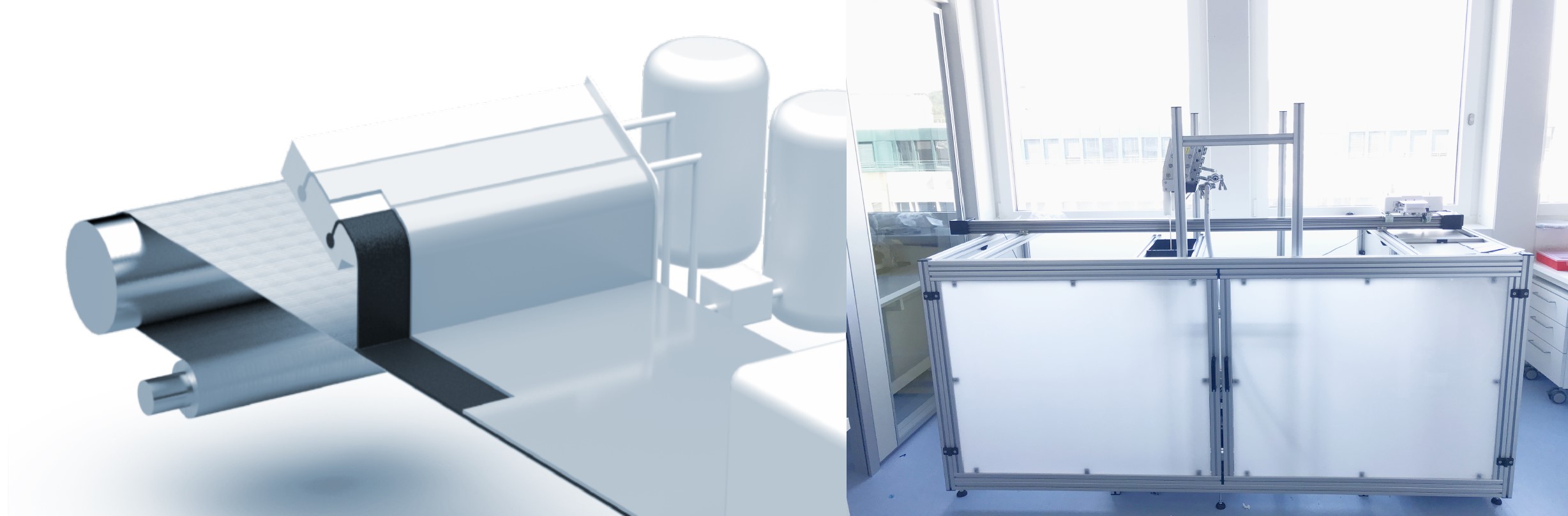
Eightinks' process offers significant advantages in production:
- Coating thickness: 10 microns or even thinner layers are possible at the same speed for improved fast charging capability and high energy density.
- Coating design: Structuring of electrodes and integration of boundary layers optimises battery design for the materials used.
- Production throughput: Compared to before, a 10x faster coating rate is possible with substantial cost reduction in production.
- Compatibility: The technology can be integrated into existing production lines and is compatible with today's materials. Should these change in the future, the technology is flexible enough for adaptation as it is not dependent on a specific material.
Sustainability through circular economy
For cost reasons, only about 5% of batteries are currently recycled. Only the expensive raw materials such as cobalt are worth the recycling effort. However, Eightinks develops its lithium-ion solid-state batteries with the clear goal of a complete circular economy. To this end, Eightinks is aiming for direct recycling, i.e. making it possible to extract the individual particles directly from the batteries and recycle them instead of melting everything down and then filtering out the individual components. This eliminates an additional step, making battery recycling much more energy and cost-efficient. The technology needed to do this is emerging.
Successful laboratory tests
Currently, Eightinks is being established. Founded last December, they have been an official ETH spin-off since June and are in the process of setting up their own laboratory. In close collaboration with the coating head manufacturer TSE Troller and the Bühler Group for the mixers, they are fine-tuning their process. They are also interested in partnerships for materials to enable extensive testing. Eightinks sees several possibilities for the future - from licensing their technology, and contract manufacturing of electrodes, to in-house production of solid-state lithium-ion batteries.
Dr. Paul Baade is a speaker at this year's ETH Industry Day on September 6 at ETH Hönggerberg. Together with his team, he is looking forward to welcoming interested visitors to their booth. external pageRegister today!
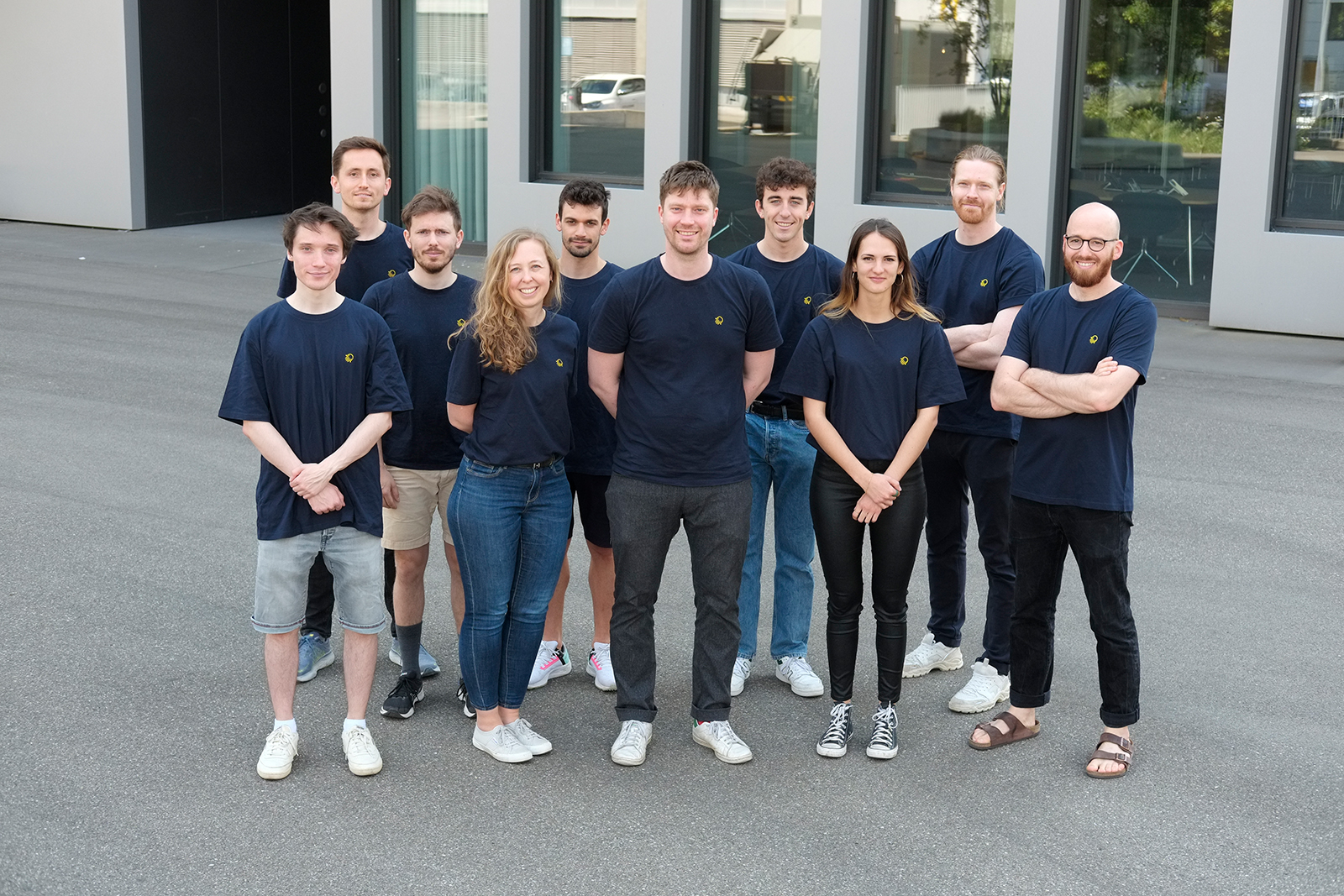
Contact/Links:
ETH Industry Day: external pageregistration
ETH News Batteries for transporting mobility into the future
Do you want to get more "News for Industry" stories?
external pageFollow us on LinkedIn
Are you looking for research partners at ETH Zurich?
Contact ETH Industry Relations
ETH spin-offs: facts and figures
Since 1973, 540 spin-offs have been founded at ETH Zurich. ETH transfer, the technology transfer office at ETH Zurich, supports recognized ETH spin-offs in the founding process and in their first years of operation.
With the help of the Pioneer Fellowship Programme, funded by the ETH Foundation, young researchers can develop innovative products and services based on their scientific work at ETH Zurich. A Pioneer Fellowship is awarded to young ETH entrepreneurial minds intending to develop a highly innovative product or service to be exploited commercially and/or for the benefit of society.
Offers for entrepreneurs at ETH
Press release ETH spin-offs January 2023: Digital twins, new cancer treatments and three unicorns