Digital twins for the machine industry
What is a digital twin, what can it do, and what requirements does it have to meet to be of practical use in the machine industry? ETH researchers and three companies investigated these questions and came up with some surprising results.
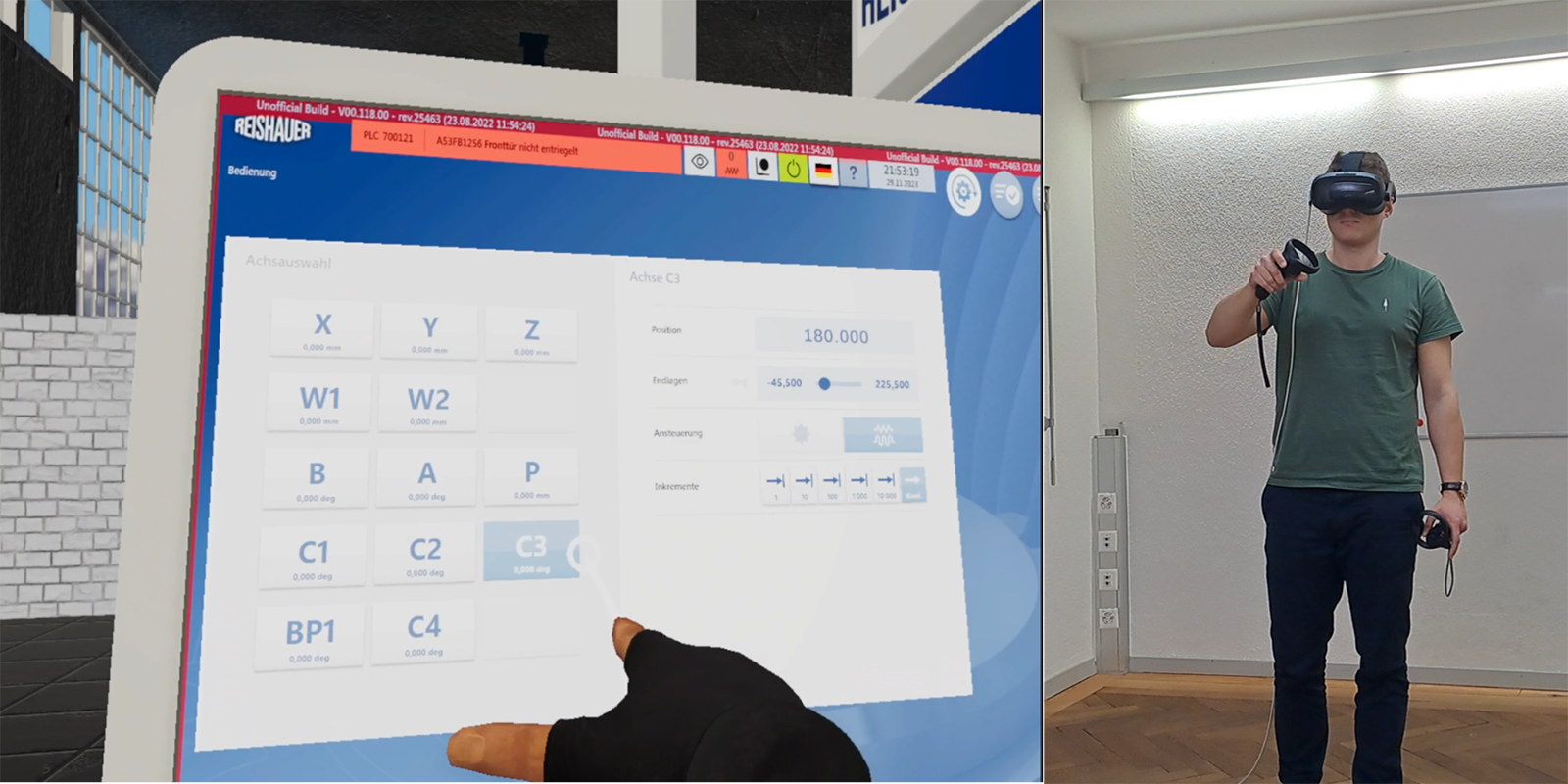
Joy Gisler (ETH Zurich), Florian Hänni (Reishauer AG), and Alexander Farger (Siemens Schweiz AG) provided insight into the project.
Digital replicas of real machines that can be operated virtually are called digital twins. "ETH is doing a lot of research into virtual reality and digital twins," says Joy Gisler, a researcher at the Institute of Machine Tools and Manufacturing. "At some point, you want to know how useful the developments are in practice." There was also a lot of interest from industry, which led to an Innosuisse-supported project entitled "Virtual Reality Extension for Digital Twins of Machine Tools". The project investigated two specific applications:
- How should the training course be structured on a virtual machine (digital twin) so that the skills learnt can be implemented on the real machine?
- Can collision analysis for a grinding process be reliably calculated and simulated on a virtual grinding machine (digital twin)?
“ETH is doing a lot of research into virtual reality and digital twins. At some point, you want to know how useful the developments are in practice.”Joy Gisler, ETH Zurich
Learning digitally is as good as learning on a real machine
Extensive training is required to operate the complex machines of grinding machine manufacturer Reishauer. In a test, 20 people were trained directly on the actual machine and a further 20 were trained digitally using a digital twin in virtual reality.
Using the conventional method, the machine is not available for production during the training. The operators were taught in groups of three which took 2.5 hours each.
In contrast, the digital-twin-based method could be carried out independently by all operators at any time and place. The operators only needed 50 minutes to do this. Interaction with the digital twin was intuitive through hand and pointing movements, which were captured by sensors from Sensoryx.
One week after the digital-twin-based or conventional training, the operators were tested on the real machine. It turned out that the tasks were solved equally well by both groups. In summary, digital training has the upper hand: it is faster, can be carried out independently of time and location, and the real machine can produce without interruption.
Good simulation of potential collisions
Grinding machines for gears must work with micrometre accuracy, which requires precise part guidance. Complex algorithms are developed to prevent a collision between the part to be ground and the machine during the grinding process. The second study aimed to determine whether such collision analyses could be calculated more easily, faster and with less effort using digital twins. Here too, the results are very satisfactory because the required accuracy in collision detection was achieved, and the analysis was performed at the push of a button, saving time.
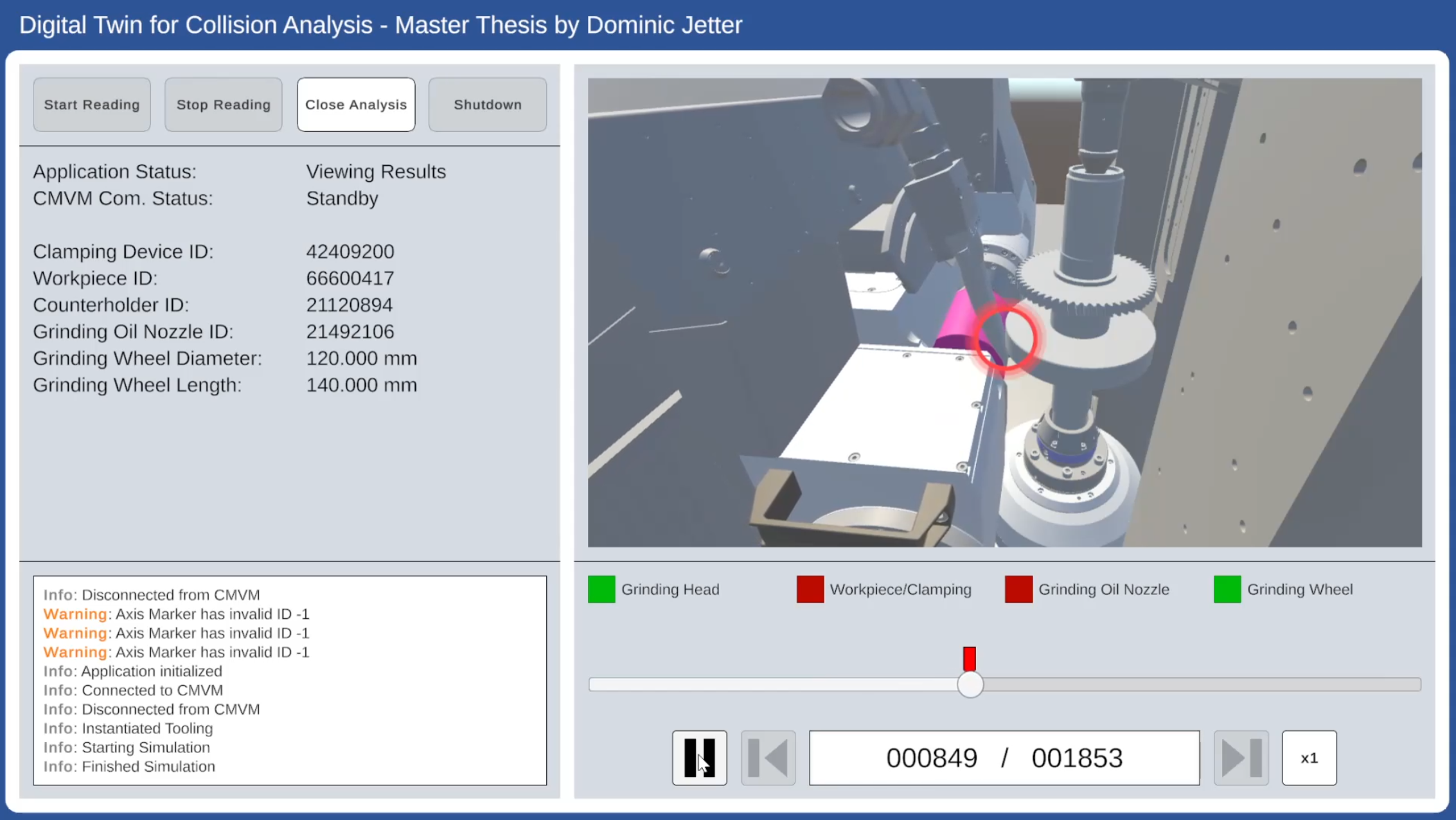
Technological challenge
What sounds so simple was a significant technological challenge: a single digital twin had to be created from the three individual components machine, controller, and algorithm. In other words, a digital version of the Reishauer machine had to be built, equipped with the Siemens controller and the complex algorithm.
“We see great potential in using digital twins in the training of operators and maintenance personnel. The combination with virtual reality takes the teaching of training content to the next level.”Alexander Farger, Siemens Schweiz AG
Everyone benefited
It took all the partners involved to realise this project. The ETH researchers led by Professor Andreas Kunz were able to further develop and apply their VR research in practice. Alexander Farger from Siemens concludes: "Machine manufacturers and operators are already successfully using our products 'Create and Run myVirtual Machine' to create digital twins and optimise manufacturing processes. However, we also see great potential in using digital twins in the training of operators and maintenance personnel. The combination with virtual reality takes the teaching of training content to the next level. The solution is also interesting for educational institutions as it provides an easy way to learn how to use machines of different technologies and complexity levels.
“Thanks to the support of Innosuisse, we were able to evaluate two options for collision testing. Both worked.”Florian Hänni, Reishauer AG
Florian Hänni from Reishauer sees several advantages of this project: "Thanks to the support of Innosuisse, we were able to evaluate two options for collision testing. Both worked. We will integrate collision testing into our design software but will use a different technological approach. Furthermore, we have learned that it is possible to convey complex tasks virtually with a digital twin." For both Hänni and Farger, projects with ETH Zurich are of high value because they knew from the beginning that they had access to the experts in this field and that communication was always open and on an equal footing.
Contact/Links:
Institute of Machine Tools and Manufacturing, Professor Andreas Kunz
Do you want to get more "News for Industry" stories?
external pageFollow us on LinkedIn
Are you looking for research partners at ETH Zurich?
Contact ETH Industry Relations