Architecture of the Mirrors
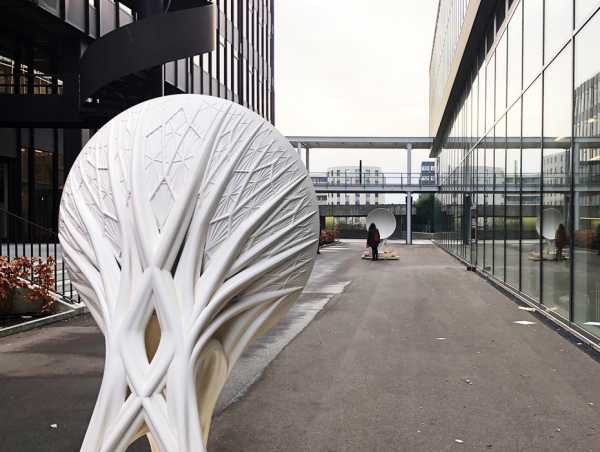
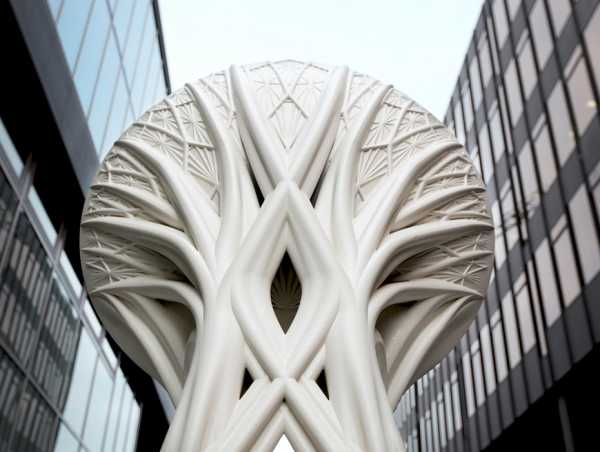
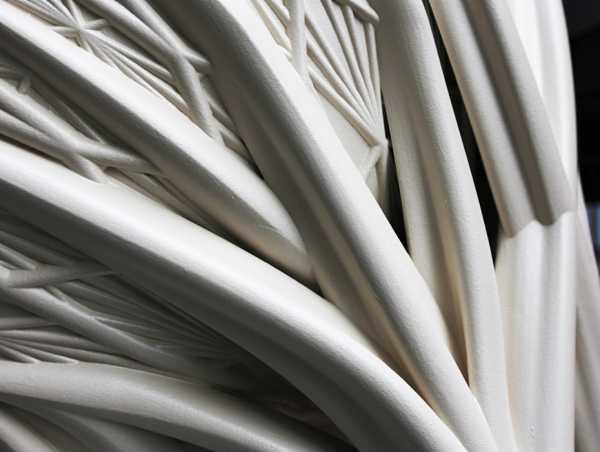
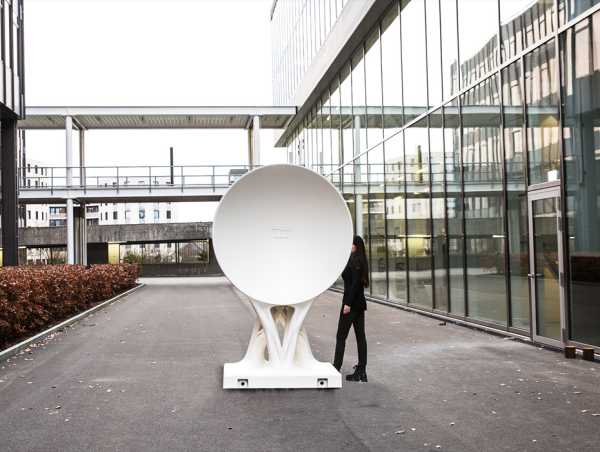
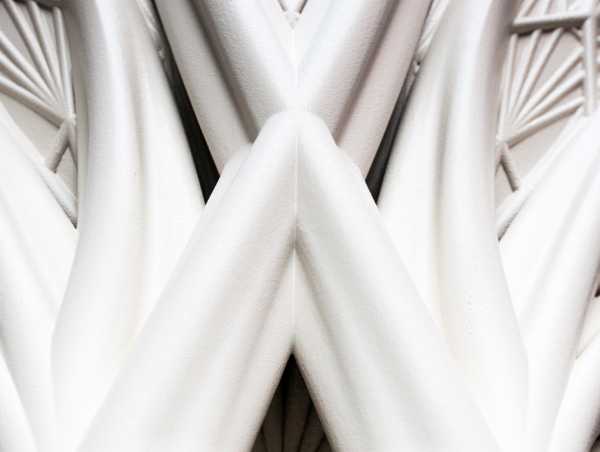
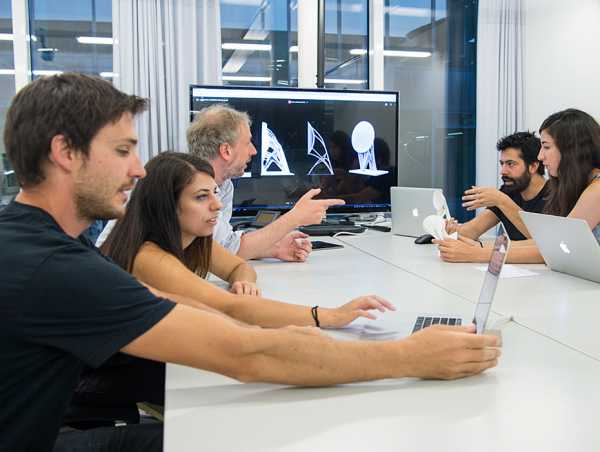
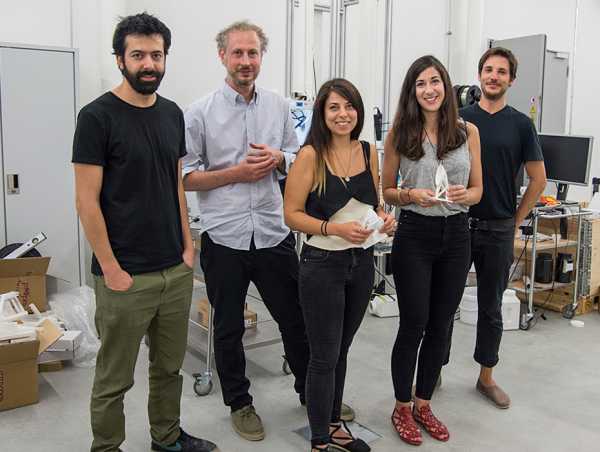
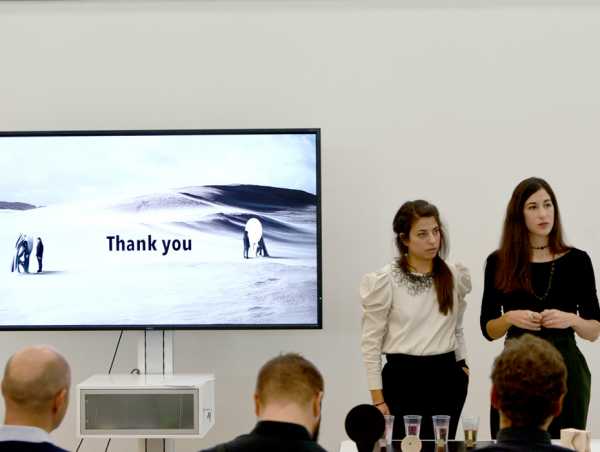
With its performative form, engineered to create a spatial acoustic effect whilst being structurally optimized for efficient material use, the installation “Acoustic Mirrors” showcases the potential of computational design and large scale 3D printing for construction.
The interdisciplinary project bridging physics and architecture consists of two 2 meter monolithic concave mirrors. These mirrors are designed to allow people to communicate by whispering over a large distance, making use of a physical effect which can also be found in the historic architecture of whispering galleries.
The organic and highly ornate design of the mirrors were generated through custom design software, integrating acoustic, structural and fabrication parameters. An optimal weight / strength ratio could be achieved by selectively distributing material along the flow of forces.
Using 3D printing, the resulting complex forms could be materialised in a fully automated and materially efficient fabrication process with precision at a fraction of a millimeter.
Slideshow Design
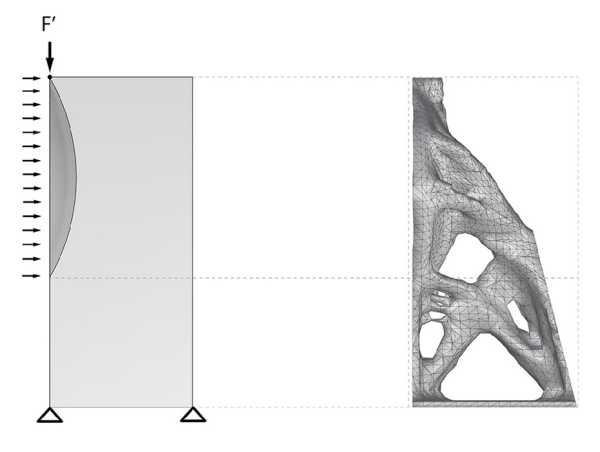
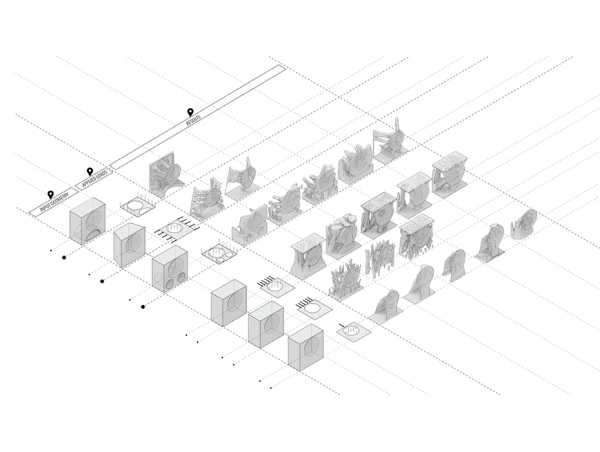
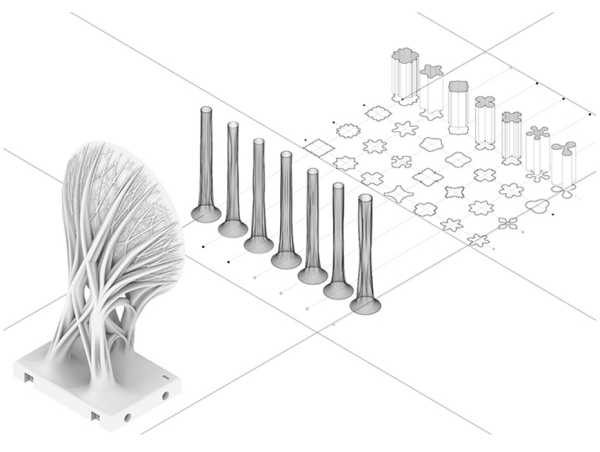
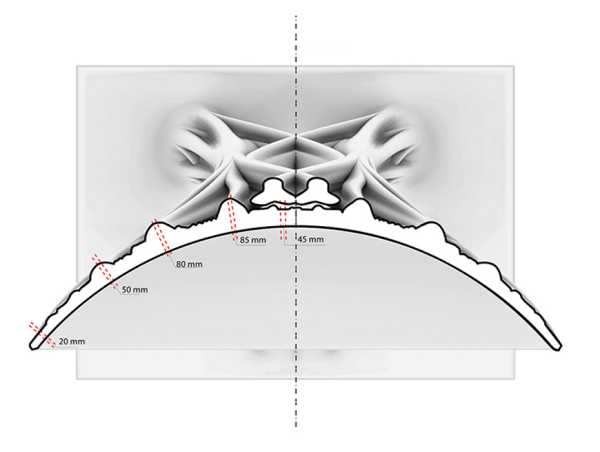
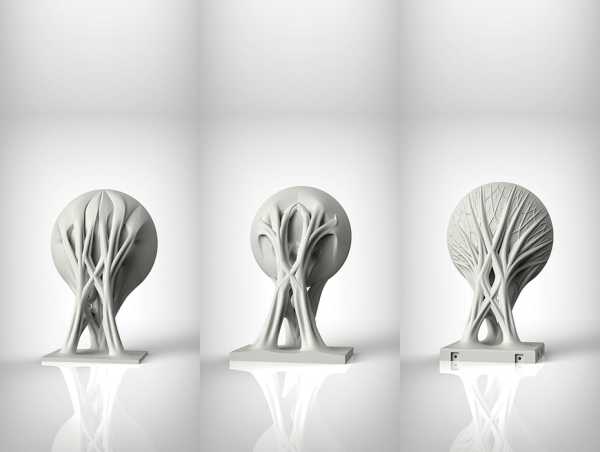
Computational Design
The project Acoustic Mirrors uses computational design for form finding. The design is entirely generated within custom software that integrates a structural optimization program and acoustic simulation software. This workflow facilitates a deep study and evaluation of several design variations, while integrating multiple design criteria into the design. In addition, the parametric design tool developed for this project allows the design of both the overall structures and the small scale details in a coherent process, finally offering the direct export of the final fabrication data.

The overall form is dominated by a spherical cap, which reflects and focusses acoustic waves. The dimension and position of the mirror shell is calculated in a feedback loop coupled with an acoustic simulation software developed by Dr. Kurt. Heutschi at the Signal and Information Processing Laboratory of ETH (ISI). The custom software simulates the propagation of the reflected sound waves and evaluates the sound amplification on the receiving end.
Further information on the reflection of sound.
One of the design goals was to optimize the geometry of the sphere’s supporting structure in order to reduce the overall weight of the construction. Hereby the material properties of the 3D printed sandstone had to be taken into account - with similar properties to natural sandstone, the material is stronger in compression than in bending or tension. The structure is optimized on two scales: The topology of the supporting legs and the topography (rib structure) of the shell itself.
Topology Optimization: The buttress structure, referring to gothic stone architecture, is optimized for a material reduction of 30% in balance with the minimization of strain energy against vertical and horizontal forces (i.ex. gravitational load and wind pressure).
The applied topology optimization (multi-level substructuring eigensolver) finds an optimal material distribution and topological arrangement of the pillars. The resulting geometry is interpreted and translated into the final shape.

Topography Optimization: The large shell contributes a substantial amount of mass to the overall structure. In order to reduce this mass and to stiffen the shell, an organic microstructure was designed to branch from the main support elements and subdivide the overall backside with stiffening ribs. With this shape/topography optimization, the thickness of the spherical cap with a diameter of 1.6 m could be reduced from 50 to 23 mm.
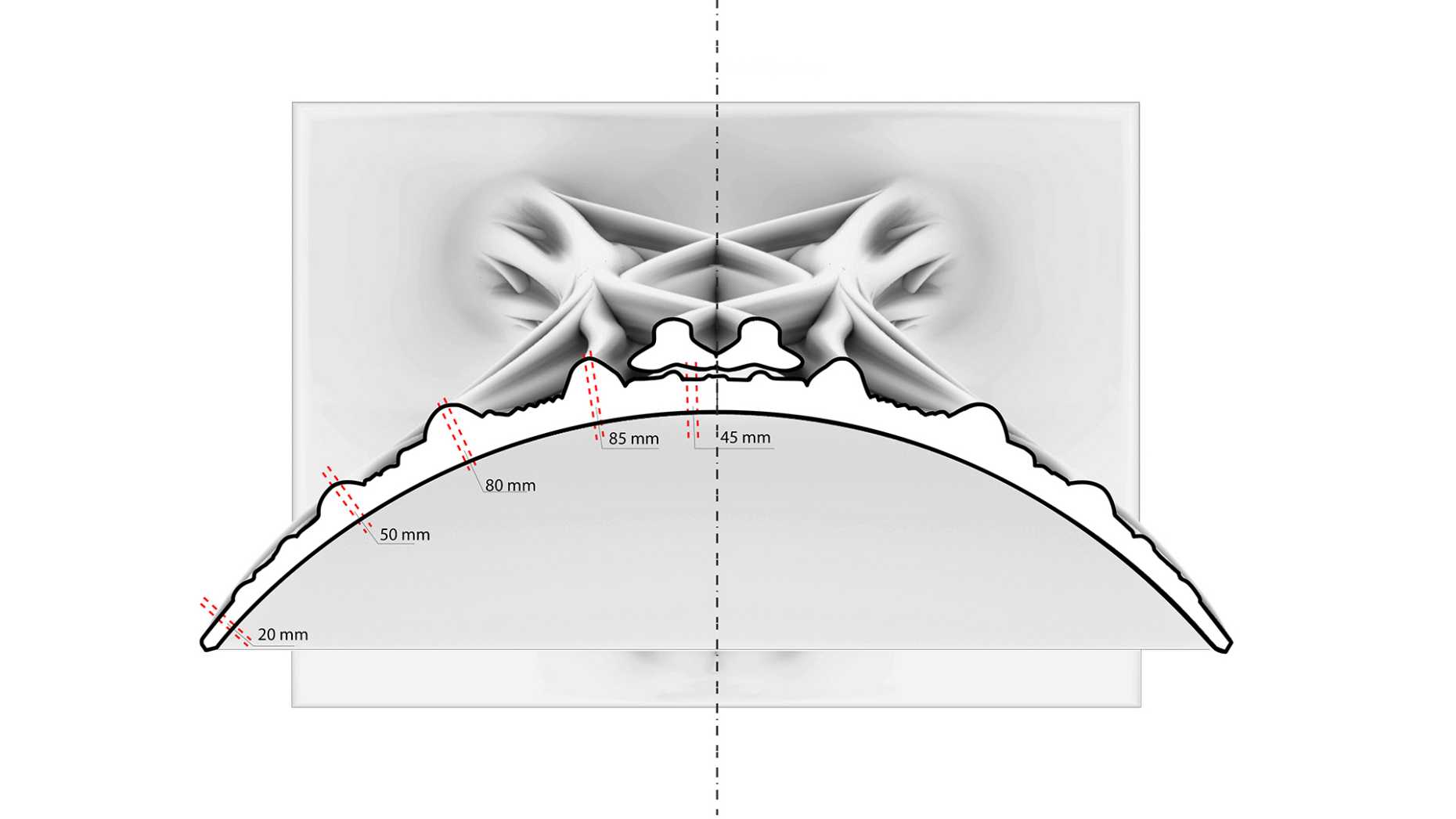
Similar to gothic masonry ornament, the profiles of the hierarchical branches are modulated along the structures, adjusting the orientation and diameter according to the load case. The stone ribs are smoothly and continuously interwoven with each other. These filigree structures appear on various scales, from 100 mm thickness down to 5 mm, in each case reaching the structural limit of the 3D printed stone material.
All features for lifting, transport and assembly could be directly integrated into the 3D model, and no additional machining was necessary after the 3D printing. As the mirrors were 3D printed horizontally, lifting details were integrated which allow the rotation of the 600kg structure. The design is adjusted to move the center of gravity of the mirrors to an optimal position for transport and assembly. Connections to the ground are integrated. Within the shell, the acoustic focus is indicated, and on the base, details for the precise alignment on site are integrated.
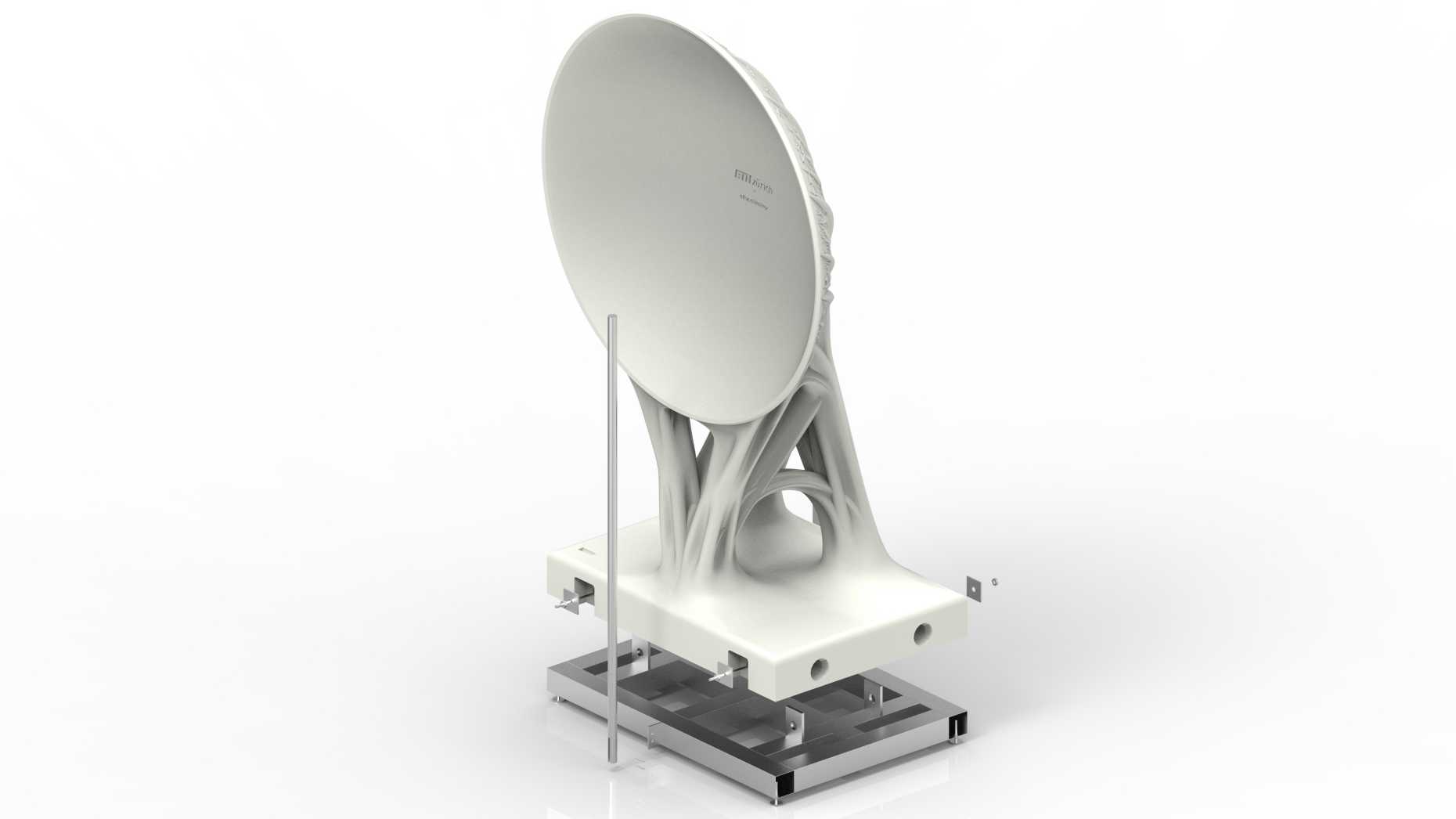
Print Slices
- Chapters
- descriptions off, selected
- captions off, selected
This is a modal window.
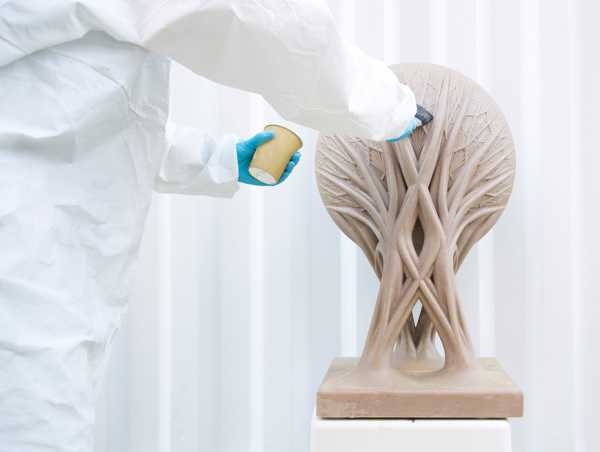
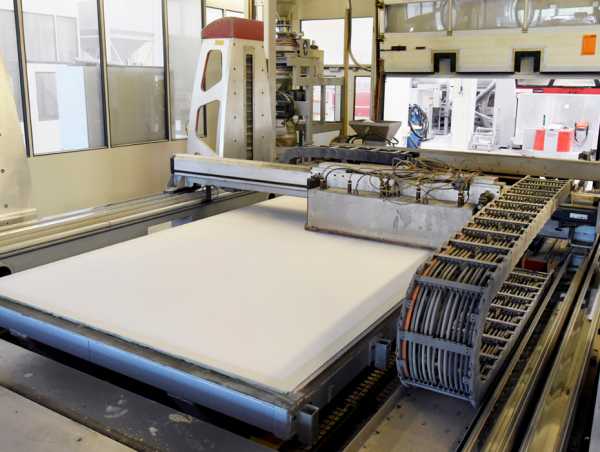
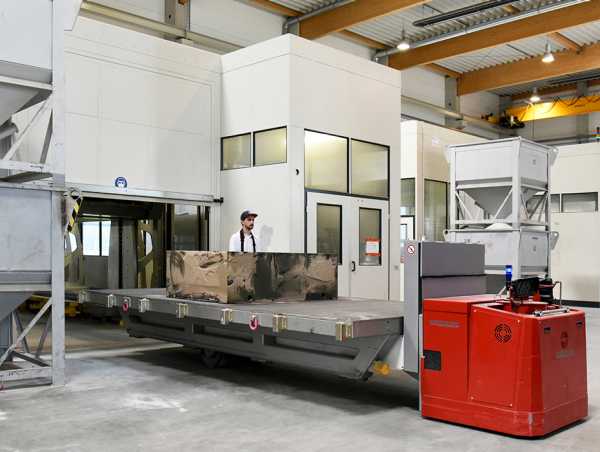
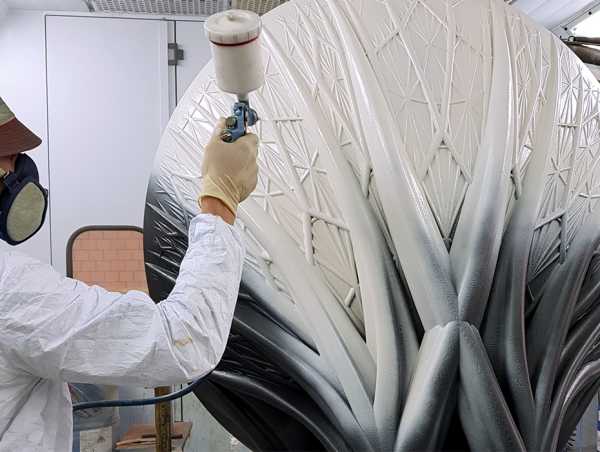
Digital Fabrication through 3D Printing
Additive Manufacturing for construction
For the first time, 3D binderjet printing was used to create a large scale outdoor installation made from artificial sandstone. The two mirrors are some of the largest parts printed with binder jetting. Compared to fabrication based on cast concrete, direct additive manufacturing has key advantages.
- Formwork free fabrication: The process does not require formwork, hence reduces waste and cost in the fabrication process.
- Material efficiency: No material needs to be milled and material is only used where needed, while unused material can be recycled.
- Customization: Using 3D printing for construction promises to fabricate customized elements without generating extra cost.
- Complex Geometry: With 3D printing, complex geometries can be efficiently fabricated that might otherwise require multiple, time- and labour-intensive fabrication steps, or could even be impossible to fabricate otherwise.
Binderjet printing
Binderjet 3D printing follows a procedure which is repeated layer by layer with an increasing height. In the first step, loose sand is evenly distributed along the full print bed. In the second step, a 2D pattern of binder is printed which selectively bonds the sand together with the lower layers. Among the various 3D printing strategies, binderjet printing offers specific advantages for construction:
- High resolution: Features can be printed in a resolution at a fraction of a millimeter
- Large dimension: Large print-bed of up to 4x2x1m
- Highest geometric freedom: Cantilevering and hollow geometries are possible as the loose sand acts as support during the printing process
- Fast print speed: Fabrication time is independent from the complexity of the geometry due to fullwidth industrial printheads.
- Low cost: Material costs are significantly lower compared to other high resolution printing strategies
Each acoustic mirror could be printed with the largest industrial 3D binderjet printer with a print-bed of 4x2x1m and a layer height of 0.3 mm in less than 48 hours.
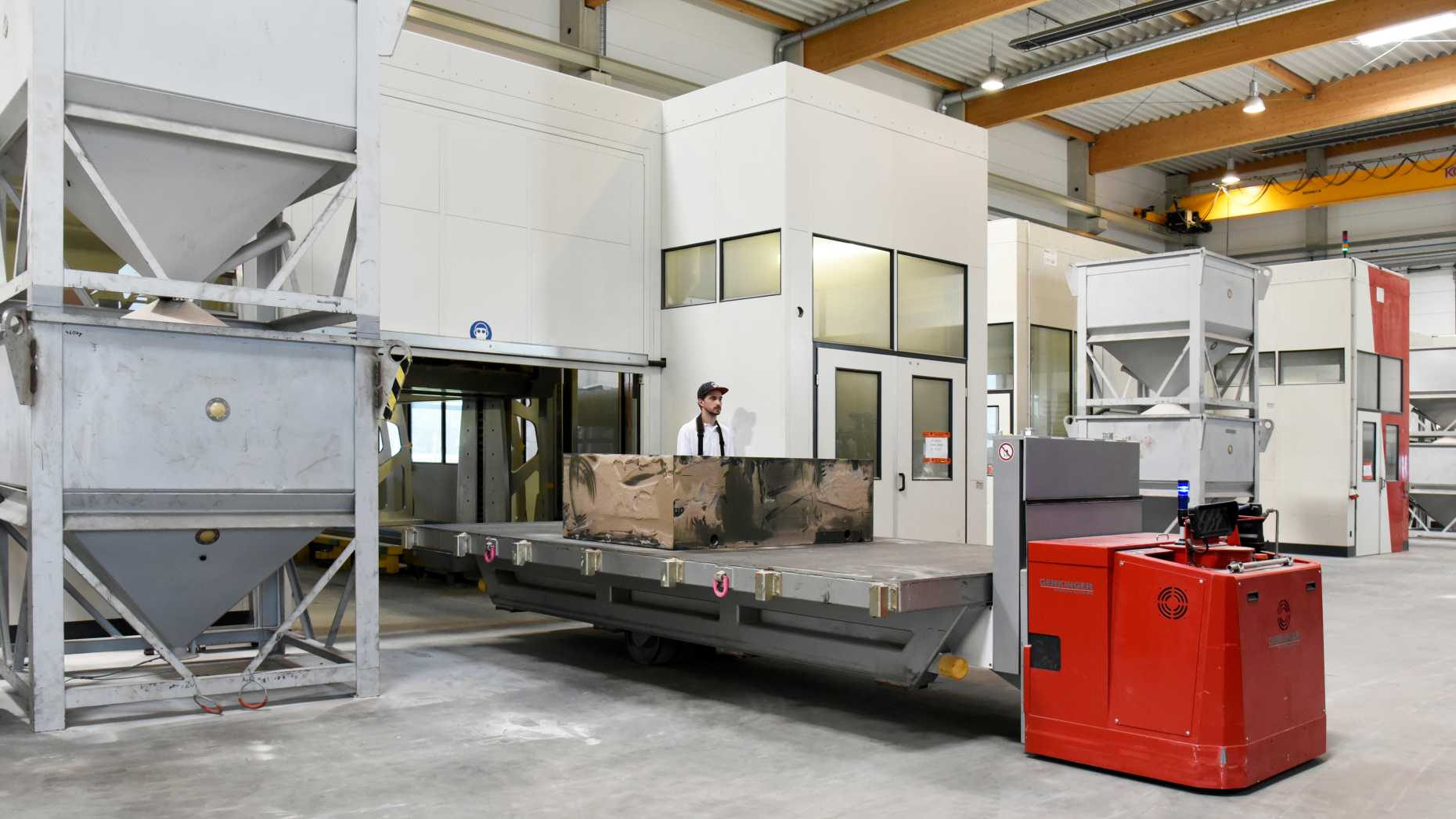
Functional coating
As the surface of printed sandstone is porous and fragile, for an outdoor application, several coating strategies were investigated. The selected sprayed sealant with a thin layer of polyester resin protects the structure against the weather. Structural tests have also shown that the 3D printed parts can be dramatically strengthened through the resulting composite material system. A final coating of a bright layer of color reveals all the details and ornament of the installation and guarantees high contrast and shadowplay under sunlight.
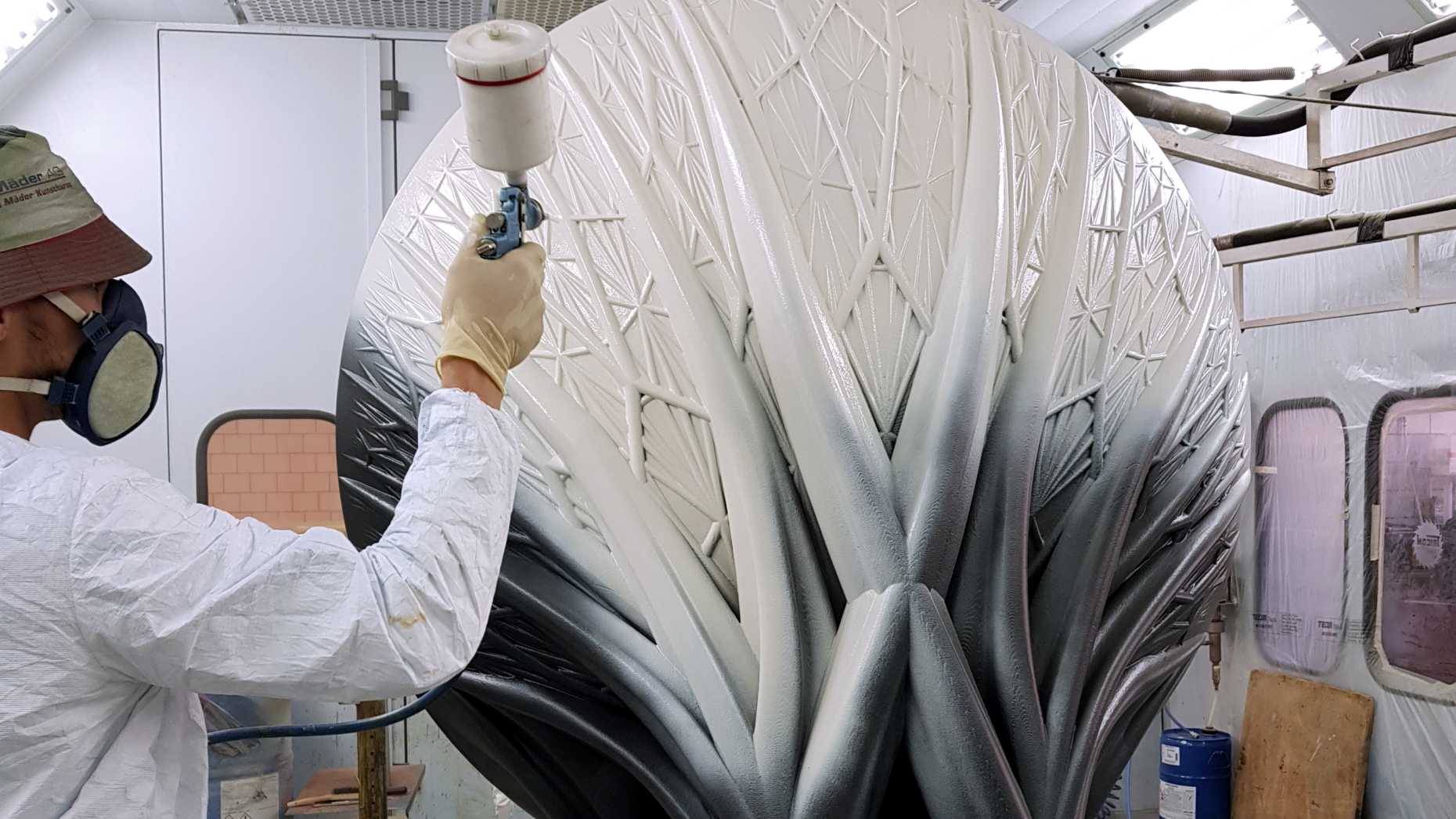
Please find more information about the team of the Acoustic Mirror in the imprint.