Augmented Reality manuals
ETH spin-off Rimon Technologies has developed a framework to enhance the capabilities of teams and companies to build their own augmented reality (AR) applications such as manuals for complex machines or inspections.
- Read
- Number of comments
David Shapira and Kordian Caplazi talked to us about their start-up.
What problem does Rimon Technologies solve?
Technology is developing rapidly. Modern machines feature integrated software, process engineering and complex devices. It is essential for companies and their workforces to keep up to date through continuing education and on-the-job training to stay relevant.
This, however, requires an immense amount of time and effort for all parties involved. Workforces depend on the manuals provided by the companies that built the machines, or the know-how of instructors. This is a time- and resource-consuming commitment.
To alleviate this, Rimon Technologies enables companies and employees to create their own step-by-step instructions more simply and quickly than with conventional tools, allowing them to compile tailor-made instructions that can be deployed on either augmented reality (AR) glasses or handheld devices such as tablets or smartphones.
How does the solution work?
Rimon develops and validates AR applications in close cooperation with industry representatives to determine the best suitable application for each company. First, we define a given company’s specific needs and then build a solution that is applicable in any use-case. We support the digitalisation process alongside the workforce and offer tech talks and workshops on virtual and augmented reality, ensuring a positive introduction to this relatively new technology. In several trial runs, the use of AR glasses with Rimon’s step-by-step instruction has proven to reduce critical errors by 100% and the overall performance improved thanks to clear and structured guidance.
To create these AR step-by-step instructions we asked ourselves how we could make it as accessible as possible. So we split the instructions into four components: Pictures, videos, CAD models and logic. Images, Videos, CAD-Models and logic. The Images, Videos & CAD-Models guide the user through the process. The logic is there to tell the software when to display which components and how to guide the user through the process. This logic can be written with tools available in any organisation. This allows companies to eventually write their own AR step-by-step instructions and apply them to the use-cases where they see the biggest benefit.
Our overarching goal is for people to do their job well - always and everywhere – so that both customers and employees are satisfied with the result, whether it is commissioning a new machine, maintaining equipment, or inspecting infrastructure.
In addition, the software can collect data in the background to determine if there are steps in the process where the workers have repeated problems, which means there is the possibility to optimise the processes by supplying the worker with additional information.
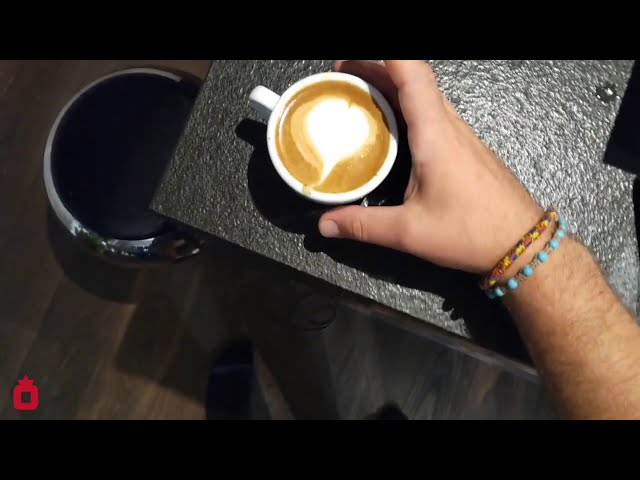
Is the technology already in use? When will people be able to benefit from your solution?
Yes the technology is already in use, we are working project based with companies to determine what their individual needs are. Given the relative newness of augmented reality technology, there are not many specialists within companies. This is where Rimon comes in: we support the companies in implementing the solution and teach them how to develop it further themselves, so that they can adapt it to their needs as these evolve. Once our customer has an understanding of our solution we switch to a licensing model, allowing them to create as many instruction manuals as they need.
Frontline workers in the industrial engineering industry are our current focus group. Applications of our technology range from helping internal specialists within the company to save time and reduce errors in their work. The augmented reality solution can also be used to support the onboarding of new employees who require training.
Other use cases include installing or repairing machines. Furthermore, Rimon’s augmented reality solution could save expensive trips of expert installers around the globe in connection with the export of complex machinery. The file with the instructions can simply be transferred to a person on site who can then take over. Using Rimon’s quality control features allows for a clear documentation of the work process for the costumer, the company and the technician.
What are your plans for the future?
One of our first partners is an automation company for which we created an augmented reality app that was very successful. We would love to support other companies in helping them to create their own augmented reality manuals.
For now, we want to implement our solution primarily in the machine industry because we both studied mechanical engineering and, consequently, have an understanding of its inherent challenges. We are open to other fields, of course, and can see use-cases in a number of different industries and areas.
What is your vision?
Our vision is to enable people by rethinking the manual. Our solution was created to allow people to perform tasks they have never done before, by displaying information differently to the user.
This makes the work tasks of frontline workers easier, which translates into them being happier since they can deliver solid results every day.

Contact/Links:
external page Rimon Technologies
Master Thesis external page video showing the commissioning of an automatic door (source: Rimon Technologies)
Do you want to get more "News for Industry" stories?
external page Subscribe to our newsletter
external page Follow us on LinkedIn
Are you looking for research partners at ETH Zurich?
Contact ETH Industry Relations
ETH spin-offs: facts and figures
Since 1996, 471 spin-offs have been founded at ETH Zurich. ETH transfer, the technology transfer office at ETH Zurich, supports recognized ETH spin-offs in the founding process and in their first years of operation.
With the help of the Pioneer Fellowship Programme, funded by the ETH Foundation, young researchers can develop innovative products and services based on their scientific work at ETH Zurich. A Pioneer Fellowship is awarded to young ETH entrepreneurial minds intending to develop a highly innovative product or service to be exploited commercially and/or for the benefit of society.
Comments