Replication of coloured 3D models simplified
Researchers at ETH Zurich and Disney Research Zurich have developed a new technique called Computational Thermoforming. It enables them to manufacture plastic replicas of digital 3D models, in which the shape and colour are reproduced in detail. This technique extends the range of digital fabrication methods and represents an efficient and cost-effective alternative to colour 3D printing.
The new method is a clever combination of an established industrial production technique (thermoforming) and a new software, which allows even ambitious amateurs to produce individual pieces or small batches of objects with structurally complex and coloured surfaces quickly and cheaply. The researchers have just described their method in a scientific publication, which will be presented at the ACM SIGGRAPH 2016.
The technique’s core is based on an accurate simulation of the thermoforming process, which ETH doctoral student Christian Schüller developed in the Interactive Geometry Lab under the supervision of ETH Professor Olga Sorkine-Hornung. The simulation computes an image from the coloured surface of a digital 3D model, which is then printed on to a plastic sheet. Through thermoforming, this sheet is then heated and forced into a three-dimensional shape. The key lies in computing the deformed image, so that the colours and patterns align perfectly with the geometric details of the mould.
The thermoforming technique is widespread in industrial applications and is used to manufacture many of the moulded parts that we use daily, such as yoghurt containers, inserts for boxes of chocolate and other packaging materials. “But the industrial method is not suitable for inexpensive manufacture of small batches or even individual pieces of complex shape or colour-printed models,” says Schüller. In order to print these parts accurately, specialist equipment and elaborate calibration are required.
The researchers have thus developed a method based on readily accessible and inexpensive equipment and materials, and which does not require highly specialised expertise.
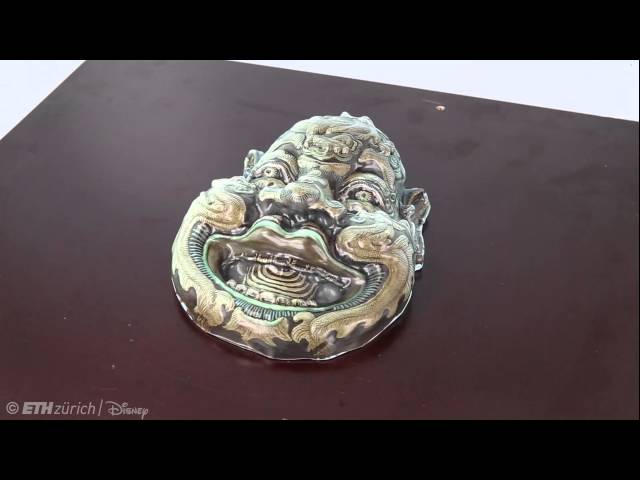
Mould and print
In a first step, a simple 3D printer is used to produce a negative mould of a model made of polylactic acid (PLA), a single-colour plastic. This forms the basis for the temperature-resistant gypsum mould, which is required in thermoforming.
The software computes the correct texture for the 3D model, which is printed with a standard laser printer on to a special transfer paper. With the help of pressure and heat, the image is then transferred on to a plastic sheet.
The printed plastic sheet is clamped in a thermoforming machine above the gypsum mould and heated until it becomes malleable. A vacuum quickly sucks the air from between the sheet and the gypsum cast, setting the plastic tight on to the gypsum mould like a skin – creating the plastic replica.
After the thermoforming, it is possible to see whether the software has computed the printed image correctly: “The deformation of the plastic also changes the printed image. But our software accurately calculates and compensates for this deformation,” says Schüller.
Computational Thermoforming - fabrication steps
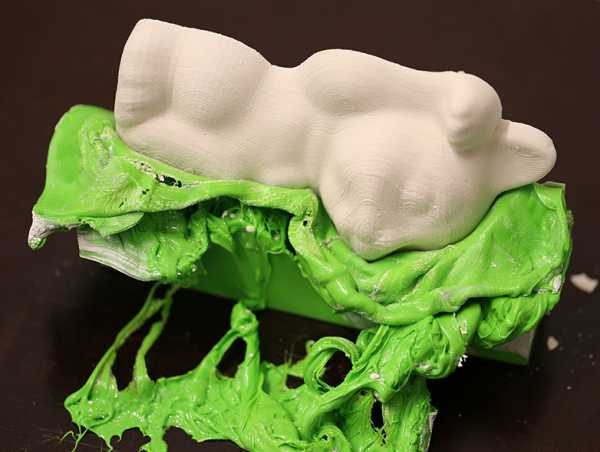
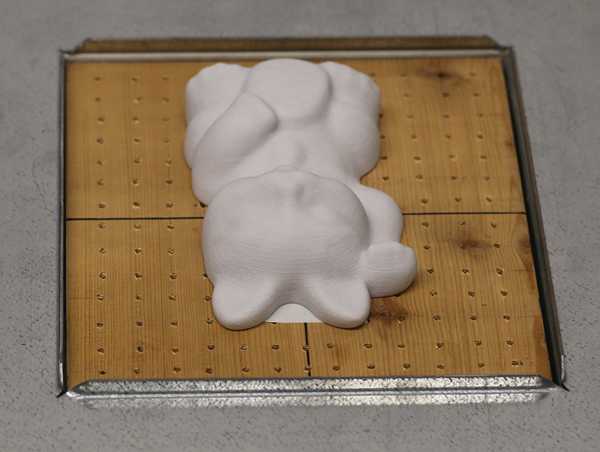
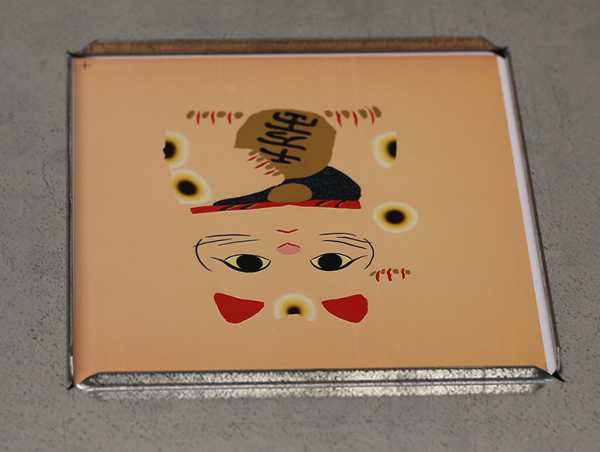
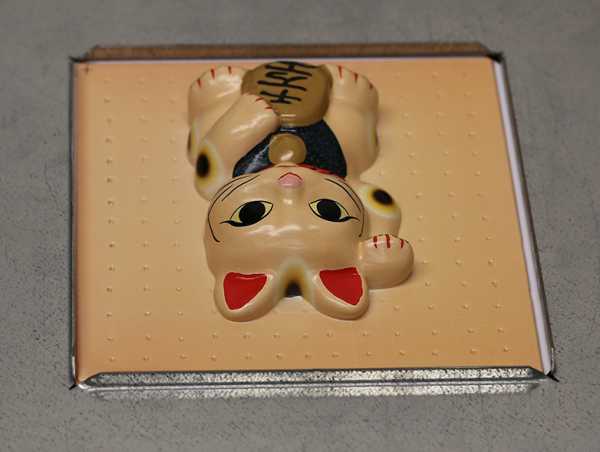
High quality replicas
The researchers tested their technique with some very complex objects, including a Chinese mask and various model-making components, such as a car body shell and food replicas.
The Chinese mask in particular has many detailed features, which were reproduced perfectly in the replica; for instance, the teeth in the original are decorated with gold paint. “This detail is reproduced exactly in the copy. The surface has a high-quality look, and the colours and structure are almost identical to those of the original,” says Schüller.
Due to the plastic used, the method is less suitable for reproducing the properties of objects made from materials such as wood or stone, since the surface has a high gloss. But this may even be preferable depending on the application.
Inexpensive technique for modellers
The researchers are convinced that the new method can be used in digital fabrication and industrial applications to mould prototypes before large-scale production. Architectural firms and modellers could also benefit from this method to cheaply and quickly fabricate a 3D model based on their plans and visualisations.
The technique may even be of interest to the hobby sector or schools, since the equipment needed is readily available and the gypsum cast can be used multiple times to produce numerous copies. The technique does not need to fear comparison with 3D colour printing processes: “The replica has a high quality appearance, and for many applications it’s cheaper and faster than today’s 3D colour printing process,” says Schüller.
Reference
Schueller C, Panozzo D, Grundhoefer A, Zimmer H, Sorkine E, Sorkine-Hornung O. Computational Thermoforming. SIGGRAPH 2016 Papers, July 24-28, 2016, Anaheim, CA. http://igl.ethz.ch/projects/thermoforming/computational-thermoforming-2016.pdf
Comments
No comments yet