Innovation is a balancing act
New manufacturing technologies will transform the way we produce things. So can we expect everything to come off a 3D printer? Mirko Meboldt, an expert in product development, talks to management expert Torbjörn Netland about the potential – and reality – of the situation.
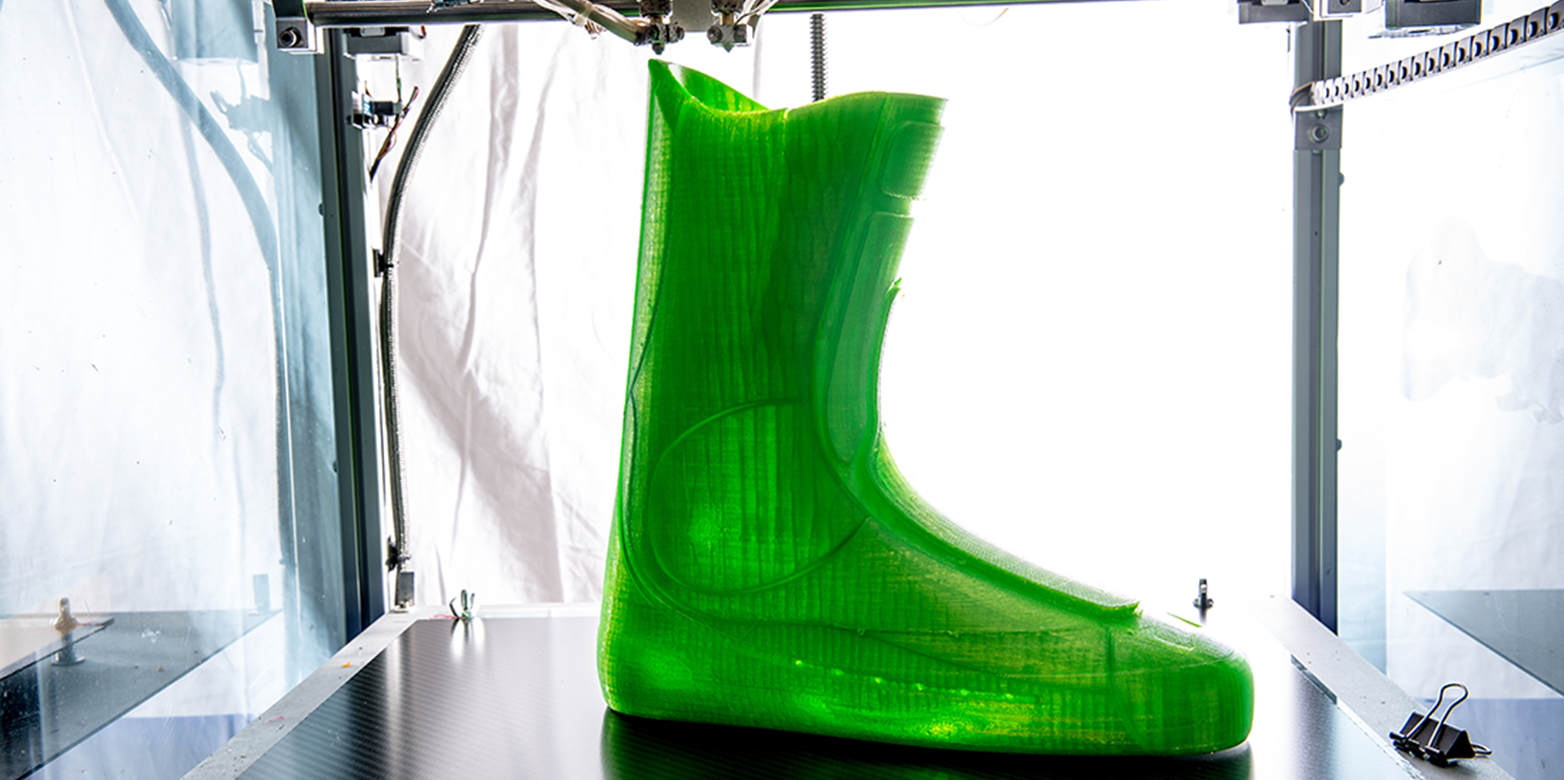
ETH News: Do you have anything 3D printed at home?
Mirko Meboldt: I made an attachment for my milling tool. It’s cheaper than buying it and I can tailor it to my own needs.
Torbjörn Netland: I have some tracks for a toy train set. It’s something of a metaphor for where 3D printing stands at the moment – which is in the hobby room. Something to play around with.
Play around? Enthusiasts are calling additive manufacturing the disruptive technology that’s going to change everything…
Meboldt: It’s a rather absurd situation. I don’t think we’ve ever had a situation where a production technology enters children’s playrooms and company board rooms at one and the same time. Never before has a technology been so over- and underestimated.
Why is that?
Netland: Often people get the wrong idea in their head. Yes, you can buy a 3D printer right now for just a few hundred Swiss francs. But it’s only going to print toys. It’s not suitable for industrial applications.
Meboldt: You have to remember that 3D printing isn’t a singular term, but instead encompasses the entire range of additive – that is to say, layer-based production techniques. These form a whole category of their own, bringing together more than two dozen different process technologies, and a whole plethora of different properties and materials.
So how do we do it all?
Meboldt: These days, there are 3D printers for ceramics, metal, plastic, wax, plaster, sand, and concrete – and for every scale. I can just as well print shapes that you can thread through the eye of needle as I can print an entire building. In other words, it’s a technology with a great many fields of application, even in medicine, where it can be used to manufacture artificial limbs or tissue replacements. It’s a huge range of techniques we’re talking about, and that is really grabbing people’s attention.
So it is a disruptive technology after all?
Meboldt: With new technologies, it’s all about the accompanying vision as well. In my opinion, technology itself is not disruptive. The disruption lies in its application, and how I as the user employ the technology within my value creation chain to generate added value for the customer or to optimise my production operation.
Could you give us a specific example?
Meboldt: I could point to the invisible “aligners” offered by Invisalign, a company founded in San Jose, California in 1999 that now has sales exceeding 1.3 billion dollars. The founding principle of alignment treatment, the patent, goes all the way back to 1945. However, it was only with the advent of 3D printing and digital technology that it actually became efficient to produce the aligners. Today, treatment begins with a mould of the patient’s teeth, which is subsequently scanned and digitalised. The orthodontist can then digitally manipulate how they want the teeth to shift over the course of the treatment. An exactly fitted aligner is printed for each stage of the treatment – 12 in all, and all for a cheaper price than one traditional set of braces – and a much better match with what the customer needs. Another example is the Swiss start-up Tailord Fits. They’ve just brought out the first tailor-made 3D printed ski boot.
Netland: Probably the best-known industry example is the injector for the LEAP engine for General Electric’s Boeing Dreamliner. It’s a relatively complicated component made up of many different individual parts. Before, it required up to 20 suppliers to manufacture. But if you produce the nozzle in one piece using additive techniques, suddenly all you need is one single supplier for the metal powder. It all goes to show that disruption isn’t about the technology itself, but rather how the techniques are used for extremely specific applications.
You're saying that it requires specific conditions?
Meboldt: Exactly so. It’s good if I can automate value-creation processes relating to design, production and distribution, or if I need structures that I can’t manufacture with any other technique. The truth is that additive manufacturing techniques are still expensive and time-consuming. I have to find the niches where the added value of the application justifies the high price of the technique. One really good example is the company Schunk, which manufactures gripper systems. Thanks to digitalisation and 3D printing, today the company can deliver each gripper – which must fit exactly to the specific component – much more easily than in the past. It’s been able to eliminate 90 percent of its previous design work while significantly reducing delivery times. This makes it all worthwhile even if producing the grippers might be more expensive.
What about in 20 years’ time? Can we expect these techniques to become cheaper in the foreseeable future?
Netland: Personally, I think that traditional processes will keep a cost advantage over additive manufacturing for most manufacturing processes over the next 20 years. However, additive manufacturing will keep getting cheaper and better, and thus gain more and more market share. Right now, for instance, 3D printing isn’t suitable for mass production – it can’t compete.
Meboldt: For companies, the critical question is how they get started with the technology and manage the learning process. It’s not about putting everything on the table all at once. The technology first has to be successfully implemented in suitable pilot projects to allow it to become a sure-fire success. The key thing is to keep on pin-pointing where the added value is within one’s own value-creation chain, what the current limits are, where the costs arise and what the business model will look like. Working through these points is a learning process, and hard work.
Netland: We’re still at the trial and error stage. 3D printing is well established in the design process – think rapid prototyping. But it is new to manufacturing, and still somewhat of an exception. Basically, what companies need is some sort of sandbox to experiment in alongside their bread and butter business. ETH is an excellent partner for that.
Read the full version of this interview in the new issue of Globe.
Slideshow
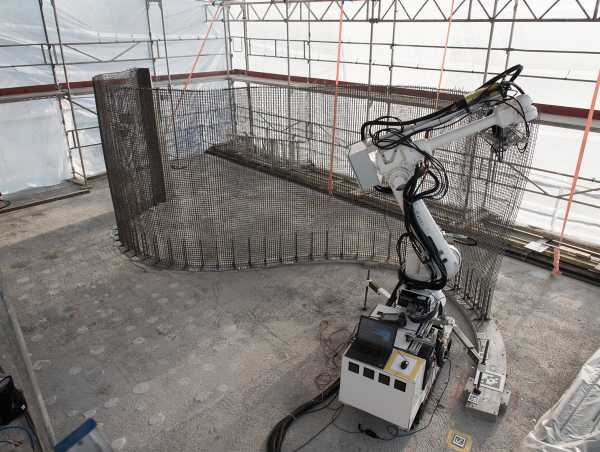
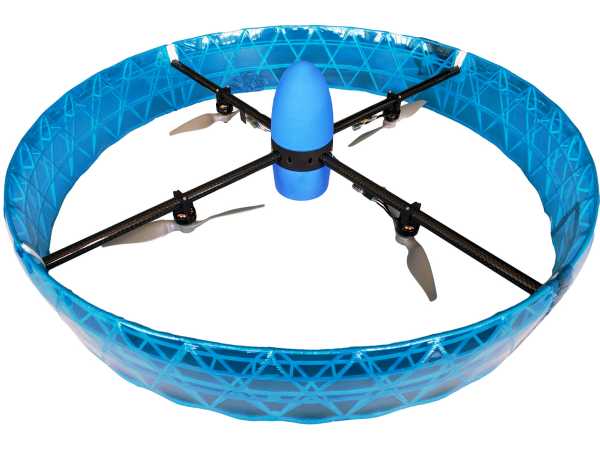
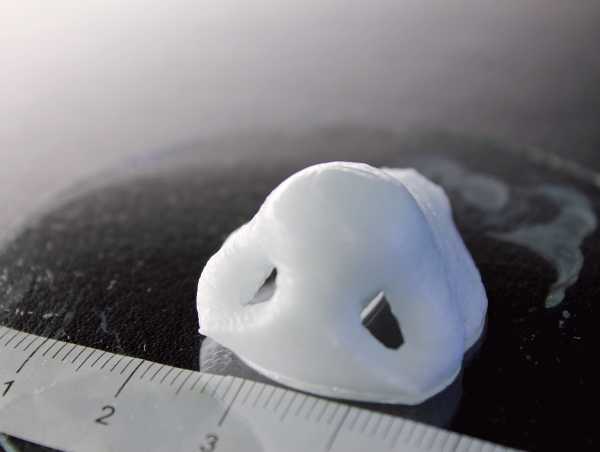
Globe: Manufacturing redifined
From microsensors to digitalized architecture, from the lab to the production floor: The new issue of Globe, the magazine for ETH Zurich and ETH Alumni, shows how new technologies like digital fabrication and additive manufacturing are creating new possibilities.
Comments
No comments yet