Materials of the future
In Paolo Ermanni’s laboratory at the ETH in Zurich, the composite materials of the future are developed. By optimizing the core elements of sandwich structures, the researchers create materials that are extremely light, robust and adaptable at once – and thus ideal for aerospace applications.
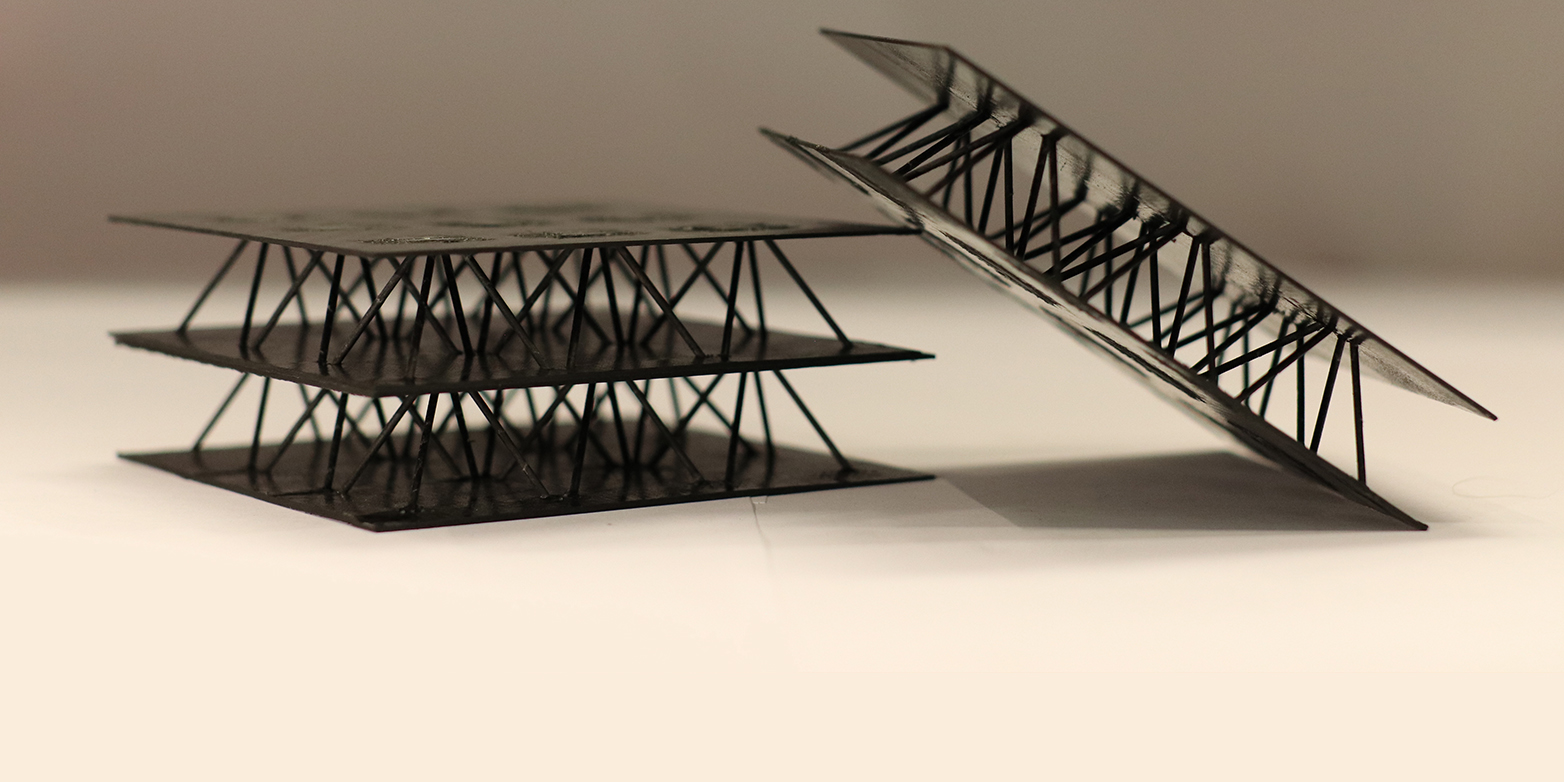
Materials that are light and robust, inherently stable and still easily adjustable, and which can also be produced sustainably and in a resource-friendly way – what may appear as impossible as squaring the circle becomes a reality day after day in Paolo Ermanni’s lab at the ETH in Zurich. “It is our philosophy to develop modern composite materials for adaptive systems and, while doing so, to optimize their structural efficiency – that is, obtaining the same performance with fewer resources or better functionality with the same amount of material”, says Paolo Ermanni, professor for Composite Materials and Adaptive Structures at ETH. At the same time, he and his collaborators investigate appropriate production processes that make the new materials interesting for practical applications.
Truss structures in sandwiches
Ermanni’s PhD student Christoph Karl takes care of the “structural efficiency” aspect. “As they feature a large stiffness and stability whilst also being very light, sandwich structures are often used for lightweight construction”, he explains. Sandwich structures typically consist of two thin and stiff cover layers and a low-density core material. “In our research we develop high-performance sandwich composites made of carbon fibre-reinforced polymers, also known as CRP’s or simply carbon fibre. In this approach, the core consists of a truss structure of carbon fibre rods”, says Karl. The good mechanical properties of carbon fibre mean that such core structures can have a larger stiffness and stability than conventional foam or honeycomb cores.
According to Karl, another significant advantage of the truss cores is the possibility of a load-optimized design: “The mechanical properties of the sandwich composite depend strongly on the core topology – in other words, on the arrangement and orientation of the rods inside the core. With the help of numerical optimizations, we can tailor the orientation of the rods to specific external loads and thus maximize the structural efficiency for a particular application.”
Applications in aerospace engineering
The core of a sandwich material constructed and optimized in this way weighs less than 30 kilograms per cubic metre (a cubic metre of steel, for comparison, weighs in at almost 8000 kilograms). “This makes our materials particularly interesting for aerospace applications, where structural efficiency is of crucial importance,” says Karl. “Moreover, it is possible to integrate additional features, such as vibration damping, directly into the core structure.” In the framework of the EU project ALTAIR led by the French aerospace lab Onera, real-life applications of the new sandwich structures are investigated. Within that project, Ermanni’s research group is involved in the development of load-bearing structures of new deployment systems for small satellites.
Futuristic car components
Flexible and adaptive structures, on the other hand, are the specialty of PhD student Oleg Testoni. Within the Strategic Focus Area “Advanced Manufacturing” of the ETH board, he develops techniques that allow one to adapt sandwich structures flexibly and dynamically. Those techniques could be used, for instance, to build futuristic spoilers or wheelhouses for sports cars that can be deformed while the vehicle is in motion in order to accurately optimize its aerodynamics for a particular velocity or wheel position when cornering.
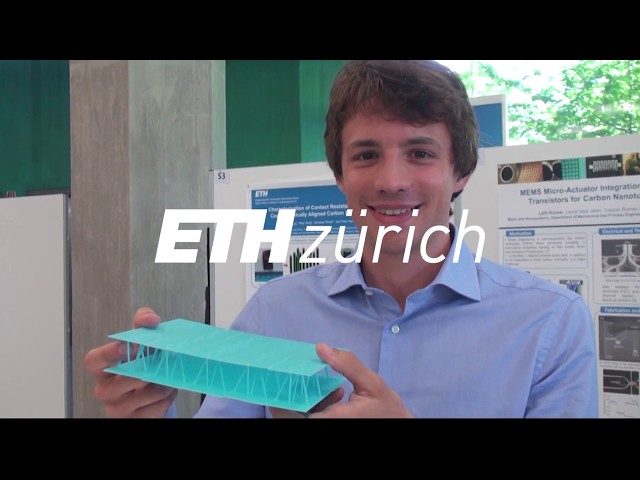
Switches in the material
To achieve such a degree of flexibility whilst maintaining the robustness of the material, semi-active elements – so-called mechanical switches – are embedded in the material. “With such switches, the rods inside the core can be temporarily loosened in order to adapt the shape. After that, they are locked in place again so that the material regains its original stiffness”, Testoni explains.
Mechanical switches can be built using “intelligent materials” such as shape memory alloys. A component made of such an alloy can take on two different shapes depending on temperature. Above a certain critical temperature, its shape changes, but when cooled down it goes back to its exact original shape. By fitting many of those mechanical switches inside the rods of a sandwich structure, one can change the shape of the entire material.
3D-printing for carbon fibre cores
Ermanni and his co-workers do not just carry out basic research on new materials, however. The spin-off company 9T Labs, co-founded by Ermanni’s PhD student Martin Eichenhofer, develops a 3D-printing technology that can be used to produce high-quality carbon fibre components such as the rods for sandwich structure cores in a robust and flexible manner. “First and foremost, this is about expanding the range of application of such materials through novel production techniques, which will enable smaller companies to use them as well. This ‹democratizes› lightweight construction technologies, as it were,” says Eichenhofer. The first products for 3D-printing are supposed to hit the market as early as 2019. “This procedure also opens up the possibility of integrating active elements directly into the printing process in the future, thus realizing 4D-printing,” Ermanni adds.
Comments
No comments yet