3D printing silicone for breathing apparatus
Right now, the 3D printers at the ETH spin-off Spectroplast are working at full capacity as never before: the young company has started producing silicone attachments for breathing masks on behalf of medical companies.
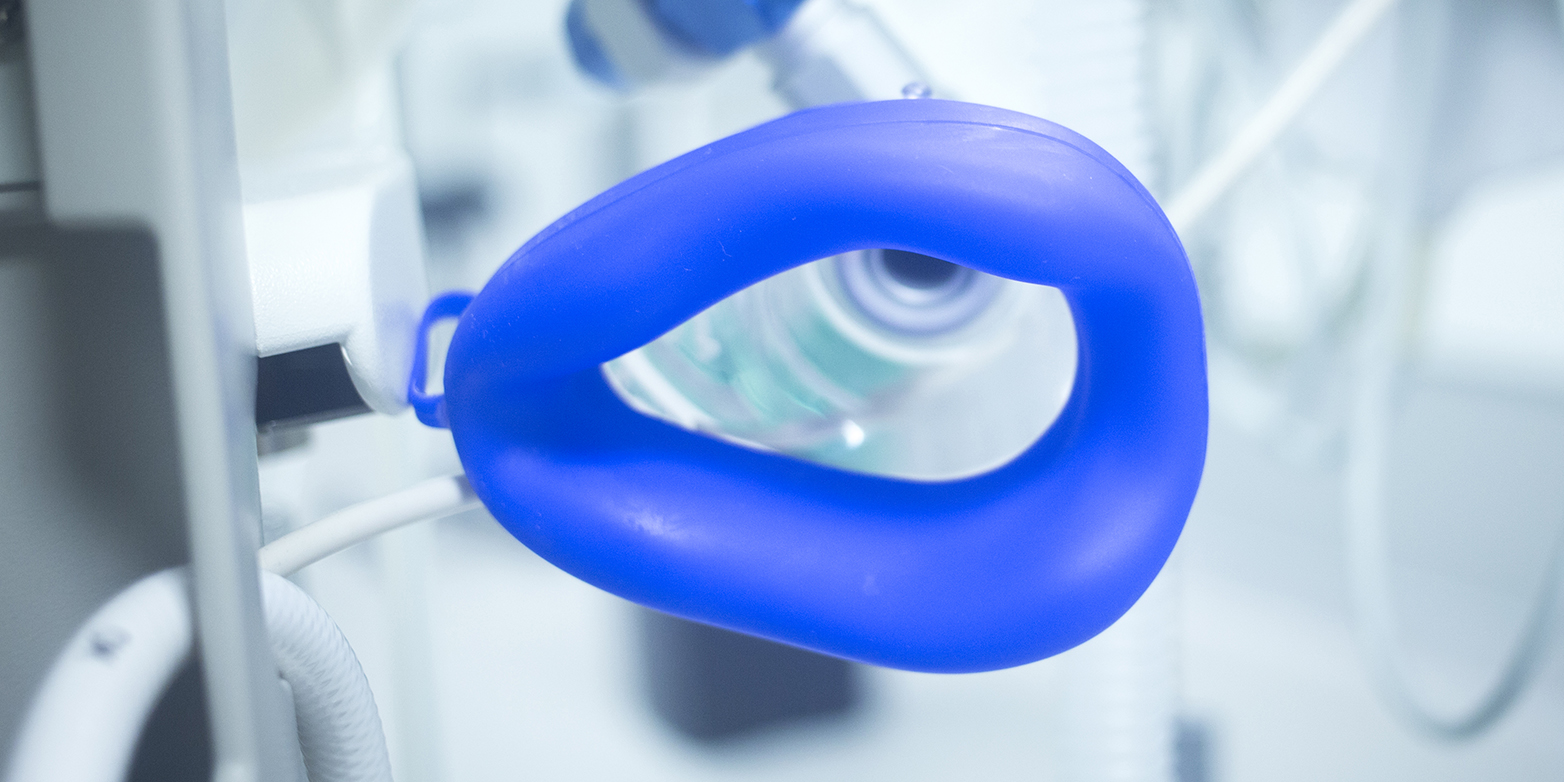
“We’re actually working pretty much flat out,” says Manuel Schaffner, a materials scientist and the CEO of Spectroplast, a young company based at ETH Zurich in Professor André Studart’s Complex Materials group. The coronavirus crisis had an effect on this young company virtually overnight – causing its order books to bulge.
This sudden increase in demand is down to the fact that Spectroplast uses a 3D printing process to produce individual customised items from silicone. This know-how is now very sought after: “The enquiries are really flooding in,” Schaffner says. One order that came in at the end of March was to manufacture seals for breathing masks.
3D printers run day and night
Spectroplast ramped up production in response. Two of the five 3D printers the company owns are running day and night to fulfil the orders for the mask seals. In addition, Schaffner and his three employees have brought two more 3D printers online. This means they now have the capacity to produce 50–70 mask seals per day. The customer provided the young entrepreneurs with the design files for controlling the 3D printers, which speeds up order processing enormously. “Normally it takes us a lot longer to print special parts like these, because we first have to clarify the customer’s needs and then make 3D scans of the desired objects,” Schaffner says.
Schaffner explains that everything is very hectic and they are currently working in shifts: “Even our sales manager is working the machines now,” he adds with a smile. However, Spectroplast has not grown its workforce; it takes a lot of prior knowledge and intuition for someone to manufacture the products at the desired level of quality.
Raw material will not run out
Should more orders come in, the team won’t run out of raw materials anytime soon. “Even before COVID-19, we’d already increased our raw materials inventory on the assumption that things might get tight,” Schaffner says. That decision has proved to be beneficial: “It means we can concentrate all our efforts on production.”
Now, the tricky part is getting the products delivered. “In the case of international deliveries, it’s sometimes taking days longer than usual,” Schaffner says. In Switzerland, on the other hand, the Swiss Post guarantees delivery at all times.
The current exceptional circumstances are challenging for the young company, but also a great opportunity to gain a foothold as a supplier in the international market. Schaffner is delighted that what he and his colleagues are doing really helps alleviate suffering in these troubled times. “The world is in crisis,” he says, “and to get through it, we’re going to need innovative ideas.”
Comments
No comments yet