Light construction, efficient operation
Boasting an intricate, doubly curved concrete roof, lightweight funicular floors, and self-learning building technology, the latest addition to Empa and Eawag's NEST research building in Duebendorf, Switzerland officially opened today. The innovative unit illustrates nearly a decade of formative ETH Zurich research in architecture and sustainable technologies.
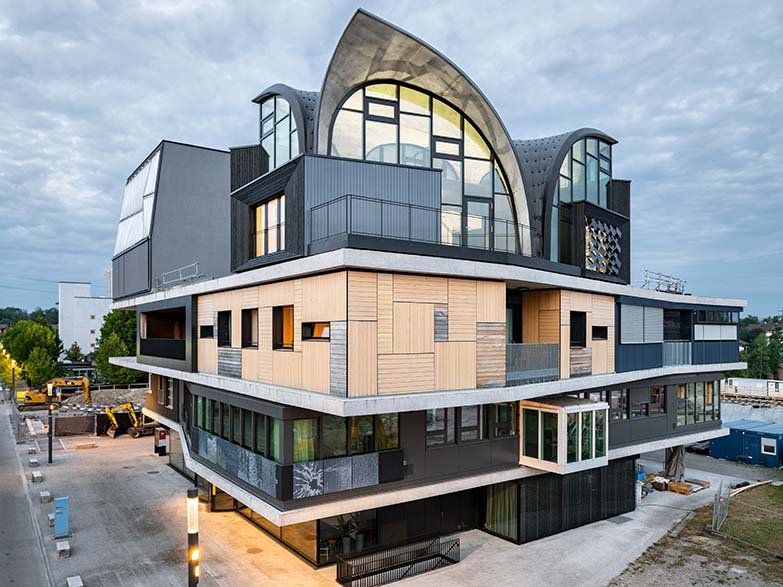
HiLo, the latest NEST unit, combines medieval building principles with futuristic construction methods: the two-storey building module with its striking, doubly curved concrete roof and novel, lightweight funicular floor system was inspired by construction methods of the past, and planned and built using state-of-the-art computational design and fabrication techniques. In the new unit, a team of scientists led by Philippe Block, Professor of Architecture and Structures, and Arno Schlueter, Professor of Architecture and Building Systems together with industrial partners explored how lightweight structures and efficient construction methods can be combined with intelligent and adaptive building systems to reduce both embodied and operational emissions in the construction and building industry.
Resource-efficient concrete structures
The unit’s striking roof derives its load-bearing capacity from its highly curved geometry combined with a concrete sandwich structure, made of two thin layers of reinforced concrete connected by a grid of concrete ribs and steel anchors. To save large amounts of formwork material, the roof was built using a flexible formwork consisting of a tensioned cablenet covered with a thin membrane onto which the concrete was sprayed.
For the mezzanine floors of the two-storey unit, the researchers primarily aimed to use as little material as possible in the structure itself. By using a rib-stiffened funicular shell instead of a flat plate, HiLo's lightweight funicular system uses over 70 percent less material than conventional floor slabs in reinforced concrete. Furthermore, digital production methods allowed the integration of ventilation, cooling, and low temperature heating systems into the floor structure for an even greater reduction in materials and volume.
Learning building technology
The HiLo unit is also equipped with an adaptive solar façade developed by Schlueter's group. It consists of 30 photovoltaic modules that can be aligned with the sun. The flexible modules can also be used to control how sunlight enters the room in order to passively heat it or reduce cooling requirements.
The adaptive solar façade is one of a series of innovative building technology components designed for efficient indoor climate regulation. During operation, the researchers consistently optimised the interplay of the individual technologies using machine learning and considering the users, in order to investigate how comfortable indoor conditions can be achieved with as little energy and emissions as possible.
Research and industry learn from each other
HiLo stands for "high performance – low emissions". The unit allows researchers to test how the construction and operation of buildings can be designed to be as energy- and resource-efficient as possible, while at the same time ensuring an attractive architectural space and a high level of comfort.
HiLo is the eighth module in the experimental NEST building on the campus of the two research institutions Empa and Eawag in Duebendorf, Switzerland (just outside of Zurich). In the modular research and innovation building, scientists and industry partners can test and advance new building and energy technologies in temporary building modules or units and under “real-life” conditions.
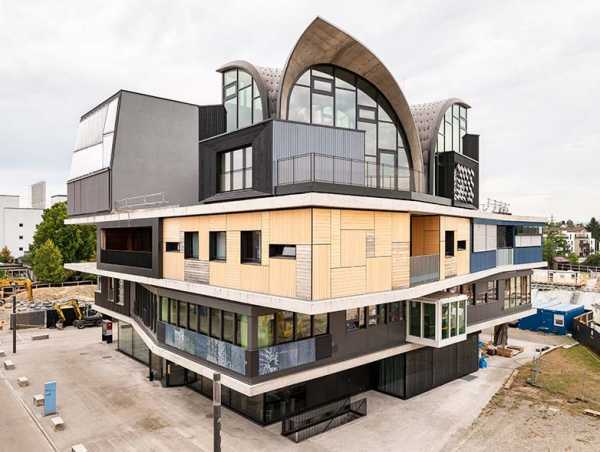
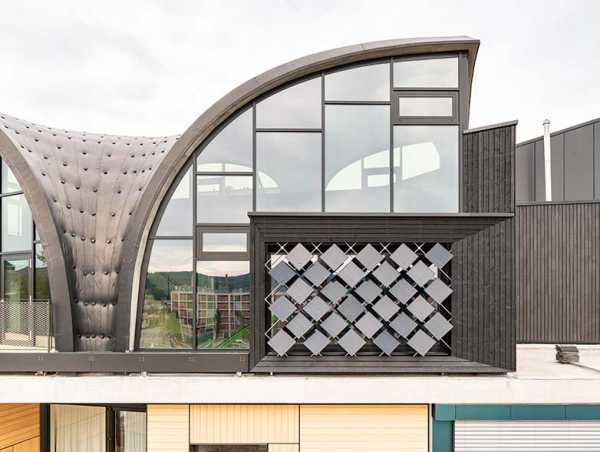
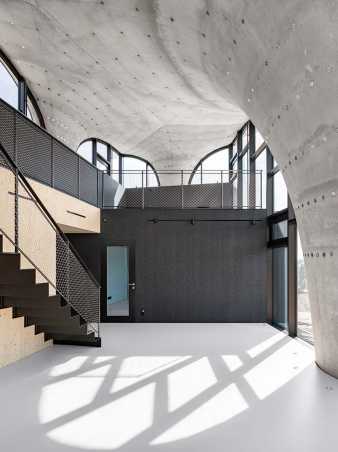
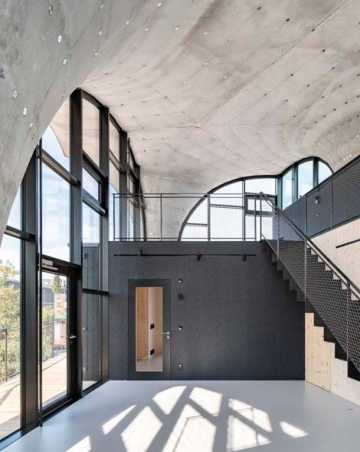
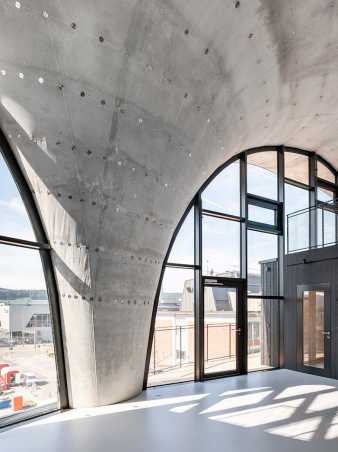
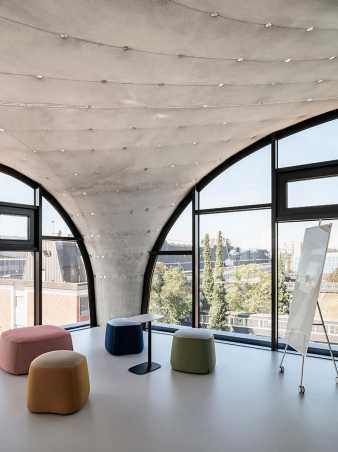
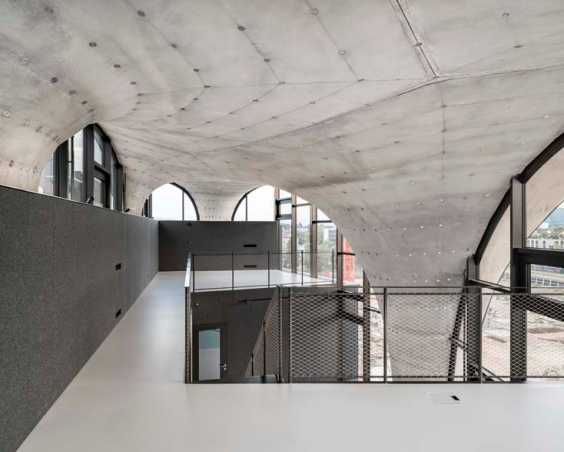
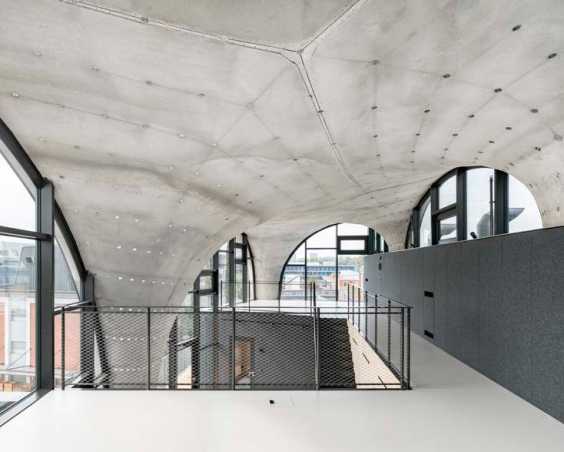
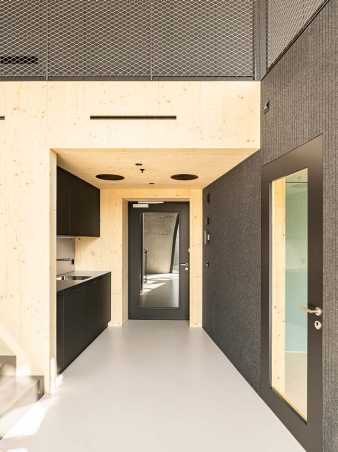
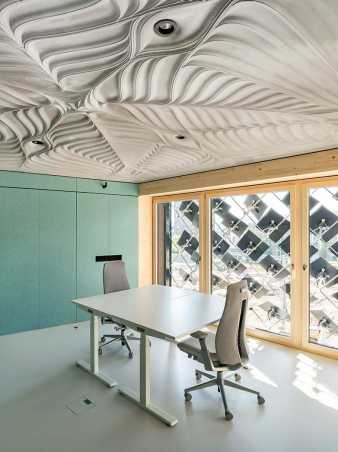
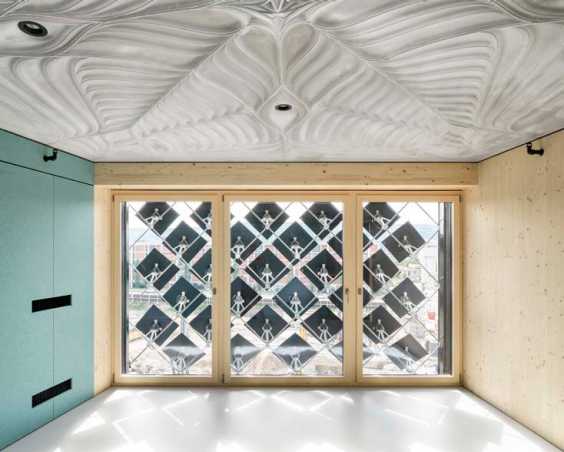
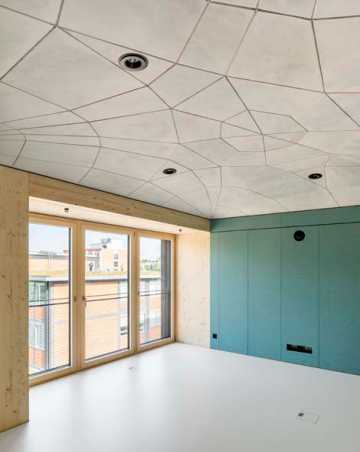
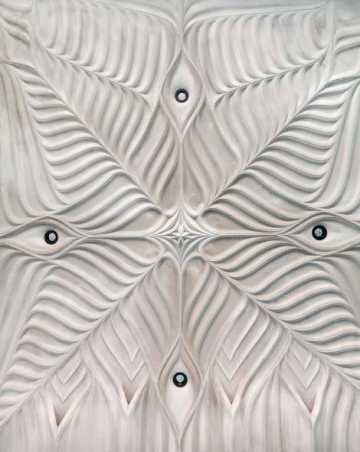
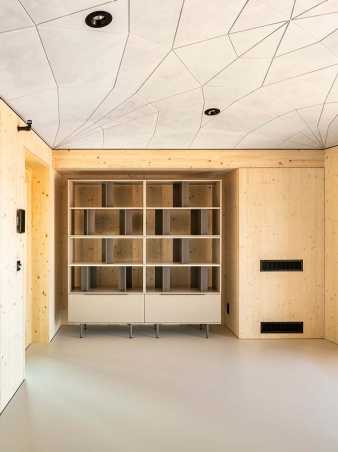
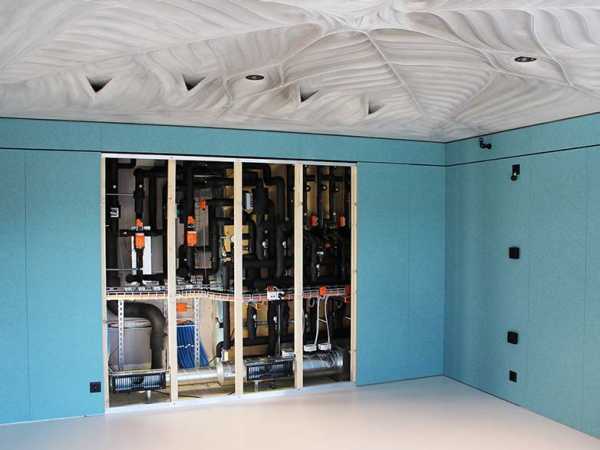
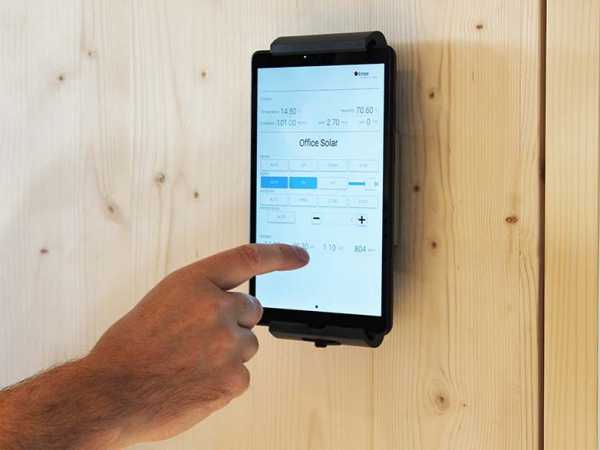
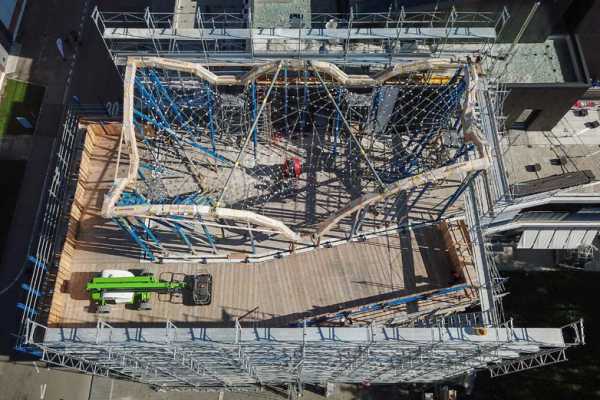
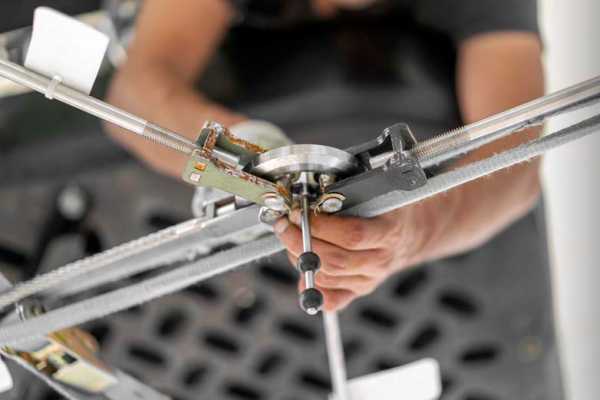
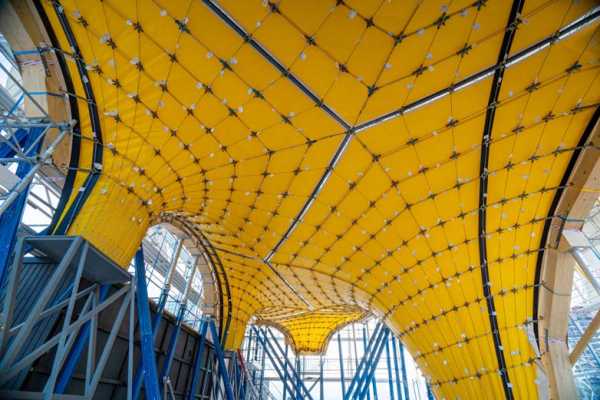
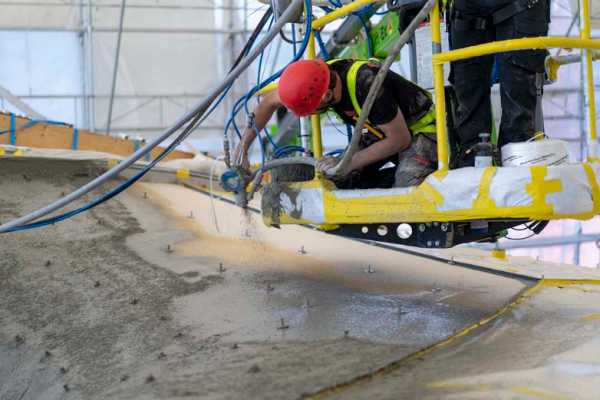
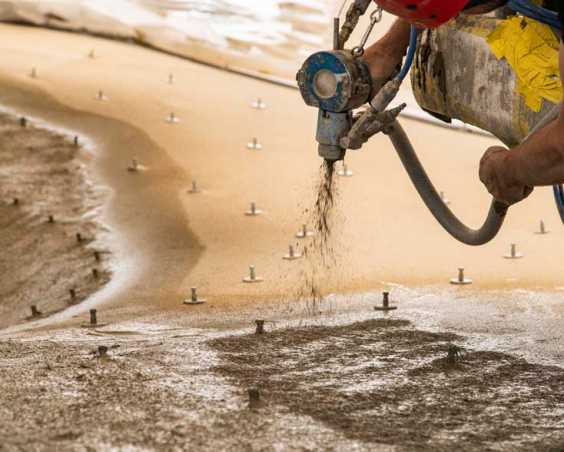
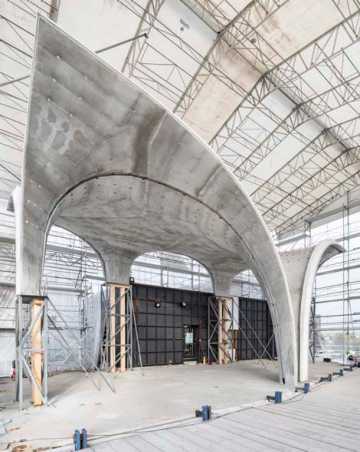
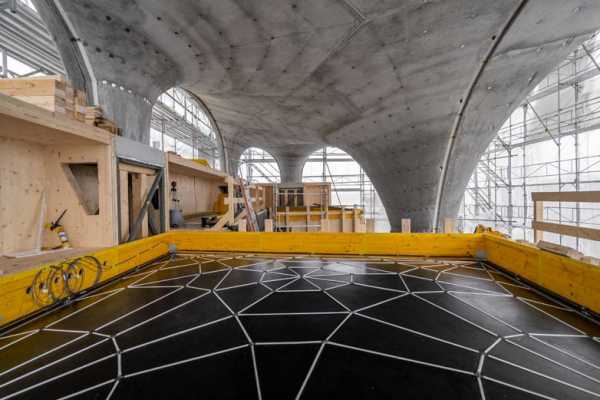
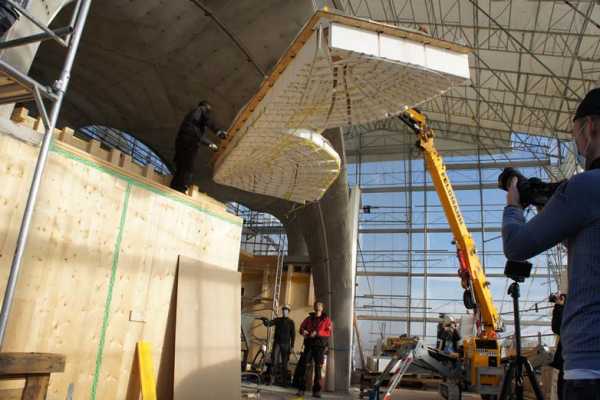
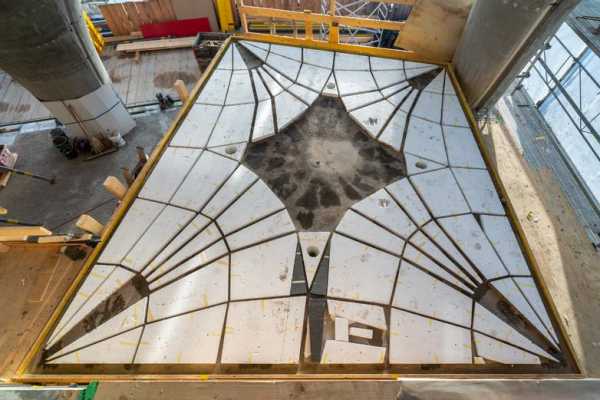
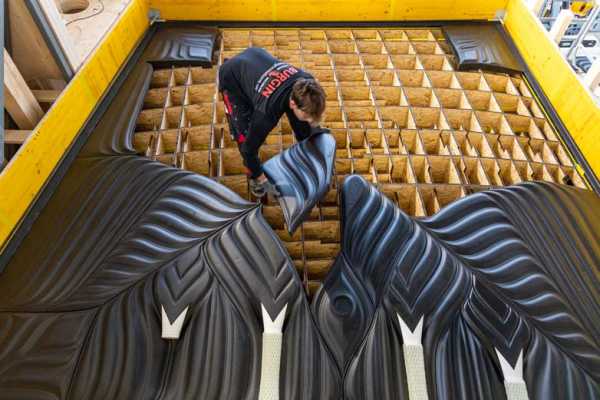
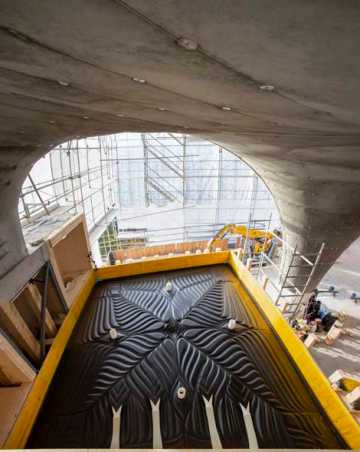
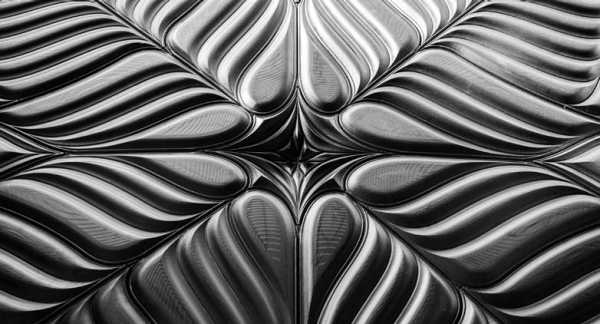
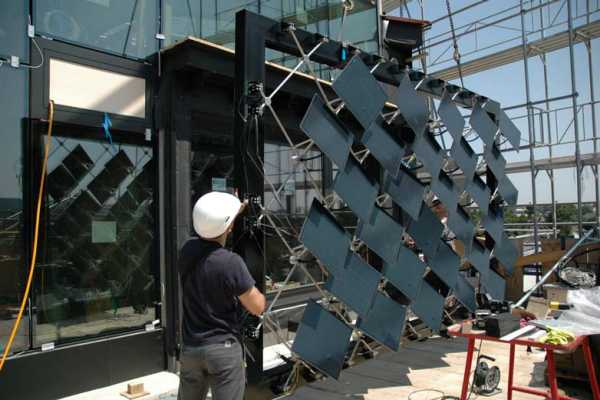
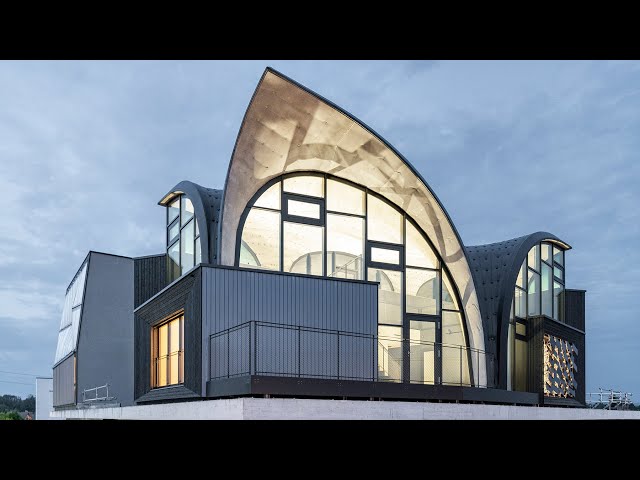
Participating research and industry partners
ETH Zurich
external page ETH Foundation
external page Autodesk
external page Belimo
external page Bouygues Energies & Services Schweiz AG
external page Bürgin Creations
external page Debrunner Acifer Bewehrungen AG
external page Doka Schweiz AG
external page Feller AG
external page Flisom AG
external page Haworth
external page Holcim (Schweiz) AG
external page Impact Acoustic AG
external page Künzli Holz AG
external page Marti AG Bauunternehmung
external page Mensch und Maschine
external page Mitsubishi Electric R&D Centre Europe B.V.
external page NCCR Digital Fabrication
external page Pletscher Metallbau
external page R. Nussbaum AG
external page ROK Architects
external page SageGlass
external page Sika AG
external page Vetrotech
Comments
No comments yet