Compost for Kenya
Manuel Mathis is doing an internship at a composting plant in Nairobi as part of his Master’s degree programme. He is now in charge of a 20-strong team of workers – and, thanks to his improvements, the business is back in profit.
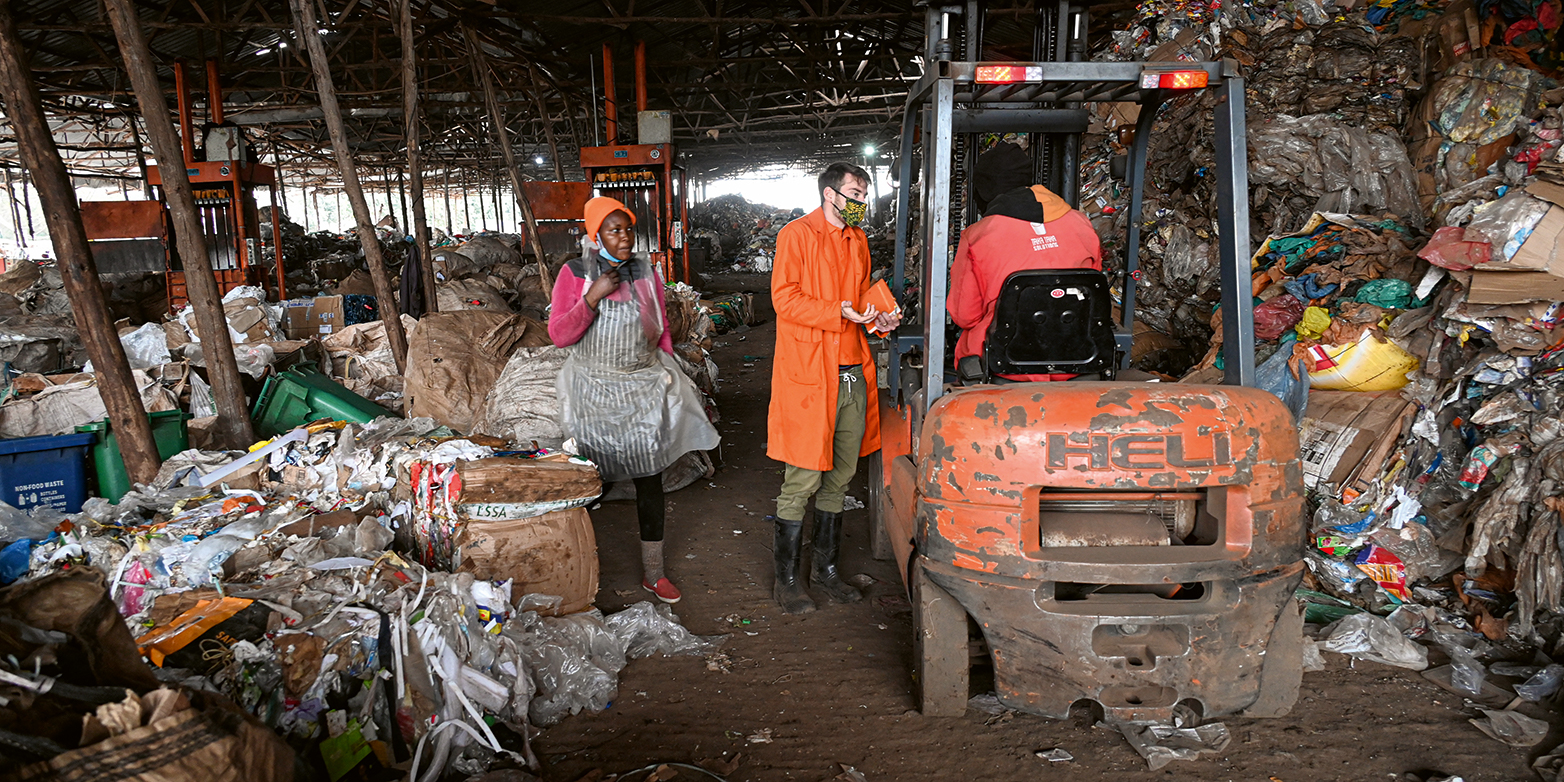
Manuel Mathis still remembers the human geography class that made such a lasting impression on him at secondary school. His teacher explained that millions of people go to bed hungry each night, in part due to the erosion and diminishing fertility of the soil they use to grow their crops. There and then, Mathis resolved to pursue a course of study that would help to alleviate hunger and poverty. In 2015, he enrolled at ETH and embarked on a degree programme in agricultural sciences. He was bombarded with huge amounts of theory about soil-plant systems, yet he yearned to spend more time digging in the soil to get hands-on experience. This led him to take a job, alongside his studies, at a composting plant in Fehraltdorf in October 2020. “The practical experience I gained there has served me well,” says the 25-year-old student on a Zoom call in late September. He is sitting in the living room of his apartment in the centre of Nairobi, looking rather under the weather. It turns out he is fighting off another in a series of nasty stomach bugs. “It’s a natural consequence of working here,” he explains. “I get pretty close to all sorts of unfamiliar viruses and bacteria!”
A chaotic start
Since May, Mathis has been working at the composting plant run by the privately owned recycling company TakaTaka Solutions in Kenya’s capital Nairobi. Each day, he jumps in a white Nissan Estate and drives 20 minutes from his apartment to the 8,000-square-metre site on the city outskirts. When the idea first came up to do the internship for his Master’s degree at the plant, the plan was simply for Mathis to set up a small lab to help the workers monitor the pH, ammonium and nitrate content of the compost – all key indicators of high compost quality. But things worked out rather differently.“When I got here, everything was in total chaos,” says Mathis. “The whole plant was overflowing with fresh organic waste; the raw materials were just piling up everywhere rather than being turned into compost!” He then discovered that most of the workers had recently been dismissed for theft, and the plant’s long-time manager had gone on holiday, exhausted by the relentless workload. The only people left were two new, inexperienced workers and a tractor driver, who was reasonably familiar with the site, but who spent most of his time repairing the wheels of the only available tractor, which were constantly breaking down. “Everyone else gave the area a wide berth because of the terrible smell,” says Mathis.
After overcoming his initial shock, the student took stock of the situation. He quickly identified that the two key problems were profitability and infrastructure. The quality of the compost was so poor that its former buyers – most of whom were large agricultural suppliers – had turned their backs on the company after seeing the results of their own lab analyses. With no buyers for the decomposed compost, or humus, it was simply stacking up on site and the business was no longer making a profit. Mathis approached the company founder – a philosophy graduate with a German passport who had grown up in Nairobi – and persuaded him to order a new tractor from China as well as buying new wheels for the old one. Only then were they able to shift the towering piles of waste and line it up in long, 1.5-metre-high rows where the process of controlled decomposition could begin. The owner also agreed to invest in a new sifter to speed up the sieving process and relieve the bottleneck.
At the same time, Mathis quickly began recruiting workers. By November, he had a team of 20 people working at the plant. Their main job is to remove contaminants from the organic waste, such as old batteries, plastics and metal parts. Mathis knew from the start that everything relied on establishing a good working relationship with these untrained workers, each of whom was taking home a modest salary of 100 dollars a month. “Most of what I know about leading and motivating a team comes from my ten years of youth work in the church,” he says.
"What I learned at the ETH above all is to acquire things myself."Manuel Mathis, Master student
Advice via WhatsApp
Within a few weeks of arriving in Nairobi, Mathis was coordinating the entire workforce, drawing up work schedules and teaming up with the tractor driver to manage day-to-day operations at the plant. Support also came from Switzerland in the form of Jacques Fuchs, a family friend who had also studied agricultural sciences at ETH in the 1980s. After completing his doctoral studies in the Plant Pathology group, he became a composting consultant, providing advice to compost projects all over the world – including TakaTaka Solutions. This was how Mathis had ended up choosing Kenya in the first place. “I often turned to Jacques for technical advice, especially in those first few weeks. It was great being able to chat to him on WhatsApp from the plant,” says Mathis. In fact, Mathis was pleasantly surprised by how well it worked and how good internet coverage was in Kenya.
In mid-July, Fuchs flew to Nairobi for a week to help Mathis make further improvements to processes and infrastructure so that things would run even more smoothly. “Composting offers huge potential to increase crop yields, not just in Kenya but all across Africa,” Fuchs explains. He says this partly comes down to the climate, but also to the fact that many soils are hardly ever fertilised. What’s more, he adds, a nutrient-rich soil protects plants from many kinds of diseases.
Kenya is certainly not short of raw materials for producing humus. According to government figures, the country generates 22,000 metric tons of waste a day, with an ever-increasing proportion coming from the fast-growing cities. Official forecasts indicate that the urban population will be generating some 5.5 million metric tons of waste a year by 2030, three times as much as the figure for 2009. Most of this waste currently ends up in open landfills on the outskirts of Kenya’s cities or is incinerated by the people who generate it, in both cases harming people’s health and damaging ecosystems. Yet between 60 and 70 percent of this waste is organic and could therefore be composted. In other words, the future looks bright for humus production – and for TakaTaka’s business model.
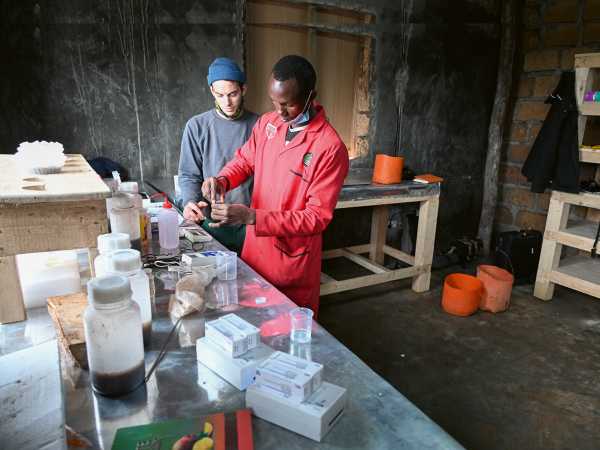
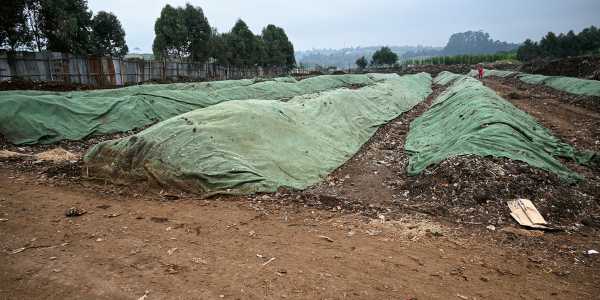
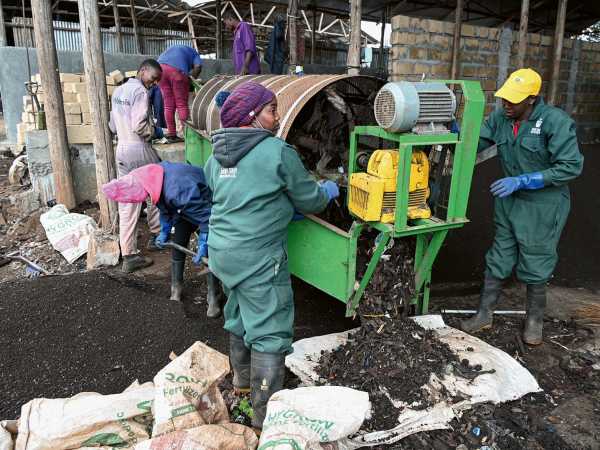
Googling and improvising
After five months of hard work, the once-neglected plant has returned to profitability, says Mathis. His team is currently producing around 90 metric tons of humus a month, enough to supply 1,000 hectares of land, roughly the equivalent of 50 medium-sized farms. This is well above the break-even point for the business, which Mathis says is around two-thirds of what they are currently producing. To find new buyers, Mathis has invited potential customers to the plant and promoted the business at agricultural fairs. He has also introduced regular checks to ensure that TakaTaka Solutions can guarantee humus of a consistently high quality in the future. Every compost heap now has its temperature logged; this can reach 80 degrees Celsius early in the composting process, dropping to 45 degrees when the compost is ready for use. The team also checks the moisture content regularly and adjusts it as necessary, using a recently purchased water tank and hose; compost that is dripping liquid is too moist, while crumbly compost is too dry. Mathis and his workers also knocked together a little shed to house a lab, and he managed to fabricate a rudimentary shaker for sample preparation, using the materials he had on hand. “One of the key things I learned at ETH was how to improvise your way to a solution,” says Mathis. Much of the knowledge he has picked up over the past few months is the result of hours of googling followed by much tinkering and experimentation.
In July, the founder and CEO of TakaTaka Solutions asked him to extend his internship by three months. Mathis will now spend the rest of the year training Fidelis Mutie Muendo, an agricultural scientist from Kenya, who will then take over the management of the composting plant. At the same time, he will be helping TakaTaka Solutions push ahead with plans for a second composting plant in Mombasa, the country’s second-largest city, on the Indian Ocean. With 400 employees already on its payroll, the company is growing fast and soon hopes to expand its services to other East African countries. “Actually, there’s enough work for me to stay another year here!” says Mathis wryly. But his time is nearly at an end, and in late December he will be heading to Bukavu – a city in the easternmost part of the Democratic Republic of the Congo – to work on his Master’s project. His research work will form part of the RUNRES project, which is led by Johan Six, ETH Professor of Sustainable Agroecosystems. Mathis’s goal will be to find ways of making Congolese consumers more aware of the need to sort their waste at source – and to motivate them to play their part. Because – as Mathis now knows from first-hand experience – the more carefully waste is sorted, the higher the quality of the humus at the other end of the recycling process.
This text appeared in the 21/04 issue of the ETH magazine Globe.
Comments
Additional comments are available for the German version of this article. Show all comments
Hi Manuel! Are you interested in trying to do the same thing as you have done in Nairobi in Lebanon in the very sad situation the country is going through? Of course neither the political nor the economical nor the geographical environments are the same. If interested please get in touch with me per email first! Thanks in advance for your eventual cooperation and hope for an interest!
Very impressive, thank you for sharing Manuel Mathis' experience in Nairobi. Having an impact in such a short time span means he hit the ground running, which is quite a feat. Well done, and great that such Masters Programmes are possible.