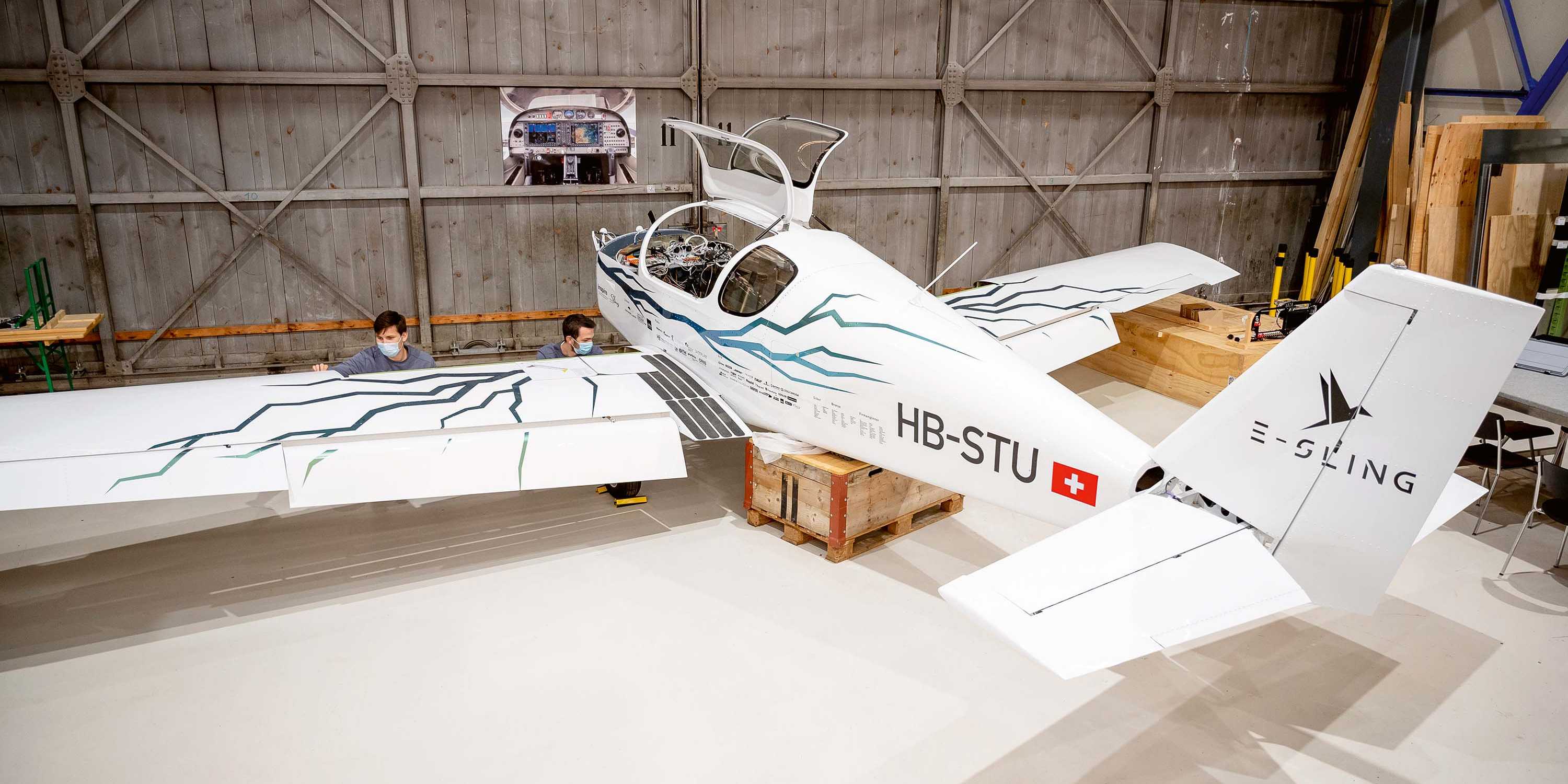
Getting into the air
Eight ETH students are working on battery and hydrogen versions of an electric aircraft as part of the e-Sling focus project. For the past year, their lives have revolved around Hangar 3 at the Innovation Park Zurich in Dübendorf.
- Read
- Number of comments
The midday sun casts a warm summery light on Hangar 3 next to the Dübendorf military airfield, evoking a holiday mood as it softly illuminates the runway and the landscape beyond. But holidays are the last thing on the minds of the eight ETH students who have been here since autumn 2021. The team of one woman and seven men – all aged between 20 and 24 – spends up to six days a week working on a small electric aircraft and its battery and hydrogen propulsion systems. Built from a kit supplied by South African aircraft manufacturer Sling, the small airplane – which stands proudly amid workbenches and various pieces of equipment – has become the main focus of many of these students’ lives.
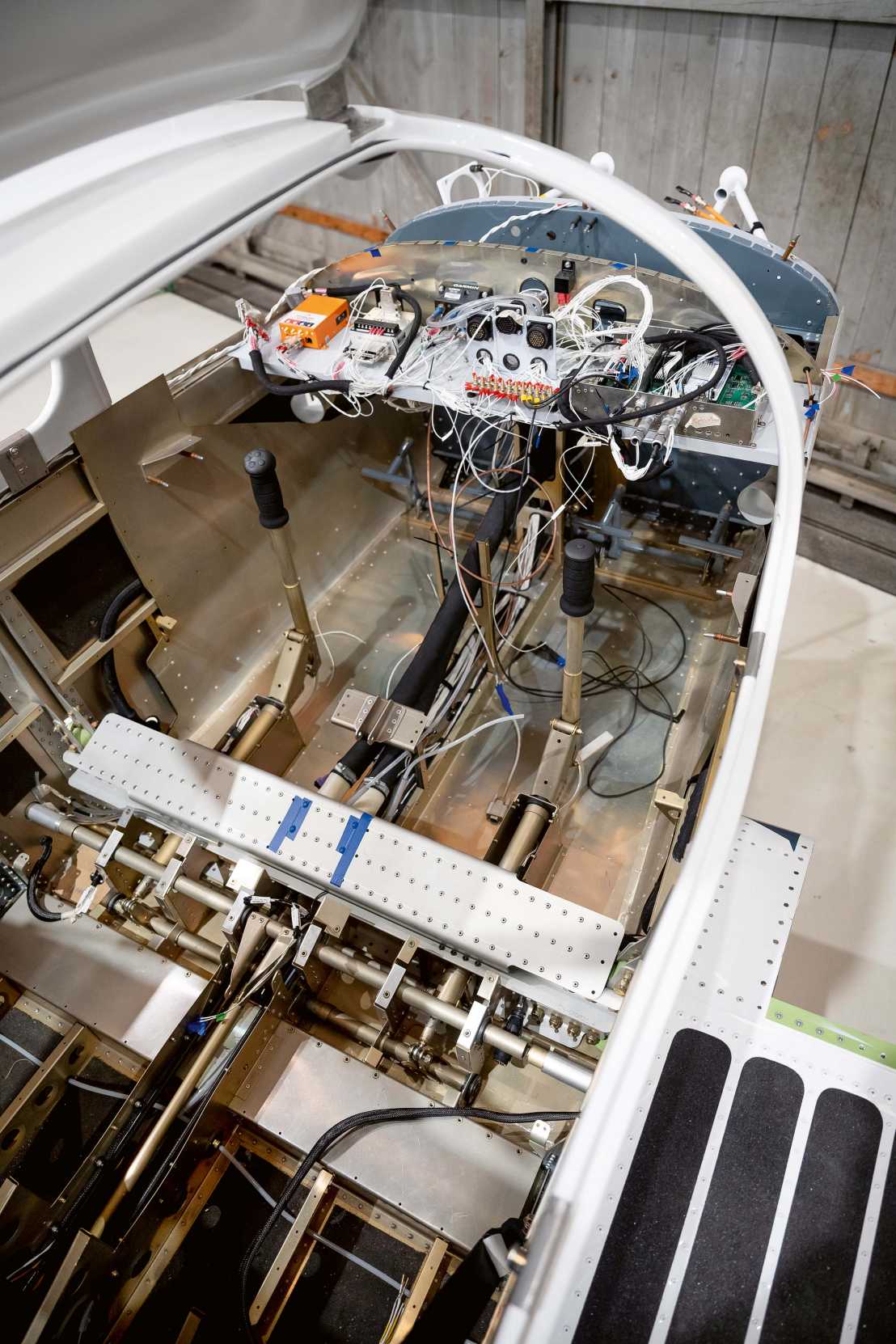
The e-Sling has a wingspan of 10.5 metres, a maximum take-off weight of 950 kilograms, a cruising speed of 160 kilometres an hour and an estimated range of 250 kilometres. Instead of running on fossil fuels, it will eventually be powered by a 240-kilogram battery consisting of almost 3,000 individual cells. Right now, however, the section of the plane where you would expect to find an engine and propeller is nothing but a mass of loose connections. What will eventually be a four-person cockpit with screens, displays and switches is currently just a tangle of cables – and there are gaping holes in both wings where the batteries should be. In other words, it doesn’t look like this aircraft will be taking off any time soon.
Project flatshare
Stairs at the back of the hangar lead up to a steel platform where the project team are sitting at a round table, finishing off their lunch break with coffee and biscuits. The platform feels rather like a student flat: it has a compact kitchen with a dishwasher, coffee machine and microwave, plus a sofa, lockers and six computer workstations. Everything you need for a comfortable flatshare!
Colin, Elsa, Jan, Joël, Patrick, Rafael, Robin and Sander clearly feel very much at home here, and the relaxed atmosphere suggests that these eight students have already spent a lot of time together. They all study mechanical or electrical engineering, but their bond goes far deeper than that: each of them has agreed to dedicate a year of their lives to a focus project, which requires them to develop a realistic product, taking it from the design phase right through to production and potential commercialisation. The e-Sling project was launched in September 2020. The first team spent 12 months developing all the components required for the battery-powered version of the plane. However, they didn’t have time to finish testing the aircraft’s new propulsion system and to obtain the necessary approval for its maiden flight.
So this task has now fallen to the current team, which comprises Elsa Wrenger and her fellow students: “We’re expecting to get the plane developed by the first team up in the air by the summer,” says the 21-year-old, who comes from Munich. But that’s a lot harder than it sounds.
Battery lab in container
A shipping container sits rather forlornly in front of the hangar. Inside these cramped quarters, the airplane’s engine and propeller have been jacked up and are connected to a computer by a mass of cables. The two battery modules are on the floor, plugged into the charger. They take three hours to reach full charge, which will be enough to keep the plane in the air for about an hour. “This is our battery lab,” says 23-year-old Jan Wallimann, the team member responsible for the aircraft’s battery system. “It’s where we test battery performance and check they work properly with the engine and the control system.”
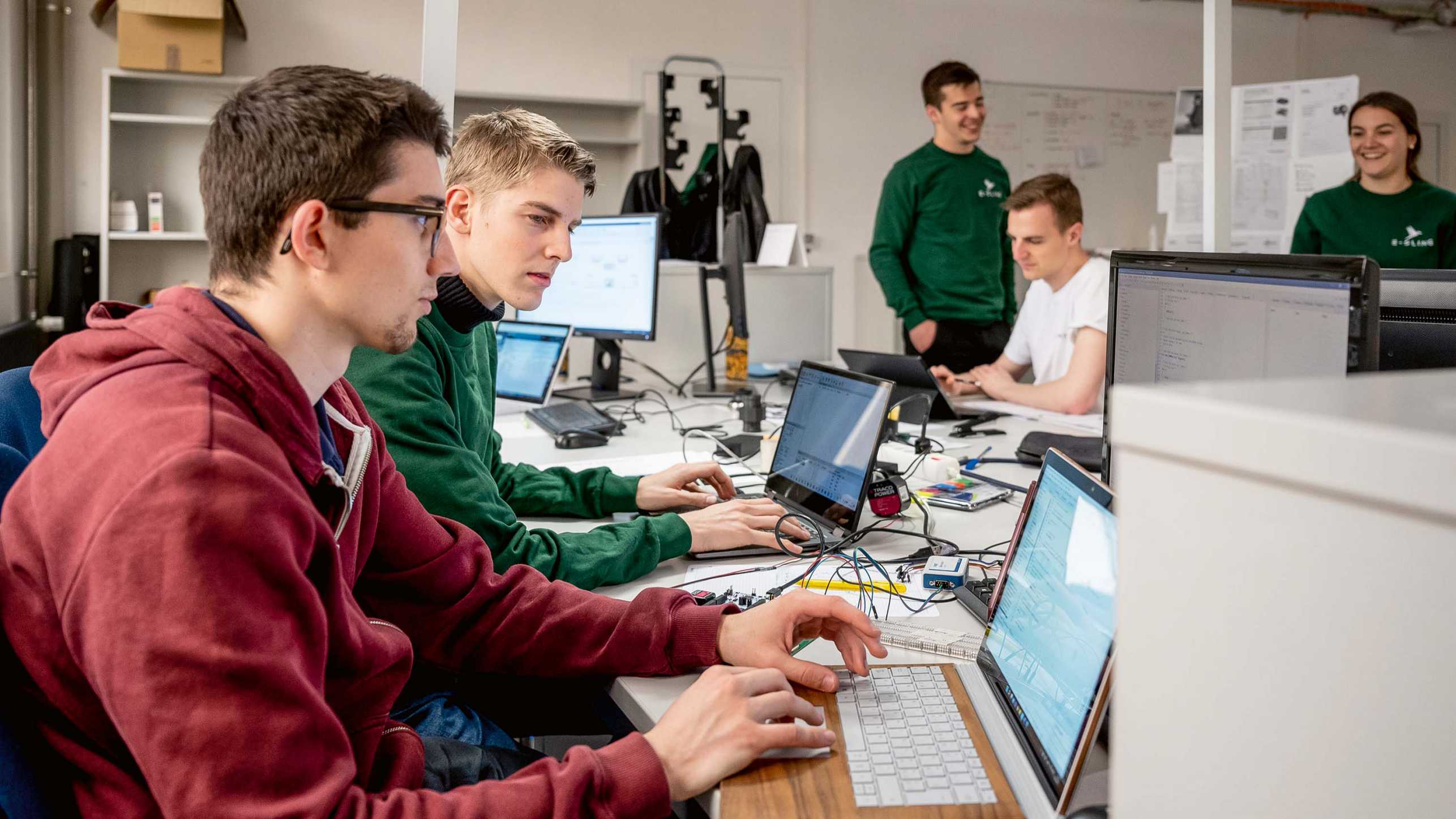
To do this, the students developed their own software, which collects data from 150 sensors. “We even came up with an app that lets us check the temperature and voltage of the individual battery modules on a smartphone while we’re sitting at home on the sofa,” says Patrick Benito, who programmed the software. The students clearly take pride in understanding every last inch of their airplane.
Focus project = Problem solving
Being part of a focus project means tackling a constant stream of surprises, and that’s certainly true of e-Sling. It was the previous team who first noticed that every time they started the propeller, the cockpit electronics would shut down and take the rest of the control system with them. Once this happened, the engine could no longer be operated via the control lever – a situation that obviously has to be avoided at all costs once the plane is airborne. Unfortunately, the original team ran out of time before they could fix the problem.
That left Jan, Elsa and the other members of the current team to come up with a solution. After puzzling over it for two months and performing numerous tests and measurements, they finally figured it out: “We realised that the engine and all the cables that run to the batteries via the cockpit were producing an electromagnetic field that interfered with the electric signals in the cockpit,” says Jan. The solution was to prevent that field from forming.
Deciding how to do that was very much a mechanical problem, so much of the work fell to Joël Meyer: “After countless attempts, we finally managed to solve the problem by making various modifications, including re-routing the cables and mounting a cover plate on the engine.”
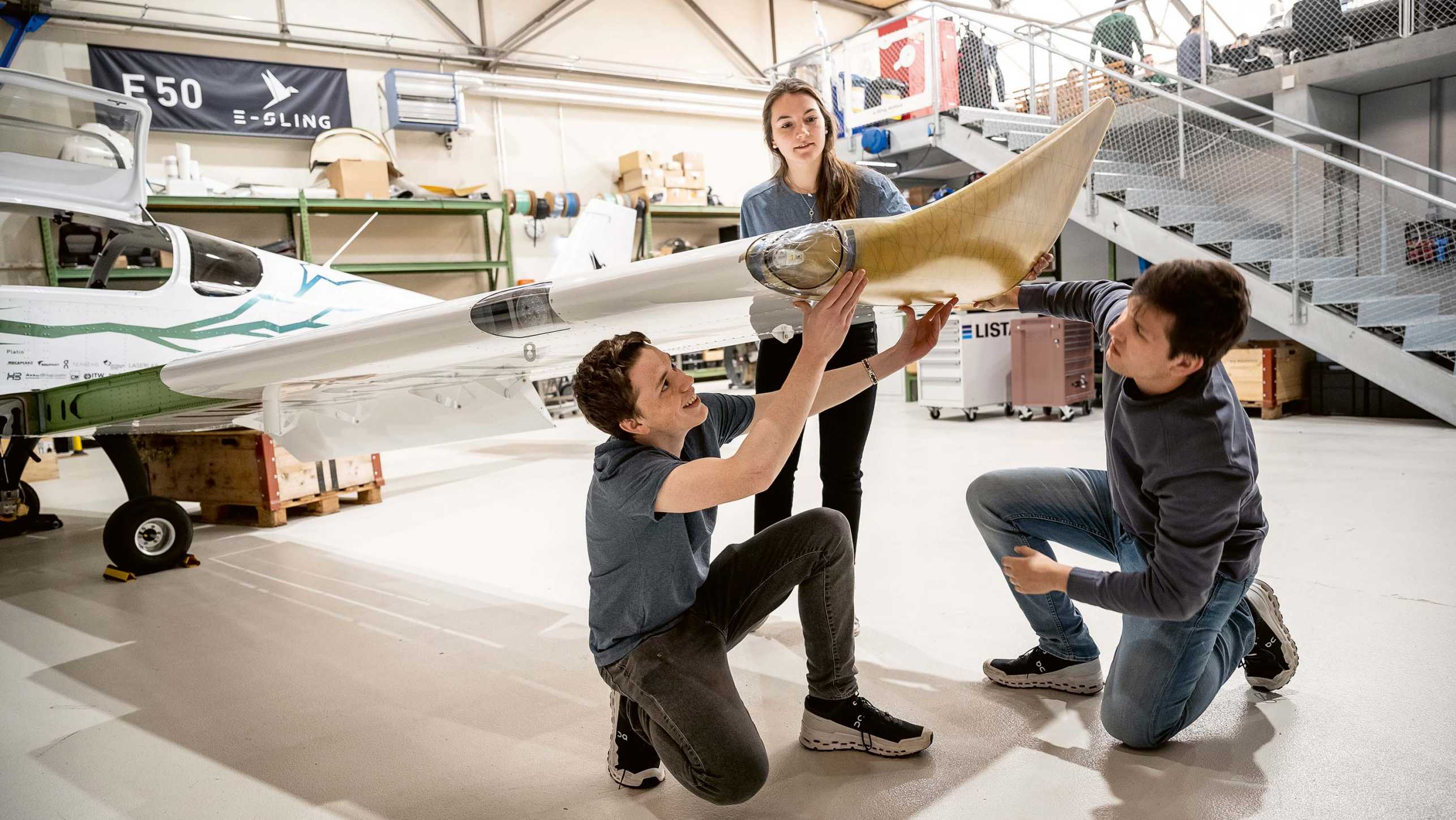
A formative experience
This is what makes focus projects so exciting: the experience of encountering new problems and solving them as a team. To find a solution, the students cannot simply rely on their textbooks and lecture materials; they also need to apply scientific and technical principles to get the job done, just like real engineers. As well as doing research and asking experts from industry and academia, they also have to put their heads together and improvise, because it’s rare to find an off-the-shelf solution that ticks every box.
The aspiring engineers are keenly aware that they are likely to face a barrage of further obstacles, both big and small, before their aircraft finally takes off this summer. Yet they still seem remarkably undeterred. So what motivates them to plough so much time into this project?
“There’s no way anyone would do it just for the ECTS credits, because you only get 14 for the entire year!” says Sander Metting with a grin. The 23-year-old mechanical engineer, who moved into a shared flat in Dübendorf for the duration of the project, argues that the biggest benefit is the huge amount of practical experience it offers to students who are still doing their Bachelor’s degree. Being able to apply the knowledge you gain from lectures and seminars to develop something from scratch is a unique opportunity, he says. That’s why applications for focus projects always outstrip the number of places available, so students need to show tremendous commitment before they even get through the selection process.
“We want to show that there are alternatives to fossil fuels in the aviation sector.”Elsa Wrenger
Most of the group also have a passion for aviation and are keen to experience the process of building an aircraft first-hand. Some are even considering a career in the aircraft industry after they graduate. Yet they are motivated by other reasons, too. “We want to show that there are alternatives to fossil fuels in the aviation sector,” says Elsa. Personally, she hopes her participation will contribute in some small way to making air travel more sustainable.
Next step: Hydrogen propulsion
Back in the hangar, a few of the team members have gathered around a big table to work on the second part of the project: developing a hydrogen powertrain for a small aircraft. Their aim is to make this sufficiently lightweight and powerful to keep the plane airborne for as long as possible. But hydrogen propulsion alone cannot provide all the power required: “You need a lot of power on take-off and landing and when you encounter turbulence in the air. That means you need batteries as a backup to make sure all those power requirements are met,” says Sander.
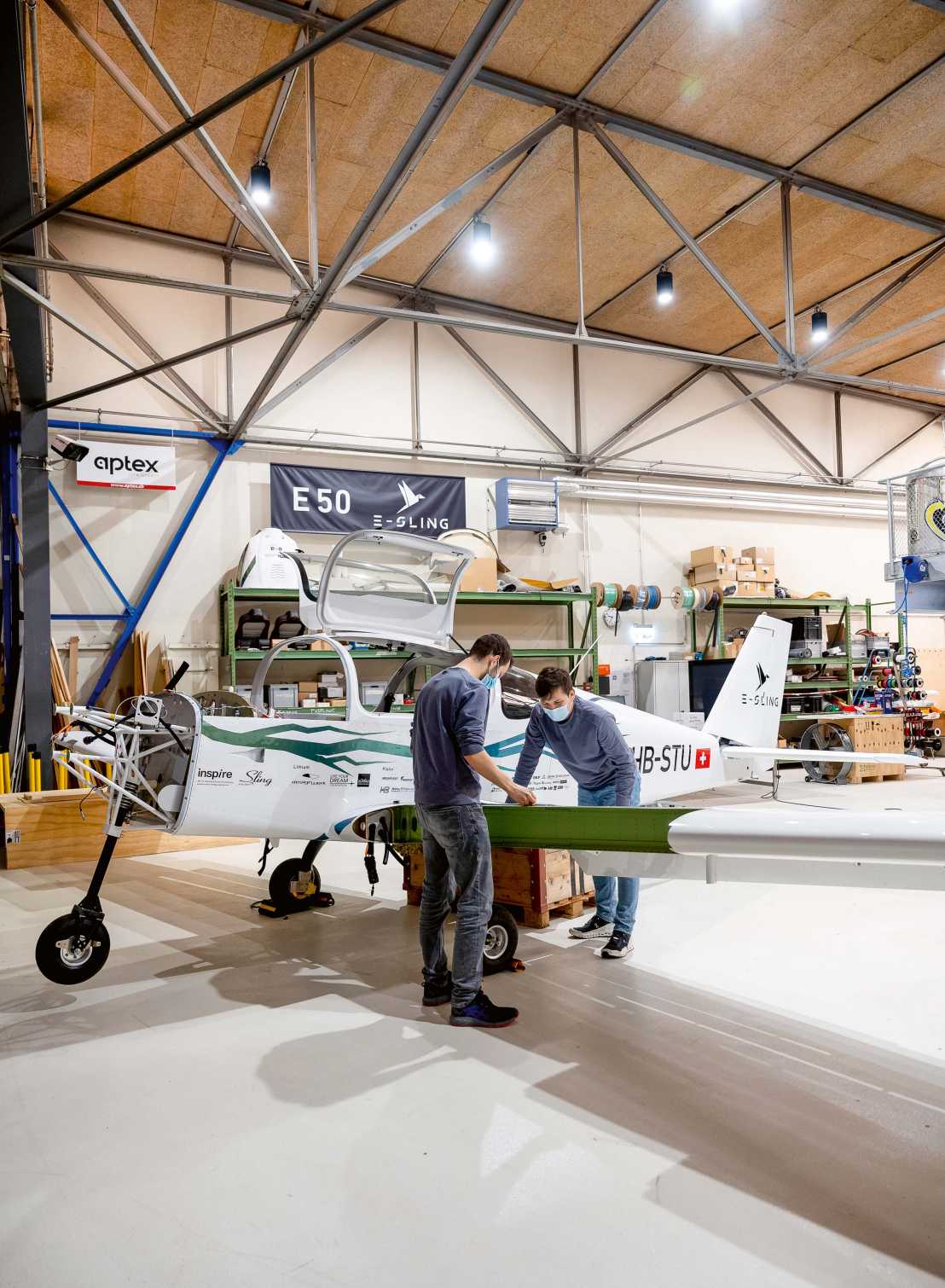
So far, they have only made sketches of the hydrogen-electric aircraft and put together a few parts. “Our goal is to get the core of the propulsion system – the fuel cell – up and running by October, which would at least lay the technical foundations for the next team,” says Robin Feuz. “We benefited so much from the previous group’s work and expertise, so we want to leave things in the best shape we can for whoever’s up next!”
Like most of their teammates, Sander and Robin are in the third year of their mechanical engineering course. They have already acquired a theoretical understanding of how fuel cells work from a lecture on thermodynamics. But this knowledge falls far short of what they would need to install a fuel cell in an aircraft, because all the elements have to be defined from scratch. That means not only selecting the right fuel cell but also configuring the cooling system and the hydrogen and air supply. “The biggest challenge is getting all those components to work together smoothly so you end up with a lightweight and inexpensive propulsion system that not only complies with all the regulations but is also airworthy,” says Sander.
At the start of the project, this topic was completely new to the team, but over the past few weeks and months they have delved deeper into the key issues, spoken to experts and even visited the Hydrogen Technology Expo Europe in Bremen. They have now acquired enough expertise to order individual parts, including the compressor that Sander pulls out of a large box to show us. Yet it’s likely to be some time before this compressor will be supplying the fuel cell with air and, together with all the other components, getting the hydrogen-powered plane off the ground. By then, it will be a new team of students making their mark in Hanger 3 at the Innovation Park Zurich in Dübendorf.
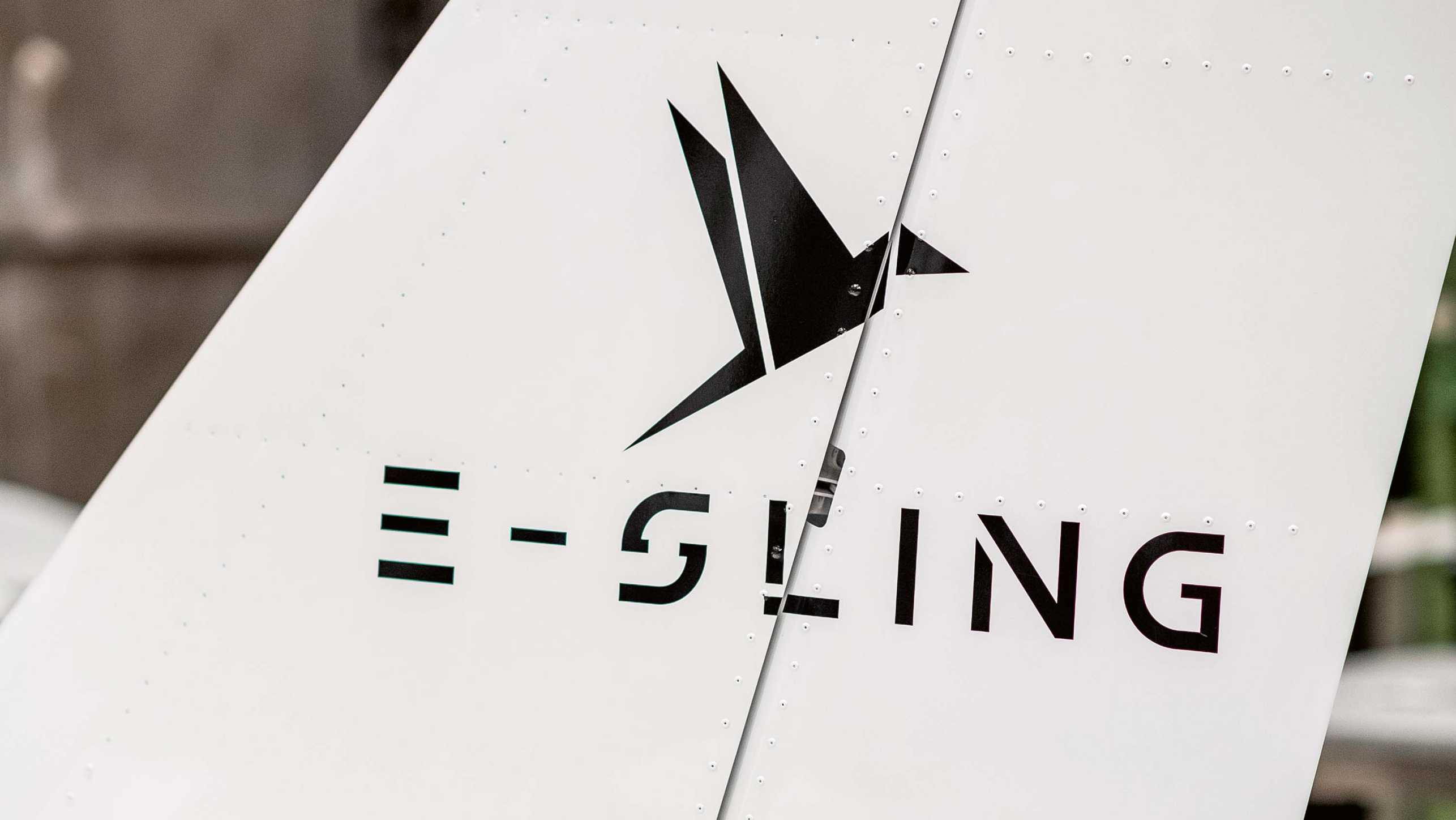
At the time of going to press, the aircraft was still on the ground. You can find the current status of the project at: external page e-sling.com/news/
Comments
No comments yet