4D Design
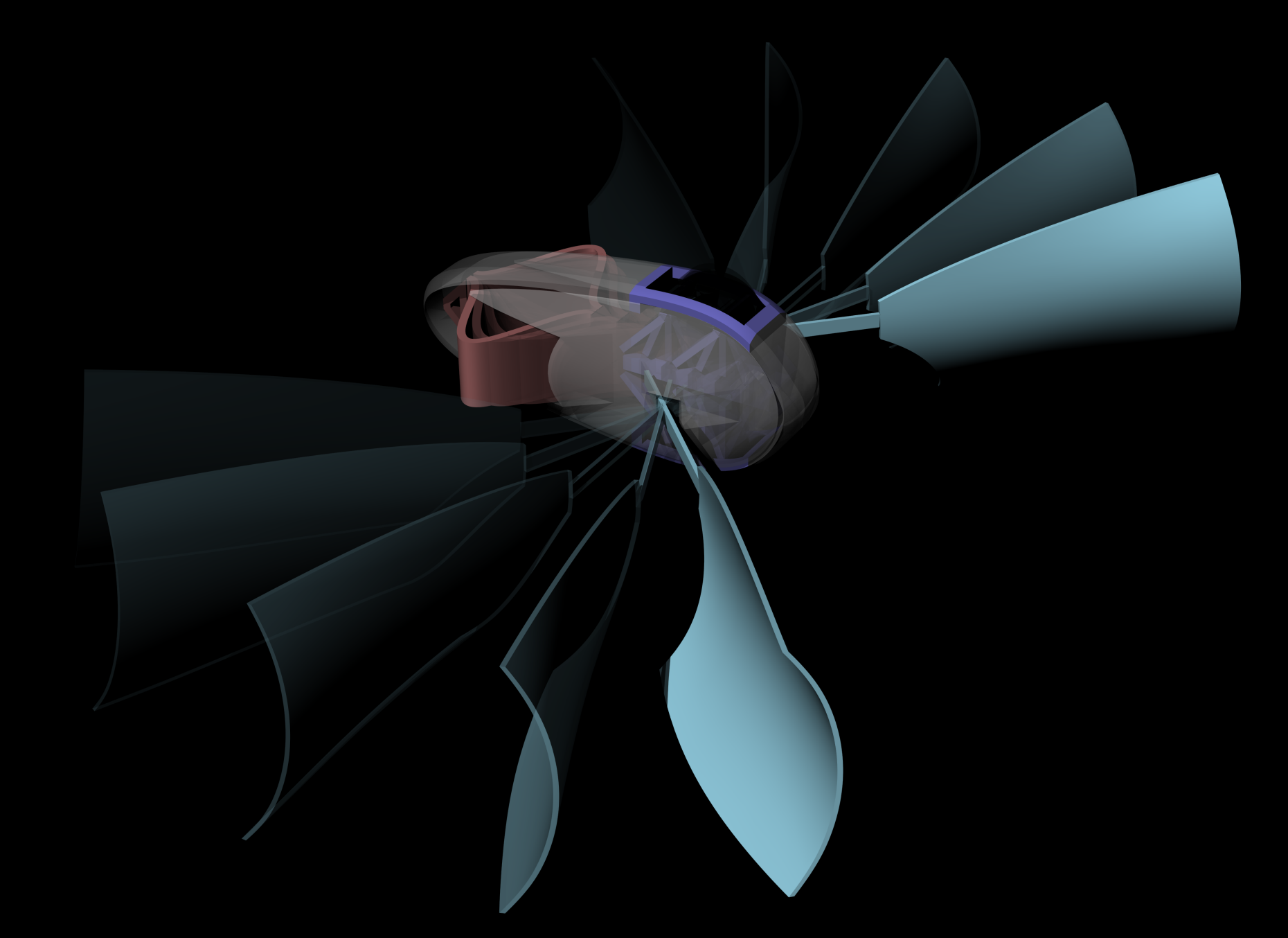
Self-propelling swimming robots and 4D design
In 2018, researchers at ETH Zurich under the direction of Professor Kristina Shea developed a new propulsion concept for swimming robots. The 3D printed polymer robot exploits temperature fluctuations in water for propulsion without the need for an engine, propellant or power supply. Now Shea and her group explore 4D Design from spare parts to space exploration.
While industry is still grasping with how best to exploit 3D printing in their businesses, ETH Zurich researchers in Professor Kristina Shea’s Engineering Design and Computing Lab (EDAC) are al-ready on to the next step: 4D Design. Today, 3D printing is revolutionizing production processes by increasing the complexity ofmanufacturable shapes and reducing the cost producing small volumes such as parts manufacturing or integrating parts to reduce assembly costs. The process also offers unprecedented opportunities for customization and personalization. At the moment, however, a much more important development is taking place: with 4D design, the functionality of 3D printed parts can be increased by using special material properties for the production of machines. Electronics, controls, heavy batteries, or conventional motors are no longer necessary.
4D design exploits 3D printing and considers not only three spatial dimensions, but also a fourth dimension - time. 3D printed “shape memory polymers” are designed and positioned in components so that over time, printed objects can change shape over time and even propel themselves in response to an environmental stimulus such as a change in temperature. 4D design is an emerging design process.
Researchers aim to design sustainable parts that can be 3D printed and self-assembling - from a flat surface to a pyramid or a more complex structure. This design concept has distinct advantages:
• Less material is required due to the flat printing
• Less transport volume is needed
• No assembly is required when putting a part into operation
• No moving assemblies or parts that can jam
Rather than using conventional actuators and controls, the polymer material itself provides a similar functionality through 4D design. 4D design paves the way for applications on land, in water and in space. Structures designed so that they can be 3D printed flat and then deployed into multiple different shapes could prove useful for deploying technologies in challenging terrain on earth or on other planets. In water, a fully 3D printed swimming robot is demonstrated that requires no battery or conventional motor so that it can be used to passively monitor the environment. Finally, in space, a 3D printed, deployable solar panel is designed to be packed small during launch and then deployed into the final shape in space.
Further information
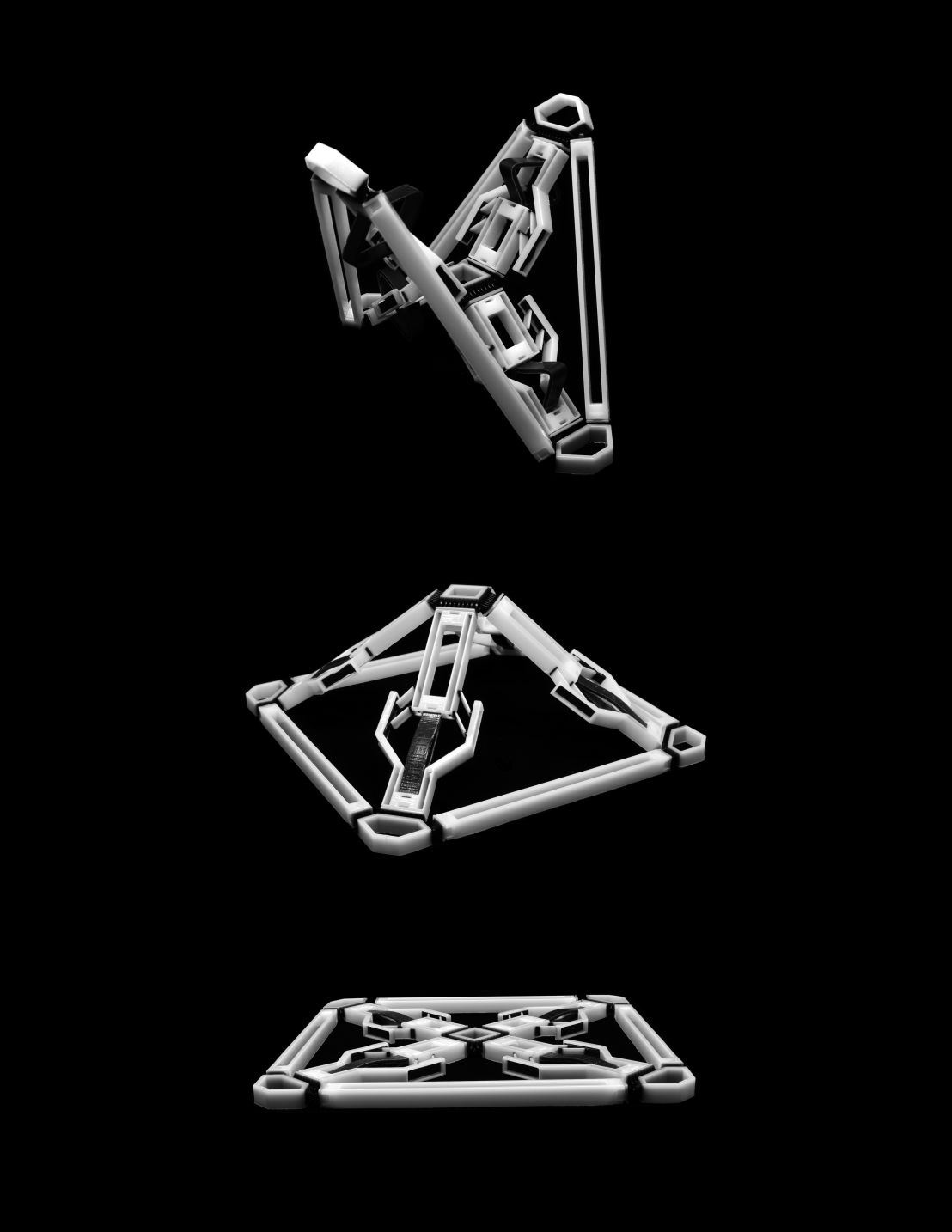
Publications/references
On Land: 4D Design of Deployable and Reconfigurable 3D Printed Structures
[1] Chen T, Shea K, “An Autonomous Programmable Actuator and Shape Reconfigurable Structures Using Bistability and Shape Memory Polymers”, 3D Printing and Additive Manufacturing, 5(2), 24 May 2018, doi: 10.1089/3dp.2017.0118
In Water: 4D Design of an Untethered Swimming Robot
[3] Chen T, Bilal OR, Shea K, Daraio C, “Harnessing bistability for directional propulsion of soft, un-tethered robots”, PNAS, 15 May 2018, doi: 10.1073/pnas.1800386115
In Space: 4D Design of a Deployable Solar Panel
Demonstrated for the first time publicly at the ETH Zurich Pavilion in Davos during the World Eco-nomic Forum Annual Meeting 2019