Ingenieure des ETH Feasibility Lab entwickeln gemeinsam mit dem IKRK eine Beinprothese, deren Verschleissteil einfach ausgewechselt werden kann. Dies erhöht die Lebensdauer. In Zukunft könnten mehr Minenopfer mit einer solchen Prothese versorgt werden.

Im Jahr 2019 wurden weltweit mindestens 5554 Menschen Opfer einer Landmine, so steht es im aktuellen Bericht der «Internationalen Kampagne für das Verbot von Landminen». Die meisten sind Zivilisten in Kriegsgebieten und fast die Hälfte noch Kinder. Über 2000 Minenopfer starben, 3357 wurden schwer verletzt. Viele der Überlebenden verloren durch die Explosion ihre Beine – oder sie mussten diese aufgrund der Verletzungen amputieren lassen. Für sie hat das Internationale Komitee des Roten Kreuz (IKRK) in Konfliktgebieten Zentren aufgebaut, in denen Menschen mit Gliedmassenamputationen mit Prothesen versorgt werden. Im Jahr 2018 erhielten dadurch 12'412 Betroffene in Pakistan, Irak, Afghanistan und vielen weiteren Ländern eine Prothese und damit auch ein Stück ihrer Mobilität zurück.
Labor für Innovation im Gesundheitsbereich
Ende 2019 kontaktierten die Verantwortlichen des IKRK das ETH Feasibility Lab mit einer grundsätzlichen Frage: Wie könnte die Lebensqualität von Prothesenträgern und -trägerinnen bei gleichbleibenden Kosten für die Prothesen verbessert werden? «Genau für solche praxisbezogenen Fragen aus dem Gesundheitsbereich sind wir da», sagt Stephan Fox, Leiter des Labs, das in der Gruppe von ETH-Professor Mirko Meboldt angesiedelt ist. «Wir wollen neue Ideen entwickeln und deren Anwendung in der Praxis in einem sehr frühen Entwicklungsstadium testen.» In Zusammenarbeit mit dem Design Technology Lab der ETH und der Zürcher Hochschule der Künste (ZHdK) begeisterte Fox für das Projekt zwei Bachelorstudierende aus den Studiengängen Maschinenbau der ETH und Industrial Design der ZHdK. Daraufhin fand Anfang 2020 ein Kick-off-Meeting in der IKRK-Werkstatt in La Chaux-de-Fonds statt.
Das IKRK hat nämlich eigene Prothesen entwickelt und eine Verteilkette dafür aufgebaut. Die Beinprothesen bestehen grundsätzlich aus zwei Teilen: einem Schaft, über welchen die Prothese am Beinstumpf befestigt wird, und einem Fuss für den Kontakt zum Boden. Die standardisierten Füsse aus weichem Polypropylen werden in verschiedenen Grössen in der Werkstätte in La Chaux-de-Fonds hergestellt. Von dort aus werden sie weltweit in Konfliktgebiete verschickt, wo lokale Mitarbeitende Minenopfer in Zentren des IKRK betreuen. Dort wird auch der Prothesenschaft produziert und an die Physionomie der Betroffenen angepasst. Die Füsse aus der Schweiz werden vor Ort an den Schaft geschraubt, justiert und mit diesem dauerhaft verschweisst.
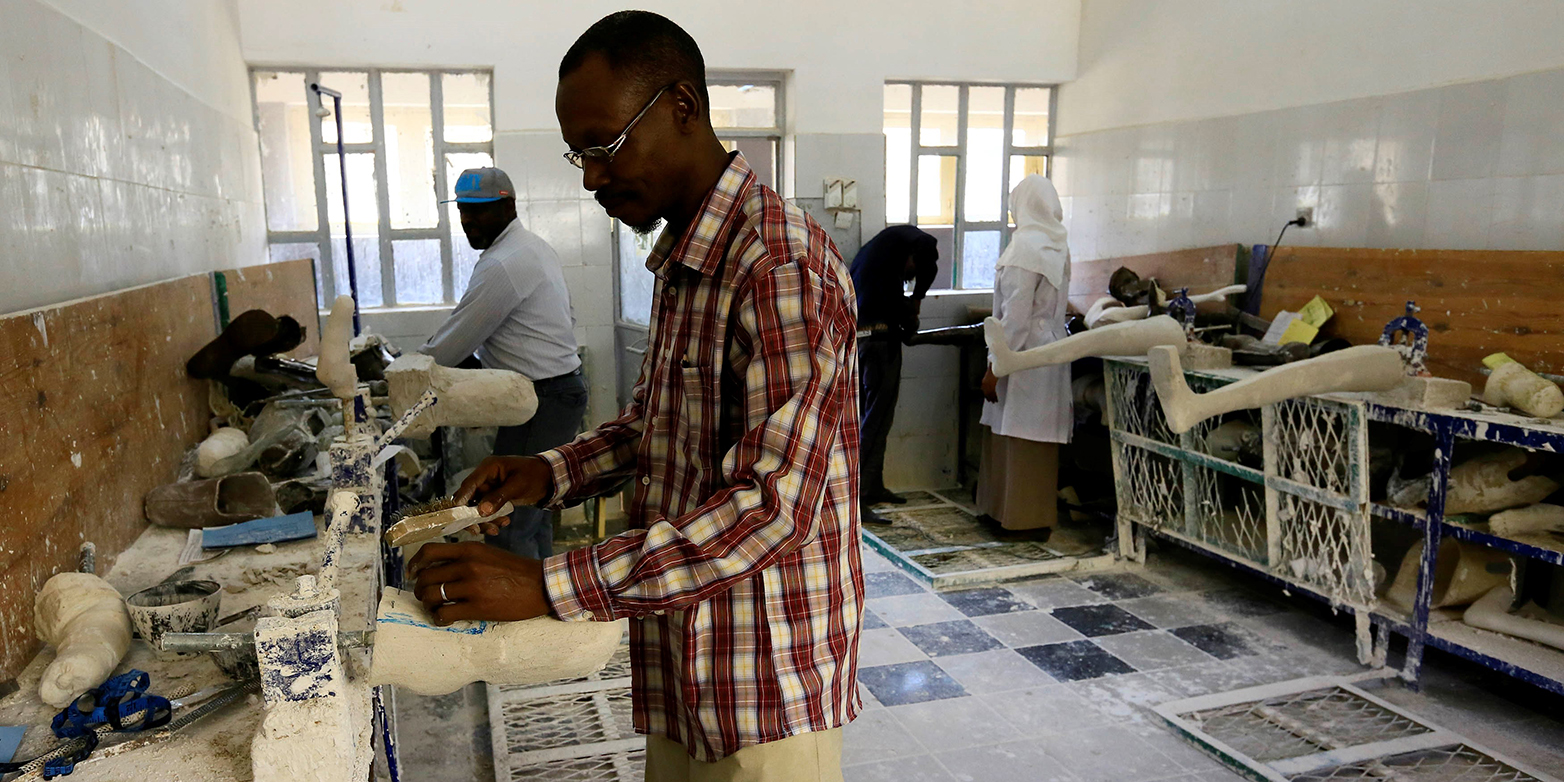
Jeder Schraube fällt ins Gewicht
Während des Kick-offs lernten Fox und die Studierenden, dass die Anpassung und Justierung von Fuss und Schaft sehr anspruchsvoll und zeitintensiv sind. Deshalb wollten sie zuerst ein neues System dafür entwickeln. «Doch wir merkten bald, dass dies viel zu teuer würde, denn fürs IKRK fallen die Kosten jeder zusätzlichen Schraube ins Gewicht», sagt Fox. Die Organisation hat den Höchstpreis zur Herstellung der Prothesen auf 250 bis 350 US Dollar pro Stück festgelegt und den gesamten Produktionsprozess daraufhin optimiert. «Unser nächster Gedanke war: Wenn das Justierungsverfahren schon so aufwendig ist, dann sollte die Lebensdauer der Prothese möglichst hoch sein.» Bei Amputationen bis unterhalb des Schienbeins (Langstumpf-Amputationen) muss die gesamte Prothese meist bereits nach einem Jahr ersetzt werden. Staub, Hitze, Feuchtigkeit und Sandstürme setzen dem Material zu. Vor allem an den Füssen ist die Abnutzung gross, weil diese die meiste Zeit mit dem Boden in Kontakt sind. Zum Auswechseln müssen die Betroffenen oft von weither in das IKRK-Zentrum anreisen.
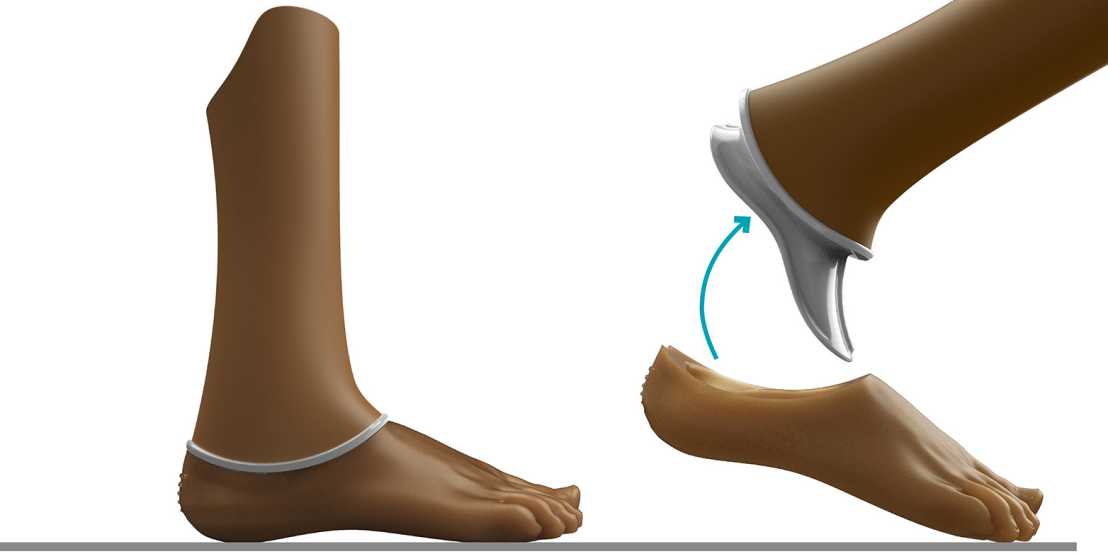
Das Team entwickelte daraufhin eine simple, aber effektive Lösung: Ein System, bei dem die abgenutzten Füsse unabhängig vom Schaft ausgewechselt werden können. Dafür gestalteten sie einen entenschnabelförmigen Kiel aus Hartplastik, der am unteren Ende des Protheseschafts befestigt wird. Anstatt die Füsse mit dem Schaft zu verschweissen, werden diese lediglich über den Kiel gezogen und temporär verleimt. Sind die Füsse abgenutzt, so könnten sie mit Wasserdampf vom Kiel abgelöst und ersetzt werden, so die Idee. «Wir machen das Verschleissteil austauschbar und erhöhen dadurch die Lebensdauer der Prothese um das Dreifache», erklärt Fox. Mit einem 3D-Drucker hat das Team sowohl den neuen Kiel als auch die angepassten Füsse fabriziert und damit die grundsätzliche Machbarkeit des Systems bewiesen.
Mehr Begünstigte mit gleicher Infrastruktur
«Das Feedback unserer Partner beim IKRK war sehr positiv», erzählt Fox. «Sie schätzen besonders, dass das neue System in die gut etablierten Werkstattstrukturen hineinpasst.» Die nötigen Anpassungen für eine grossflächige Einführung solcher Prothesen fänden vor allem in der Werkstatt im Jura statt. Dort müssten neue Spritzgussformen für die Herstellung des Kiels und der Füsse (beides in unterschiedlichen Grössen) eingesetzt werden. Die IKRK-Zentren in den Konfliktgebieten hingegen könnten mit denselben Werkzeugen und dem bestehenden Personal arbeiten, das in Hinblick auf das neue System geschult würde. Weil der Schaft nur noch alle drei Jahre ausgewechselt werden müsste, könnte das bestehende IKRK Personal rund drei Mal mehr Langstumpfprothesen herstellen – und dadurch zusätzlichen Minenopfern helfen. Das Auswechseln der Fusspartie ist viel einfacher als die Herstellung eines neuen Protheseschafts. Deshalb wären künftig auch mobile Zentren in Bussen denkbar, die in entlegenen Dörfern Protheseträger besuchen und die abgenutzten Teile vor Ort auswechseln.
Aktuell berät das IKRK darüber, wie es mit dem neuen Prothesesystem weitergehen soll. Der nächste Schritt wäre die Entwicklung von Prototypen für den praktischen Einsatz. Diese müssten anschliessend zertifiziert werden, damit sie von Betroffenen getestet werden könnten. Einzelne Normtests haben die Forschenden bereits vorweggenommen. Zum Beispiel haben sie virtuell überprüft, ob das neue Verbindungssystem stabil genug ist, damit der Prothesefuss bei Belastungen nicht abrutscht. Die Resultate waren vielversprechend und das Team geht davon aus, dass das System den Kriterien für medizinische Geräte entspricht.
Für eine globale Einführung des neuen Systems sieht Fox die grössten Herausforderungen in den teils widrigen Bedingungen vor Ort. Die Prothesen müssen Sand, Feuchtigkeit, Hitze und Kälte gleichermassen standhalten. Hinzu kommt: «Unser System muss für die Träger am Ende mindestens so komfortabel sein wie das bestehende, im Idealfall sogar noch komfortabler.» Fox hofft nun auf einen positiven Bescheid des IKRK, so dass sein Team die Entwicklung im kommenden Jahr weiter vorantreiben kann.
Kommentare
Noch keine Kommentare