Bessere Qualität durch künstliche Intelligenz
ETH-Forschende nutzen künstliche Intelligenz, um das Qualitätsmanagement bei digitalisierten Produktionsprozessen zu verbessern. In einem Experiment beim Halbleiterproduzenten Hitachi Energy konnte der Anteil fehlerhafter Produkte halbiert werden.
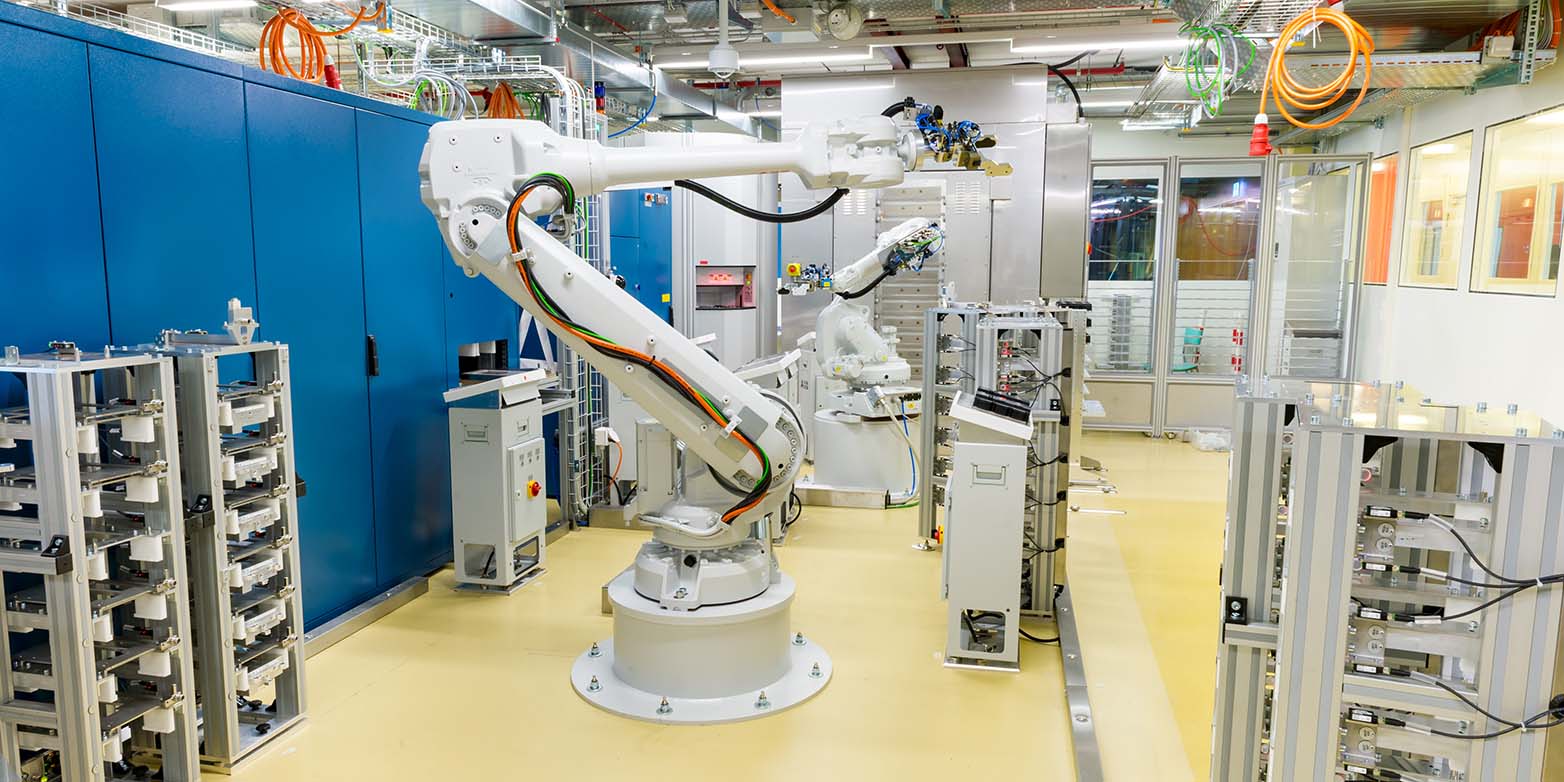
Ob bei komplexen Maschinen, Pharmaprodukten oder Mikrochips: Je teurer ein Produkt, desto entscheidender seine Qualität, um am Markt bestehen zu können. Dies gilt besonders für die industrielle Produktion in Hochlohnländern wie der Schweiz. Umso überraschender ist es, dass mangelnde Qualität im Durchschnitt weiterhin 15 Prozent der Betriebskosten in der industriellen Fertigung ausmacht. Der Grund dafür: ein oft veraltetes Qualitätsmanagement.
Die beiden ETH-Forscher Julian Senoner und Torbjørn Netland sowie Stefan Feuerriegel, der seit kurzem an der LMU München tätig ist, zeigen in einer neuen Studie auf, wie das Qualitätsmanagement bei komplexen, digitalisierten Produktionsverfahren durch künstliche Intelligenz (KI) verbessert werden kann. Erfolgreich getestet wurde ihr Algorithmus bereits in einer Hableiterfabrik von Hitachi Energy, vormals Hitachi ABB Power Grids, in Lenzburg: Die Anzahl fehlerhafter Produkte konnte in einem Experiment um über 50 Prozent gesenkt werden, was die Produktion nicht nur effizienter, sondern auch nachhaltiger macht.
Veraltetes Qualitätsmanagement
Die Herstellung komplexer, industrieller Produkte erfordert eine Vielzahl miteinander verbundener Arbeitsschritte. Um zum Beispiel Halbleiter zu produzieren, die in Computern, Zügen, oder Windkraftanlagen verwendet werden, sind zwischen 200 und 400 Produktionsschritte notwendig. Bei jedem dieser Schritte können verschiedene Dinge schiefgehen. Ist zum Beispiel die Temperatur in einer Maschine etwas zu hoch, oder der Druck in einer anderen etwas zu nieder, können Fehler einen grossen Teil der Produkte beeinträchtigen. «In der Halbleiterproduktion ist es nicht unüblich, dass die Fehlerquote zwischen 5 und 70 Prozent schwankt, da der Fertigungsprozess sehr kompliziert ist. Da steht sehr viel Geld auf dem Spiel», erklärt ETH-Professor Torbjørn Netland vom Lehrstuhl für Produktionsmanagement.
Bis anhin war es bei komplexeren Produktionsverfahren dieser Art sehr schwierig, Fehlerquellen genau zu identifizieren. Traditionelle Methoden, die in zahlreichen Fabriken weltweit zur Qualitätssicherung zum Einsatz kommen, erlaubten es Ingenieurinnen und Ingenieuren immer nur, einige wenige Parameter gleichzeitig zu untersuchen. In komplexen Produktionsabläufen werden aber mittlerweile tausende von zusammenhängenden Parametern gemessen. Wie diese interagieren und sich auf die gesamte Produktion auswirken, konnte mit traditionellen Methoden allerdings nicht analysiert werden. ETH-Professor Netland und seine Ko-Autoren haben vor dies zu ändern: «Wir wollen das Qualitätsmanagement ins digitale Zeitalter bringen. Denn die Methoden, die viele Produzenten weiterhin verwenden, sind oft bis zu 100 Jahre alt», sagt Netland.
Algorithmus identifiziert Fehlerquellen
Die ETH-Forschenden entwickelten zunächst einen Algorithmus, der die einzelnen Schritte bei der Produktion von Halbleitern imitiert. Anschliessend fütterten sie den Algorithmus mit möglichst vielen historischen Produktionsdaten, wie zum Beispiel der Temperatur oder dem Druck, die in Maschinen gemessen werden. «Auf Basis dieser Daten lernt der Algorithmus, unter welchen Bedingungen die Qualität der Halbleiter gut ist und wann es zu hohen Fehlerquoten kommt», sagt Julian Senoner, der Erstautor und wissenschaftlicher Mitarbeiter an der Professur von Netland.
Der Vorteil der auf KI basierenden Methode ist, dass man beliebig viele Faktoren und Beziehungen des Produktionsprozesses analysieren und komplexere Zusammenhänge zwischen Parametern aufdecken kann. Dadurch können Fehlerquellen systematischer und über den gesamten Produktionsprozess hinweg identifiziert werden. Gut ausgebildete Ingenieurinnen und Ingenieure in den Fabriken werden damit aber keineswegs überflüssig. Im Gegenteil: «Unser Algorithmus zeigt vor allem bislang unentdeckte Fehlerquellen auf. Wie diese aber genau behoben werden, erfordert weiterhin sehr viel technisches Fachwissen und menschliche Kreativität», erklärt Netland.
50 Prozent weniger Verlust
Um den Algorithmus zu testen, arbeiteten die Autoren mit Hitachi Energy in Lenzburg zusammen. Hitachi Energy produziert Halbleiter, die in Elektro-Fahrzeugen und Zügen gleichermassen eingesetzt werden, wie in Windkraftanlagen oder der Stromleitungen. Die historischen Produktionsdaten des Halbleiterproduzenten ermöglichten es den Forschenden, zwei Herstellungsschritte zu identifizieren, die die Qualität der Halbleiter am stärksten beeinträchtigten. Mit diesen Erkenntnissen in der Tasche gingen sie in die Fabrik, um ein Experiment unter realen Produktionsbedingungen durchzuführen.
Gemeinsam mit den Ingenieurinnen und Ingenieuren von Hitachi Energy teilten die Autoren eine Produktionscharge von 1488 Halbleitern in vier gleiche grosse Gruppen auf. Während die ersten 372 Halbleiter ohne spezifische Anpassungen produziert wurden, wurde für Gruppe zwei und drei jeweils ein Herstellungsschritt optimiert. Bei den letzten 372 Halbleitern wurden dann beide Herstellungsschritte optimiert. «Die Ergebnisse des Experiments bestätigten die Vorhersage des Algorithmus: In der Kontrollgruppe, die ohne Optimierung gefertigt wurde, war die Fehlerquote viermal höher als in jener Gruppe, die nach der Empfehlung des Algorithmus produziert wurde», sagt ETH-Professor Netland.
Hitachi Energy setzte die Empfehlungen der ETH-Forschenden anschliessend bei einer anderen Produktvariante um und senkte den Anteil fehlerhafter Produkte um über die Hälfte. Für den Halbleiterproduzenten aus Lenzburg ist der Algorithmus der ETH-Forschenden damit ein wichtiger Vorteil, der das Qualitätsmanagement entscheidend und nachhaltig verbessert.
Auch für andere Branchen relevant
Doch lassen sich diese Ergebnisse auch in anderen Industriezweigen erreichen? «Damit unsere Methode gute Ergebnisse erzielen kann, sind sehr viele Daten zur Herstellung notwendig und dies erfordert hochgradig digitalisierte Produktionsprozesse», erklärt ETH-Forscher Senoner. Aktuell, so die Autoren, seien diese Bedingungen vor allem in der Pharmaindustrie, der Chemiebranche oder in der Kunststoffherstellung gegeben.
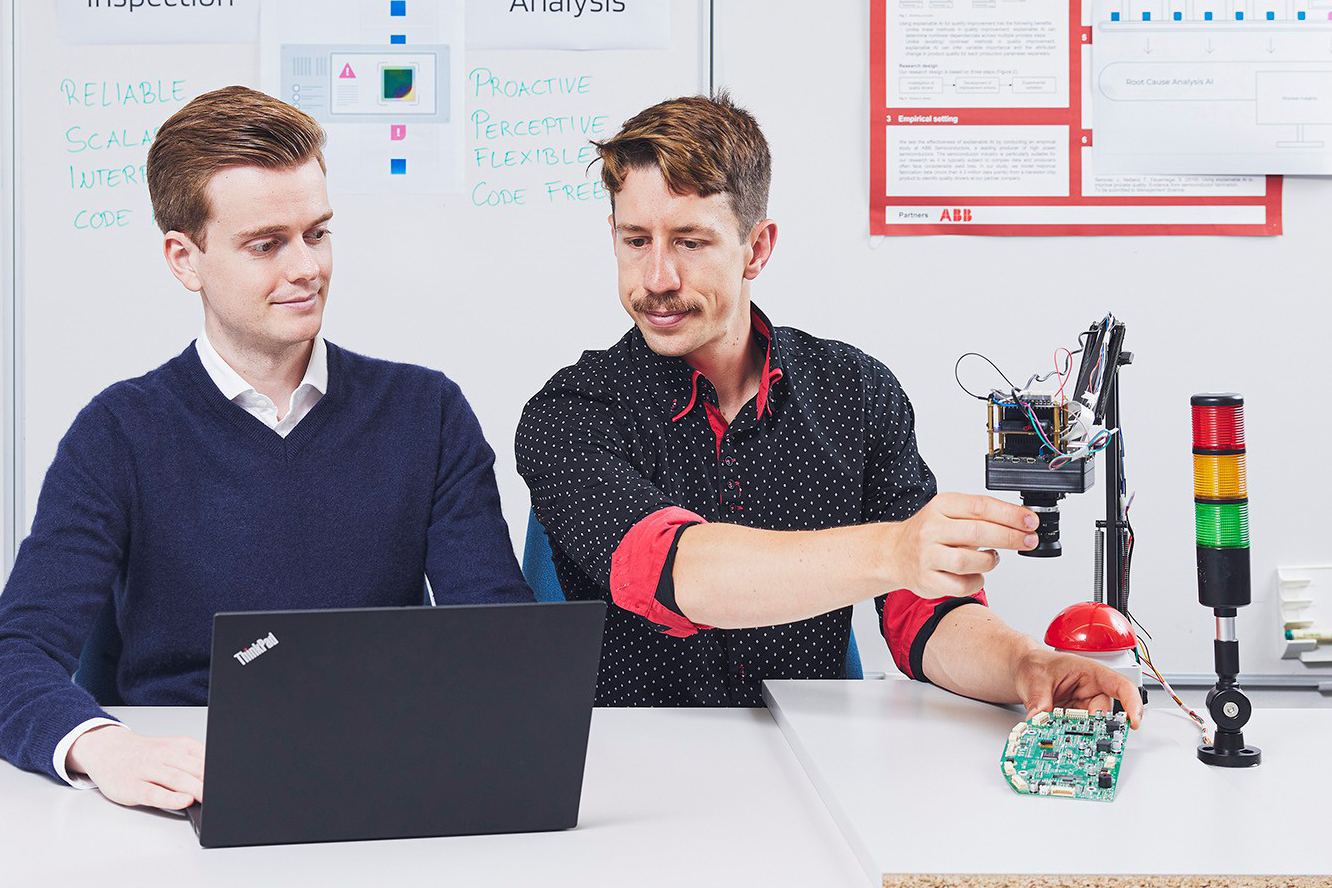
Mit der zunehmenden Digitalisierung von Produktionsprozessen sollte der Algorithmus der ETH-Forschenden aber mittelfristig auch für andere Branchen interessant werden. Um das wirtschaftliche Potential von künstlicher Intelligenz im Qualitätsmanagement zu nutzen und die Technologie möglichst breit zugänglich zu machen, gründete Erstautor Julian Senoner gemeinsam mit ETH Pioneer Fellow Bernhard Kratzwald daher das ETH Spin-off externe Seite EthonAI.
Literaturhinweis
Senoner J, Netland T, Feuerriegel S (2021). Using explainable artificial intelligence to improve process quality: Evidence from semiconductor manufacturing. Management Science, publiziert online: 9 Dezember 2021. DOI: externe Seite 10.1287/mnsc.2021.4190
Kommentare
Noch keine Kommentare